A Mississippi River levee, an Indiana water plant and an Ohio municipality take advantage of ease of installation and significant energy savings—as much as $2 million up front.
03/17/2016
In recent decades, engineers contemplating variable speed pumping for their systems often only consider a variable frequency drive (VFD) setup. Some planned installations, however, can be technically or economically daunting. In such cases, an eddy current drive might be a more desirable solution.
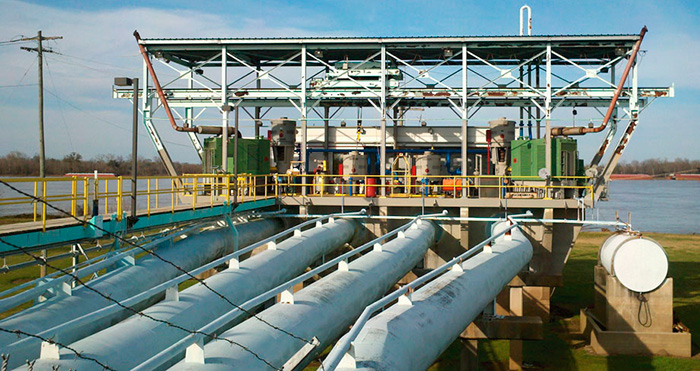
1. Installation at a Mississippi River Levee
A freshwater supply district in Louisiana operated a pumping station originally built in 1954 with three pumps. A fourth pump was added in 1960. The pumps draw water from the Mississippi River and discharge on the other side of the levee into the adjacent bayou. All four of the vertical axial flow pumps were equipped with a constant-speed electric motor drive, with two having an alternative to operate the pumps with diesel engines through a right-angle gear when electric power failed. In 2008, a consulting engineer and the district conducted a study to assess the condition and future use of the aging pump station. The pumping station was evaluated to determine whether it should be used as a continuous-duty pump station or as a backup. The district and its engineering firm decided to refurbish the pump station with two new pumps and to retain the engine/electric drive pumps. The station was designated for continuous duty. Fluctuation of the river level and the resultant effect on total dynamic head (TDH) and flow capacity suggested that variable speed drives should be considered for the two new pumps. The new pump required 300-hp, 2,400-volt motors for the rated design point of 45,000 gallons per minute (gpm) at 17.1 feet TDH at a nominal speed of 490 revolutions per minute (rpm). However, expected operating demand suggested that the pumps would operate at 85 percent speed (416 rpm), reducing the pump's brake horsepower (bhp) requirement to 111 hp, or 83 kilowatts (kW). The engineer considered and compared eddy current drives and variable frequency options for this 85 percent average operating speed (see Table 1). Annual excess energy consumption was calculated on the basis of continuous operation—24 hours for 365 days (see Equation 1).


2. Drive Replacement at Indiana Water Plant
In late 2014, a Midwest consulting engineer was asked to evaluate options and specify equipment to replace 35-year-old variable speed eddy current drives at a water plant in southern Indiana. The original equipment included two 200-hp, 900-rpm eddy current drives and one 500-hp, 900-rpm eddy current drive that controlled vertical turbine pumps. Motor voltage was 4,160. In recent years, one of the 200-hp units had been replaced by a 480-volt motor and a VFD operating through a transformer to enable operation from the 4,160-volt source. The user had experienced good reliability and service life from the eddy current drives and was equally satisfied with the newer VFD that replaced one of the eddy current units. They were, however, eager to integrate the control of the new variable speed equipment with their central control system using Ethernet communication. The engineer compared new eddy current drives to VFDs for each of the ratings on the basis of first cost, installation considerations and operating cost expectations. The user elected to replace the 200-hp eddy current drive with a 480-volt VFD, similar to the arrangement implemented some years earlier on the other 200-hp pump. However, the 500-hp unit was considered too much power to be operated at 480 volts, and they chose to keep that system at 4,160 volts. Based on this consideration, the VFD option would have cost considerably more for the equipment and would need more space than was conveniently available. The 500-hp unit was replaced with a new eddy current drive and new drive motor. The digital exciter/controller was supplied with an Ethernet Internet Protocol interface capability that was easily integrated into the user's central control system.3. Drive Upgrade at Ohio Municipality
A large Ohio municipality engaged a consulting engineer in 2012 to explore options at its water pumping station. This station was originally equipped in 1976 with two 1,250-hp, 514-rpm vertical eddy current drives with synchronous drive motors operating at 4,160 volts. Although they operated satisfactorily for 35 years, they began to experience overheating in the exciter/controller cabinets. Temporary air-conditioned cooling air was implemented to keep the controllers operating while a permanent solution was studied and implemented. It was originally assumed that the eddy current units would be replaced by VFDs. However, the engineers soon learned that new VFDs would occupy much more space than available at the aging facility. The harmful effects of heat were also a concern. The existing equipment was already in danger of failure because of the need to operate in ambient temperatures of 100 degrees F. New VFDs confined to a relatively small room would be in danger of overheating from their own heat discharge in such conditions. Furthermore, the engineers feared that this expensive new solution might last only a decade or so before needing significant repair or complete replacement at even more expense. They chose to replace the aging eddy current drives in kind with new drives and induction motors. This solution was significantly less expensive on a first-cost basis and was a proven solution. The eddy current drive losses are successfully absorbed by the air in the motor room floor without the need for air conditioning, and the new controllers are rated to operate safely below their maximum rating with a substantial thermal margin for the electronics. This solution was estimated to save the client about $2 million in initial installation costs.
To read more Motors & Drives articles, go here.