I am often asked why a system is not operating properly. In many cases, I have limited operational experience with the specific user’s fluid piping system. But by breaking down the system into the pump, process and control elements, one can quickly understand how it operates. This month’s column will look at a crude oil desalination system used to remove water and various minerals. Figure 1 provides a piping schematic of the system. This system mixes water with the crude to remove contaminants before sending to the flash and separation towers. The crude is preheated and water extracted from the second stage is added to create a mixture that is run through a mixing device before entering the first desalting unit. The first desalter separates the oil from the brine and sends the brine effluent for treatment and the cleaned crude to the second stage, where the process is repeated.
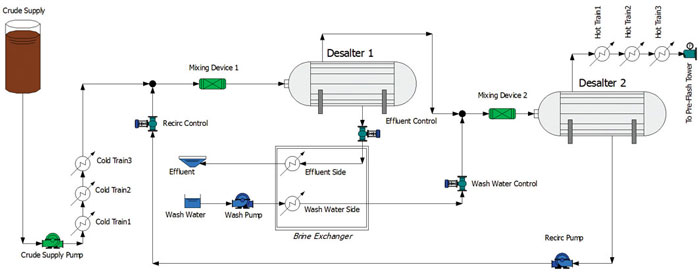
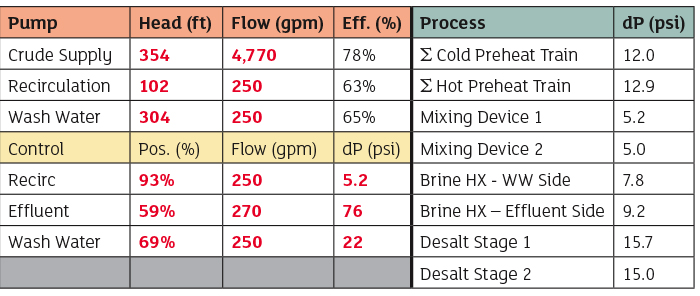
.jpg)