Pumping systems consume a significant portion of global electrical energy, accounting for nearly 20 percent of the energy used by electric motors and 25 to 50 percent of the total electrical usage in certain industrial facilities. Ironically, pumping systems are rarely included in energy-efficiency calculations, even though pumps present such energy-savings potential. One could argue that mentioning “motor” or “variable speed drive” (VSD) is sufficient because these components indicate the greatest energy-savings opportunity in a pumping system. However, the key to realizing the energy-savings potential is to look at the system as a whole instead of just its component parts. A typical component-part approach might indicate that the motor is 89.5 percent efficient and that there is an opportunity to gain 4.7 percent by switching to a high-efficiency motor. Specifically, 89.5 percent is the average efficiency of motors used on pumps, and 4.7 percent is the average efficiency increase from the U.S. Department of Energy’s 1998 pre-Energy Policy Act motor efficiency to the National Electrical Manufacturers Association (NEMA) standard 12-12 known as NEMA Premium. The addition of a VSD may save 20 percent or more, and a higher-efficiency pump could improve pump operation enough to increase efficiency from 74 to 78 percent. This approach yields an efficiency gain of 4.7 percent on the motor, 20 percent overall for the VSD and 4 percent for the pump, resulting in a power savings of 28.4 percent for the entire pumping system. In this scenario, changing the motor is an easy process because the higher- and lower-efficiency motors are normally interchangeable. Adding a VSD is a bit more difficult. The VSD must be checked for compatibility with the motor, and this often requires a change to the motor as well. Most motors supplied today are generally compatible with VSDs. The end user also must determine how to control the VSD and at what reduced speed and power level it will run. One example of a simple approach to control is maintaining a set pressure in the pumping unit. The control components can be in the mechanical room, and installation costs and required system control are minimal. Installing a VSD is relatively easy because any electrician can place the unit on the wall and run the motor power through the VSD before going to the motor. If these simple steps are followed, a VSD installation can save 28 percent in energy costs. In this example, the owner probably would not change out the pump because doing so could save only 4 percent of additional energy, and changing the pump can be an involved process. The real savings opportunity is in the rest of the system—pipe design, valves and control type, in conjunction with the pump, VSD and motor. One example of the energy use in a typical pumping system shows 20 percent for the pump, 18 percent for delivered energy, 8 percent for the motor, 29 percent for piping and 25 percent for throttle. The opportunity to save energy is illustrated by the percentage. The example shows that only 8 percent of the energy produces valuable work. The remaining 92 percent is wasted energy and is available for more efficient operation. The motor accounts for only 8 percent of the energy loss, yet that is frequently the main target for energy reduction in systems today. The second target is VSDs in pumping systems, which, on their own, can contribute limited reduction in the energy consumption of a pumping system. The true opportunity to reduce the 92 percent wasted energy can be realized only by creating an optimized pumping system with minimum hydraulic pipe losses, combined with the proper size and energy-efficient control of the pumping system.
4 Ways to Improve Efficiency
Figure 1 illustrates four opportunity levels for improving the efficiency of a cooling secondary pumping system in a heating or cooling loop in a commercial building. This example starts with a three-way constant-flow pumping configuration that any system installed prior to 1995 probably employs.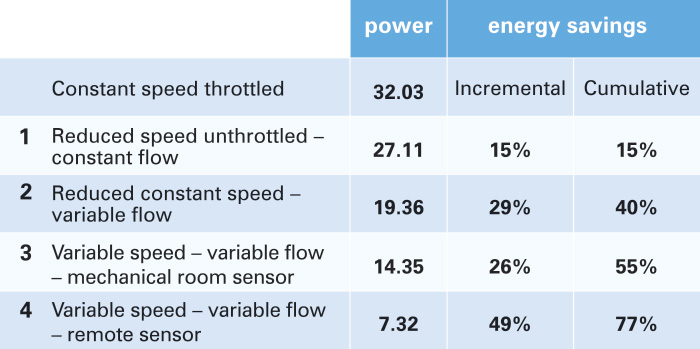
Case Study
The following case study illustrates the tremendous energy savings available when a facility considers the entire pumping system. Opened in 1972, the recreation complex of a community college contained two new boiler pumps that were installed in 2009. Two years later, technicians measured the pressure on either side of the two pumps and discovered that the pumps were operating at a much lower performance point than originally specified. The project engineers suggested that the college replace the pumps with variable speed pumps that would adjust operating speed to match the system’s requirements. To make the retrofit as easy as possible and avoid any changes to piping, the facility used the same pump size as originally specified and relied on the variable speed technology to continually adjust speed and pressure.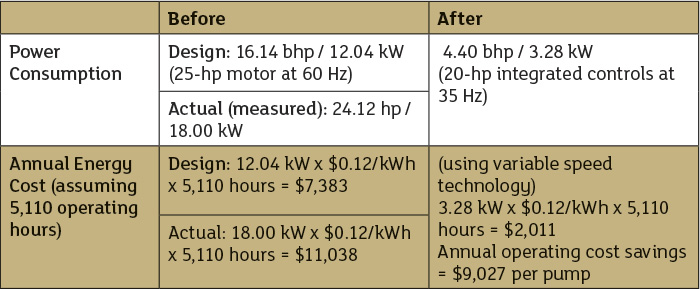