02/24/2014
First of two parts. Read part 2 here.
Prior to starting any new program, financial justification must be made. This column explains how to justify projects using readily available plant production data.
I follow two rules for any process improvement:
- If end users do not measure it, they cannot improve it.
- If operators/end users do not know how much a process costs, they cannot maximize its profitability.
Improvement Program Objective
The objective of a system improvement program is to have the same attention to detail on improved pumped system profitability as is expended in increasing total plant profitability. Within a typical industrial plant, 20 percent to 50 percent of the power consumed is for pumping applications1, and these systems have an average efficiency of less than 45 percent.2 Is that sufficient incentive to consider improving pumped systems? In the column from January 2014, the plant saved money by improving system operations, but the major problem with that application was deciding what needed to be improved. To demonstrate how to determine the value of implementing a pump system improvement program, we will look at a typical industrial plant in the Northwest.Plant Case Study
In 2005, an industrial process plant was scheduled to operate for 340 days with 25 days for planned shutdowns (allowing the plant to operate 93 percent of the year). Based on 2005 operating records, the plant operated for 7,440 hours (85 percent uptime). During that time, it produced 138,500 tons of products. Based on tons produced and operating hours, the production rate was 18.6 tons per hour, and revenue was $72,000,000. Using the plant’s financial data, along with the 2005 production numbers, operators determined the revenue, expense and profit numbers per ton of product, as outlined in Table 1.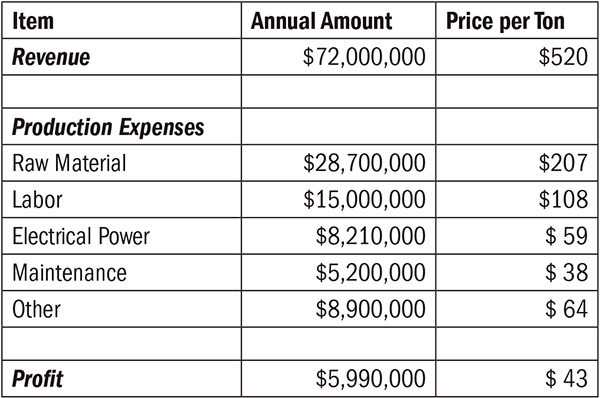
Click here to read part 2 of this article.
References
- Tobias Fleiter, Wolfgang Eichhammer, Joachim Schleich. “United Nations Industrial Development Organization: Energy efficiency in electric motor systems: Technical potentials and policy approaches for developing countries,” Working Paper 11/2011.
- Erkki Jantunen, Kirsi Vaha-Pietila & Kimo Pesonen Technical Research Center of Findland, Manufacturing Technology. VVT Symposium 172, Comadem 1997, “Expert System for the Diagnosis of the Condition and Performance of Centrifugal Pumps.”
- “U.S. Industrial Motor Systems Opportunities Market Assessment,” U.S. Department of Energy, Oak Ridge National Laboratory, Xenergy, Inc., December 1998.
The Accuracy of Estimates
The financial justification for starting a pump system improvement program uses estimated data. The accuracy of any estimate is subject to question. This sidebar discusses the assumptions made and their validity for the estimates. The percent of power going into the motors that drive pumps is based on the design load on the motor control centers and switchgear. These numbers may be greater than the actual numbers because of the design margin used when sizing electrical loads. However, if the same magnitude of design margins for all electrical load calculations are assumed, the percentage of pump power to total power should hold true. When estimating maintenance savings, the same percentage is used as that of power savings. One may question the validity of basing the maintenance savings as a function of the power savings. However, pumped systems are typically oversized. Because of this, the following logic path describes how energy savings and maintenance savings are closely related:- Most pumped systems have a design margin used in pump selection, resulting in oversized pumps.
- Oversized pumps produce greater head than required by the system.
- Excess head requires additional electric energy to drive the pump.
- Excess energy increases the hydraulic energy of the process fluid.
- To control the system to a set value, a control valve must remove the excess fluid’s energy, resulting in heat, noise and vibration. This causes increased wear and tear on the components and increased maintenance costs.