Even 1,000 miles away, these devices allow operators to work on the 9/11 Memorial with confidence.
Meg-Alert, Inc.
07/07/2017
To commemorate those who died at New York City’s World Trade Center on September 11, 2001, a memorial entitled “Reflecting Absence,” was erected. The site consists of a 16-acre plaza with 400 trees that surround two recessed reflecting pools. Each pool is close to an acre, and they are in the footprints of the Twin Towers. Both reflecting pools hold 600,000 gallons of water, and they are the largest man-made waterfalls and reflecting pools in the world.
Waterfall Challenges
The contractor chosen by the architects, Delta Fountains, faced a series of challenges from the start. The reflecting pools required massive plumbing, pumps, filters, water chemistry tanks and precision automation controls to keep everything operating smoothly 24/7 throughout New York City’s four seasons. The memorial challenged the contractor’s engineers to design a method to keep the water in the fountains flowing in clear streams from a 29-foot fall, while maintaining the required reflective and acoustic properties year-round, no matter the weather (see Image 1).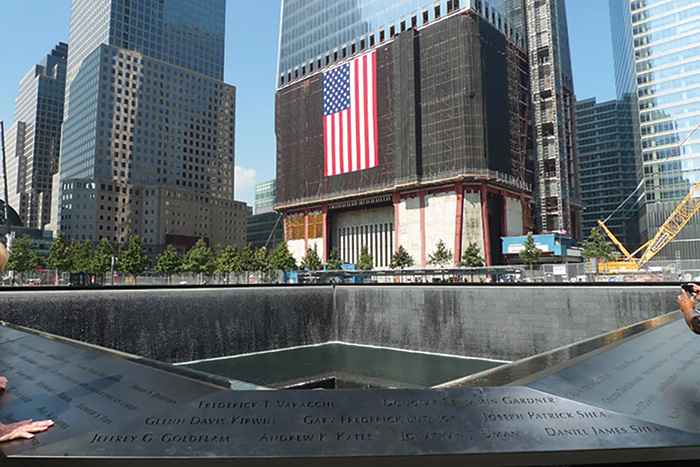
Fountain Equipment Design
Delta Fountains called on Siemens to provide them with sophisticated automation and control systems, having two levels of redundancy, to remotely operate and monitor the two memorial fountains. Multiple controllers were installed to provide the precision control required for the fountain’s critical functions. Variable frequency drives (VFDs) with additional control units were chosen to provide precision flow control for the powerful pumping system needed to transport the water in two applications, circulation and cascade. The VFD systems included the motor protection and pilot devices necessary for control and annunciation of the pump systems, while also providing an energy cost savings by keeping the pump motors operating at optimal speed at all times. The pumping system for each fountain includes eight Flygt/Xylem 480 volt, three phase, 12-inch, 60 horsepower, vertically installed, dry-pit submersible centrifugal pumps used to provide the water circulation (See Image 2). Combined, they have the ability to deliver up to 32,000 gallons of water per minute to each fountain. The vertical cascade of the waterfalls is powered by four additional submersible pumps, while four more dry-pit electrical submersible pumps take care of the stormwater drainage for each fountain.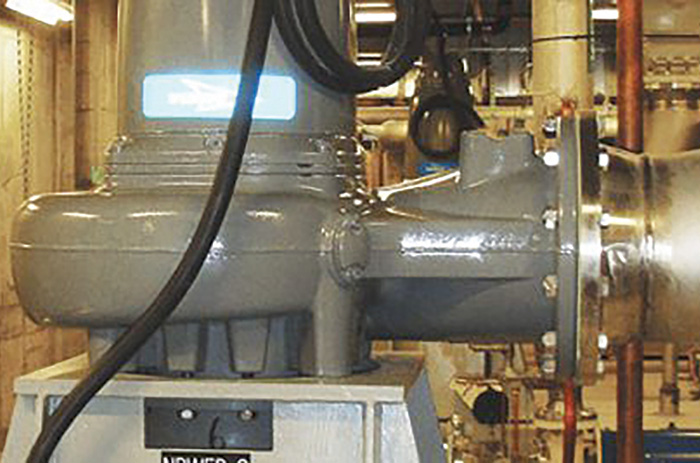
Remote Pump Operating & Monitoring Problem
The mechanical rooms housing the critical water pump systems are 50 feet below plaza level, directly beneath the pools. The contractor’s engineers needed to find a method to safely start and stop these pump motors from their remote location in Florida. At any given time, the pumps could be exposed to moisture or water leakage, which is a common cause of electric pump motor failures.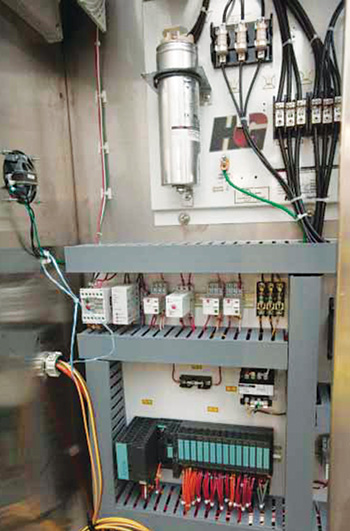
AIRT’s Provide Solution
The solution was to install automatic insulation resistance testers (AIRT) on each of the 32 total memorial pumps to continuously test and monitor the insulation resistance (I/R) condition of the motors whenever they are offline (see Image 3). The status of the I/R test would then be sent through the programmable logic control (PLC) system to the contractor’s operators in Florida, which would allow them to determine if a motor was safe to start or if it required maintenance first. The AIRT system would also have the capability of locally preventing the motor from being operated in the event the insulation readings were below a safe level, to ensure a motor failure could not occur on start up. Performing this type of I/R testing manually before every startup was not an option because it was considered both dangerous and impractical given that there were no maintenance personnel on-site daily to perform this type of testing.AIRT Custom Design
The contractor and the control systems supplier requested the AIRT manufacturer modify their units to provide the motor’s real time I/R readings on a megohm meter mounted on the door of the control cabinet. In addition, they needed to the unit to send an I/R alarm status condition signal to the PLC system and also lock out the motor start circuit locally. The particular compact model AIRT chosen for the project did not have all of these features, but the manufacturer was able to custom design the AIRT units to meet all their needs.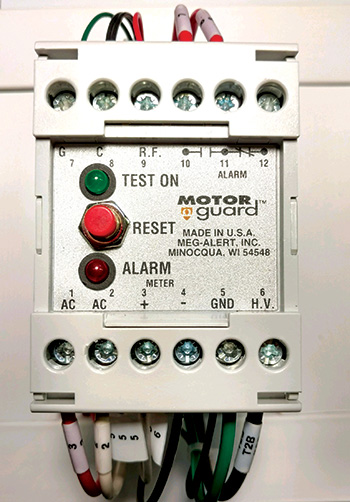
How the AIRT System Works
The AIRT systems are permanently mounted inside the motor control cabinets, and they sense when the motor is offline through a contact signal from the motor starter or the VFD (Image 4). Because these pump motors are powered by a VFD system, an output isolation contactor (OIC) needed to be installed between the VFD and the motor to isolate the motor circuit during the I/R testing. It should be noted that the AIRT testing voltage will not harm the VFD circuitry. The OIC is required because the VFD has internal leakage circuits that will skew the test results and would cause a false low alarm. Whenever the motor is offline, the AIRT continuously injects a current limited nondestructive 500-volt direct current (DC) test signal into the windings and then measures any leakage current from all three phases and the motor cables to the ground. The 500-volt test level is essential for proper I/R testing and meets the minimum testing voltage required by IEEE, ASTM, ABS and ANSI/NETA standards for these motors.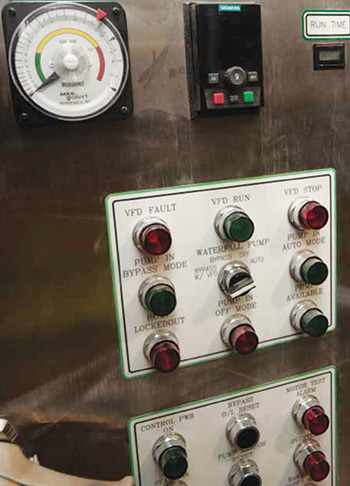