The facility’s variable speed electro-mechanical drive offered a compact, convenient solution that was energy-efficient.
Sulzer
01/05/2017
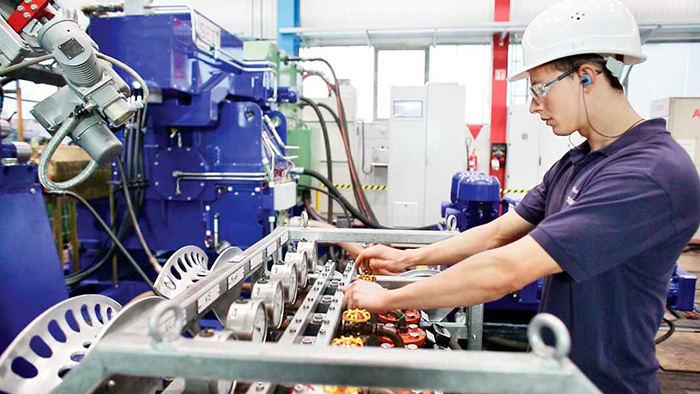
Innovative Speed Control
A gas-fired cogeneration plant located within a refinery in Germany used a boiler feedwater pump to provide 1,000 cubic meters per hour (m3/h) (4,400 gallons per minute [gpm]) of water, with a head of 1,355 meters (m) (4,450 feet). The pump was set up at a fixed speed, operating at 2,980 revolutions per minute (rpm), and required a 4.1-megawatt (MW) (5,500-horsepower [hp]) motor. Since the pump’s installation, the user’s production cycle had changed significantly, and the pump needed to run on partial load because of changes in power demand. To meet the variable system requirement of 500 m3/h (2,200 gpm) to 1,000 m3/h (4,400 gpm), the power plant used a valve at the discharge to break down pressure and throttle the flow. This meant that the energy exerted to develop the pressure was wasted. To improve the feed pump’s efficiency, the facility had to modify its operating range by configuring a speed control mechanism..jpg)
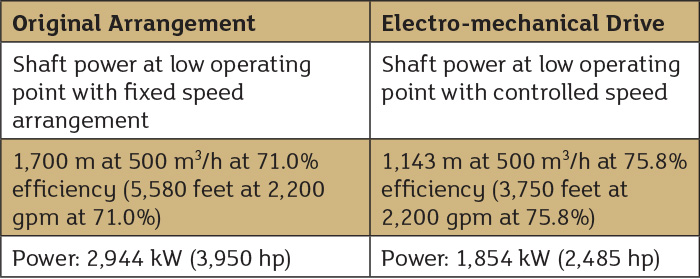