The triplex lift station arrangement provides a solution for grape wastewater processing.
07/25/2014
Proper pump selection in winemaking is important. Converting a solid such as grapes into a liquid on a large scale requires several different specialized pump types for transferring, filtering and bottling. Pressing/settling, fermentation, aging, separation, chilling and bottling are all pump-intensive operations. The dilemma that all domestic vintners face is what to do with the waste created by the process stream. The solutions differ depending on the location and federal regulations. One California producer of premium wines manages these issues with environmental awareness. The treatment and release of wastewater had to meet its high corporate standards.
Wastewater Treatment System
With an expanding market for its range of varietal wines, production at the winery had to be increased. An effective treatment process for the winery’s wastewater had to be designed. The challenge of meeting the waste stream demands and maintaining optimum production at peak efficiency was Jason Simpson’s responsibility. Simpson is the plant manager for EcoLabs, the contractor responsible for the operation of the wastewater treatment system at the winery.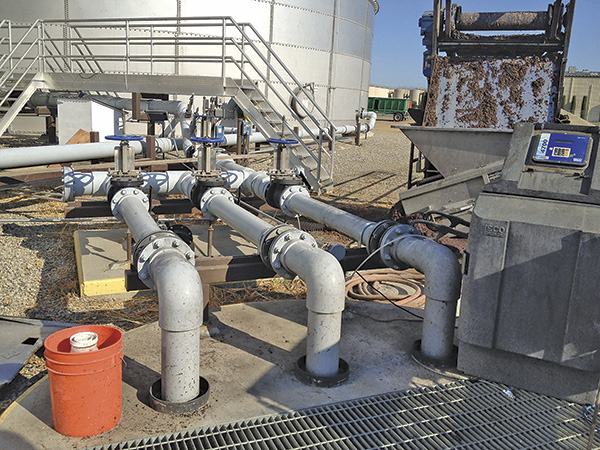
- Corrosion resistance—The pumps must be corrosion resistant because of the waste media’s acidity.
- Erosion resistance—Hard metallurgy was required to handle the coarse solids (such as stems and pits) encountered.
- Non-clog design—As solids settle out, they could clog the pumping units.
- Minimal footprint and self-priming—Dry mount pumps would require too much floor space and reliable priming. Submersible pumps are inherently self-priming and remain cool while submerged in the liquid.
- Reliable—Positioned at the bottom of a deep sump, the pumps would cause operational delays if continuous inspection or maintenance were needed.
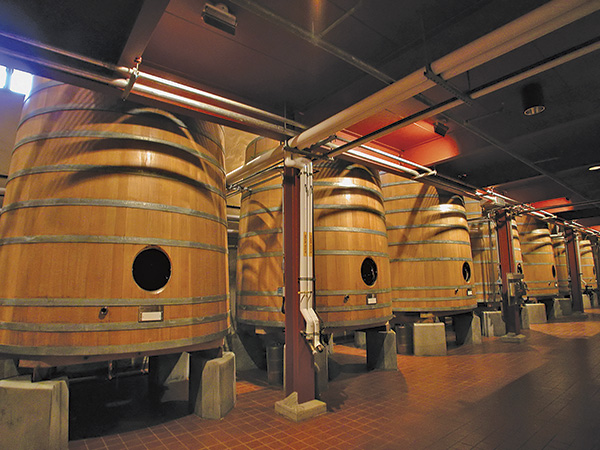
Submersible Pump Design
The pump distributor’s team decided to specify three submersible pump models that were installed in a triplex arrangement. The triplex lift station is a unique arrangement of three pumps operating in parallel. Specifying three pumps for the sump (instead of one or two larger pumps) increases the system’s reliability while efficiently covering the required wide range of operating conditions between the seasons. The triplex control allows for the operation of one, two or all three pumps at a time depending on the changing rate of inflow to the tank. The pumps alternate lead and lag position. In this arrangement, they are exercised regularly and wear more evenly. A high-level alarm is also available. The non-clogging capability of the pumps makes them an effective solution for handling the grape wastewater process. This pump produces a shredding action using a cutting impeller with a tungsten carbide tip against a suction plate. The suction plate has an irregular opening with engineered cutting slots to help grab the debris and aid the impeller with shredding. Other characteristics that make these pumps a practical solution for the grape wastewater process include:- Volume and lift—The non-clog, single vane impellers are designed for high volume and lift performance, ideal for the wet well application.
- Wear resistance—All wear and wet parts (parts exposed to the grape waste)—such as the impeller, wear-plate, oil housing, pump-housing and inner pump top—are made of cast 316 stainless steel material.
- Reliability—The pumps offer three-seal motor protection. The submersible motor is protected by double mechanical seals. The lower seals are made of silicon carbide/silicon carbide, and the upper seal is carbon/ceramic. An additional lip seal is installed above the impeller to help prevent abrasives from entering the seal chamber. Winding protection and National Electrical Manufacturers Association Class-F motor insulation allows motor temperatures up to 230 F, which offers an advantage compared to pumps with Class-A and Class-B insulation. An automatic switch turns the pump motor off if the temperature and/or amp draw rises too high.
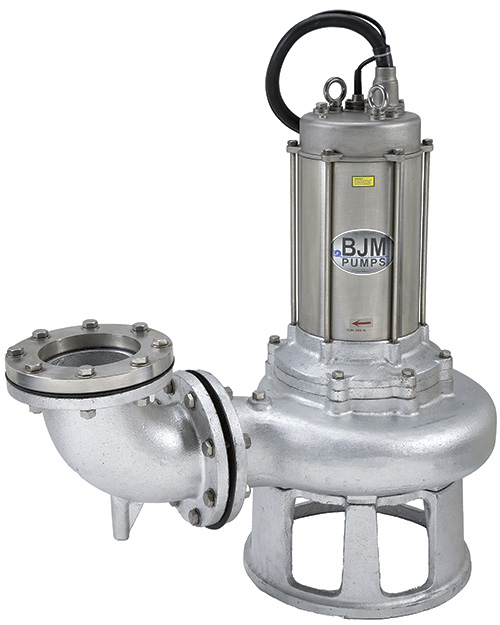