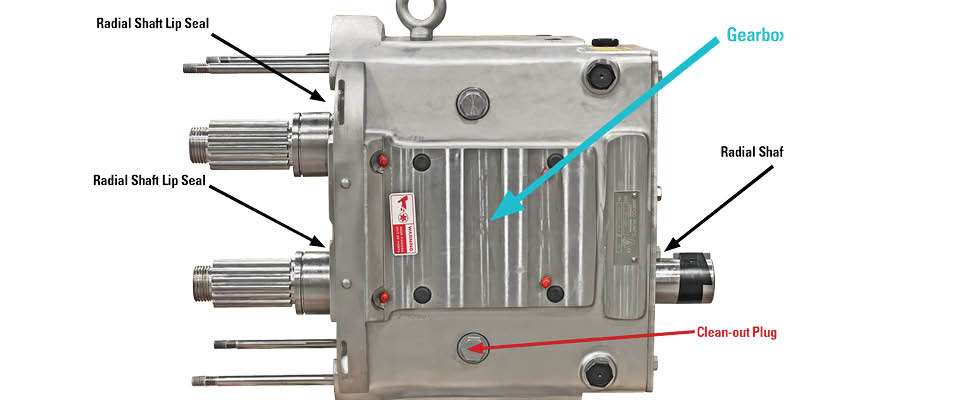
Sanitary circumferential piston pumps (CPPs) are a mainstay in food processing and packaging due to their ability to handle high-viscosity products or anything above 1000 centipoise (cp). Keeping these pumps running efficiently while also protecting product quality can be a challenge at times. Regular maintenance and inspection are required to ensure proper function and avoid product contamination. Before maintenance can begin, it is best to understand what these pumps are all about and how to identify commonly seen modes of failure.
The traditional CPP design consists of two distinct sections or compartments:
- workhead (the fluid or food end)
- bearing frame (contains all the drive components)
Between them run two shafts and two rotors—one rotor for each shaft. The motion of these rotors is coordinated by timing gears, which is why the bearing frame is often called the gearbox.
6 Maintenance Recommendations
Proper maintenance techniques and attention given to the gearbox and internal parts will extend pump life and reduce the occurrence of wear to other parts of the pump. Most abnormal wear and CPP failures begin at the pump gearbox. Six maintenance recommendations to
consider include:
1. Check for signs of premature wear in three key areas.
CPPs are heavily relied upon in conditions of high pressures and viscosities. This process relies on tight clearances between the rotors and the housing. Each rotor’s shaft bearings are therefore critical in controlling shaft runout (its deviation from a true circular motion), especially during heavy operation. These pumps are commonly outfitted with taper bearings because they have higher load carrying capacity versus ball bearing types. While ball bearings perform better at high speeds, the taper bearing allows better control of axial and lateral loads. Checking regularly for wear in these three areas helps ensure more efficient operation and timely replacement before breakdowns occur:
Shaft movement: With the body removed, push and pull on the shafts. Check for any shifting, axial and laterally. Any movement is a sign the bearings are beginning to fail. Replace the bearings immediately to eliminate the high cost of worn workhead components.
Shaft backlash: With the body removed, turn shafts left and right. There should be zero backlash. Any backlash detected can indicate bad gears or that the gearbox has no oil.
Workhead wear (rubbing): Tight clearances between the rotor and body are critical for the high efficiency of pumps, but maintaining that clearance is essential. Any play in the shafts needs to be addressed to prevent damage. Depending on the product being pumped, a small amount of wear may be acceptable, but a loss of efficiency will be present. If the rubbing has caused extensive damage, pump replacement is necessary. Remanufacturing may be an option for certain models and types of pumps.
2. Inspect the gearbox for signs of water migration.
Water can enter the CPP gearbox system in several ways. One is from incidental spray near or at the shaft seals. This is the second leading cause of failure in food processing plants. These radial shaft seals are located at the front and rear of the gearbox where the shafts protrude.
Less obvious water ingression points can come from shaft grooving. This is caused by aged or worn radial shaft lip seals, which allow fine particulates to collect and create grooves in the shaft. This seemingly small issue can become an open door for contamination into the gearbox during washdown. To correct, a speedi-sleeve can be used to restore the sealing surface.
Condensation is another source of water ingression that can occur and is caused from a variety of environmental conditions, including product and room temperature changes.
3. Use care when employing high-pressure washdown around plugs and shafts areas.
CPPs may come fitted with plugs or gasketed plug hardware to prevent migration of water and other
environmental contamination. Although most are rated for washdown duty, high-pressure spray can loosen plugs, dislodge breather protection devices or find entry into the gearbox around shaft openings.
4. Open clean-out plugs to allow any contaminates to drain.
Frequently releasing contaminates can aid in pump longevity. One way is by reducing the risk of corrosion and rust. Another is by optimizing the pump for the specific product.
Lastly, it helps avoid seal degradation and potential risk of bacteria growth. If the pump uses both oil and grease, draining periodically will mitigate cross-contamination.
5. Regularly add new grease (even minimally) and clean out old or excess grease.
Bearings and other rolling elements within the CPP are in a constant battle with the forces of friction. That is because rolling and sliding friction are responsible for enabling the majority of the pump’s workload. Without proper lubrication, these two forces can easily cause bearing failures in CPPs.
6. Consider potential equipment upgrades.
To extend the life of pumps, users may want to utilize:
- additional shielding for extra protection against water ingress during washdown
- upgraded industry parts offerings for additional protection, such as radial shaft seals, bearing retainer guards and gasketed clean-out plugs
Understanding these best practices and important areas of maintenance will help ensure the efficiency, productivity and extended operational life of a CPP.