Q. What are some effects of a gas and liquid mixture being carried through a rotodynamic pump? A. The most dramatic effect of gas or vapor on rotodynamic pump performance is the blocking of the impeller inlet. When this happens, the pump becomes air-bound, and the impeller acts as a centrifuge, tending to separate the heavier liquid from the gas that builds up at the impeller inlet. At low flow rates, the liquid flow cannot carry the gas through the impeller, and the gas bubble grows until it completely fills the impeller eye on the suction side. As a result, flow stops. Even when small amounts of gas are carried through the impeller, the liquid rate of flow and pump head are reduced (see Figure A.4). This reduction is the result of the blockage of the flow by the gas and a reduction in developed head because of the reduced specific gravity of the pumped mixture. Dissolved gases evolving out of solution can have similar effects. When the specific gravity of liquid alone is used to convert pressure to head, a lower head measurement is indicated. Figure A.4 illustrates that even with small percentages of gas, the unit stops pumping liquid because of accumulated gas in the impeller when operating near the shutoff condition of the pump. High velocities can carry higher percentages of gas. Therefore, when gas entrainment is a potential problem, pumps should be operated at or beyond the best efficiency point (BEP) flow rate specified by the manufacturer.
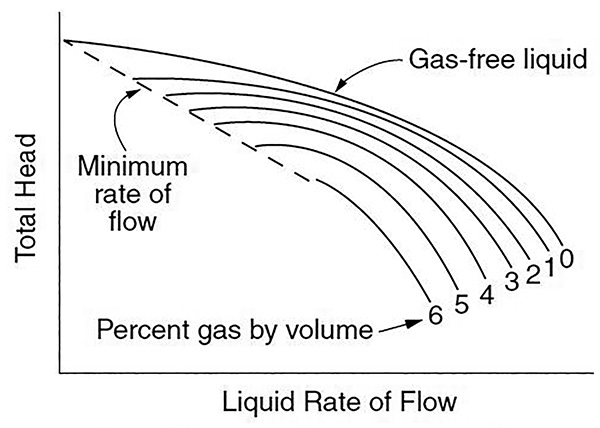
- Knowledge of the piping configuration
- The size of the pipes
- The piping materials
- The properties of the fluid
- How quickly the pump or fluid accelerates or decelerates