First of Two Parts Industry estimates assert that 50 percent of all electricity usage and up to 70 percent of electricity usage in industrial plants is the direct effect of the energy used by motors.1 In the petroleum and chemical industry, average downtime costs $87,000 per hour.2 Given that the initial cost of a 60-horsepower motor, for example, is less than $6,000, the reliability of motors is much more critical than the initial cost. This series discuss the two most frequent causes of motor failures: bearings and windings. It also identifies some steps that motor manufacturers and motor users can take to reduce downtime and increase reliability and motor life. Many end users specify a certain L10 bearing life in an attempt to ensure that their motor will have a long bearing life, which implies a long motor life. Institute of Electrical and Electronics Engineers (IEEE) 841 also specifies a required minimum L10 life. Requiring an L10 life (within reason) may help ensure long bearing life, but other parameters are also necessary. L10 as defined by American Bearings Manufacturers Association (ABMA) is a measure of bearing fatigue life, with the assumption that other critical aspects such as operating temperature, fit and lubrication are adequate. In essence, it means that under ideal conditions, 10 percent of bearings will fail because of metal fatigue in service conditions with ideal operating conditions. In practice, most bearing failures are not related to metal fatigue. These failures are usually caused by contamination, vibration, heat, too much or too little lubrication, or other environmental factors. Keeping a bearing isolated from the environment, both outside and inside of the motor, is a good first step to protecting it from contamination. A close running fit between the end shield and the shaft, along with a recessed slinger or labyrinth seal, can help keep contaminants out of the motor and the bearing from the outside. Keeping grease inside the bearing cavity and outside of the internal area of the motor is also important. Although motor bearing greases are selected to be compatible with winding materials and insulation, in service grease contamination on the windings will collect dust and debris, which is often electrically conductive and can lead to degradation of the insulation system. A close running fit between the motor bearing cap and the shaft helps ensure that contaminants arising inside the motor do not migrate into the bearing cavity. A further improvement can be created by having a bearing cap gasket and a rabbeted closely machined fit between the bearing cap and the end shield. A labyrinth seal can also increase protection.
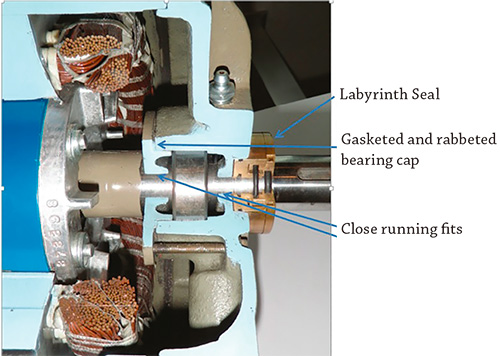
Lubrication
Lubrication is the second issue to generate premature bearing failures in motors. Over-lubrication and under-lubrication can both cause bearing failures. The motor manufacturer's installation manual should be consulted for frequency of lubrication, amount of lubrication and type of lubrication.
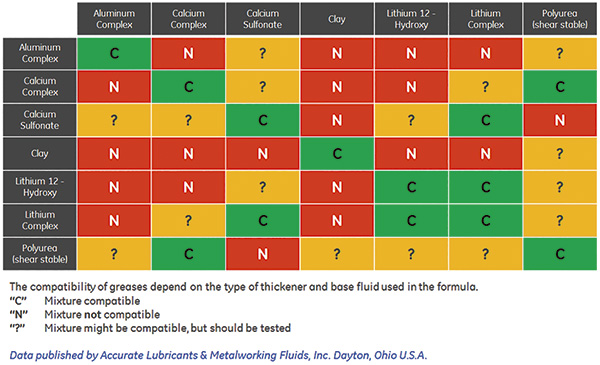
Vibration
High vibration can be a cause of bearing failures in motors as well. Petroleum and Chemical Industry Committee (PCIC) Paper No. PCIC-2005-9 states that a 50 percent reduction in vibration can result in a doubling of bearing life. Specifying low motor vibration can greatly increase the motor bearing life. The National Electrical Manufacturers Association (NEMA) standard vibration level for 140-449 frame motors is 0.15 inches per second. The IEEE 841 committee recognized low vibration as a way to increase bearing life, and they specified a level of 0.08 inches per second, roughly half of the NEMA standard. Some motor manufactures are able deliver motors with overall vibration levels of 0.04 inches per second. The overall vibration level of the motor should be a strong consideration where maximum reliability and uptime is desired. Low vibration can also increase the life of the bearings in the pump and the life of the pump seal. Specifying a maximum of 0.04 inches per second of vibration should make bearing life seven times longer according to the PCIC paper. Part 2 of this article, which will appear in Pumps & Systems June 2015's cover series, will discuss winding failures, another common cause of motor failure. References- http://www.reliableplant.com/Read/25199/methods-optimize-electric-motor "Methods to optimize electric motor efficiency"
- http://www.reliableplant.com/Read/22766/test-methods-motor-reliability "The impact of condition on motor efficiency and reliability
- IEEE Petro- Chemical Paper PCIC-94-01
- http://www.acculube.com/lubricant-acculube-compatibility.html Acculube Compatibilty Chart for Commercial Greases