As budgets tighten, operators of manufacturing facilities must implement new ways to meet established production quotas while spending less money. Improved operational efficiencies can critically affect the profitability of food and beverage, pharmaceutical, and cosmetic manufacturers, from the most basic production-line level through entire plant efficiencies, and even overall corporate performance. One common solution for this has been increasing the focus to more energy-efficient, “green” operations. This has led to the incorporation of more efficient light bulbs or streamlining operations to reduce the plant’s consumption of electricity, which leads to a decreased carbon footprint. The ultimate goal of these lean manufacturing operations is to realize current or higher product yields while using fewer resources, resulting in a healthier bottom line. Many green initiatives, however, are not driven by sound economic principles. Focusing on improved energy efficiency and consumption in manufacturing operations is admirable, but many manufacturers have already maximized their energy efficiencies. Because of innovative fluid-transfer methods, greater savings than those realized in energy alone can be realized in the food and beverage, pharmaceutical, and cosmetic/personal care industries. Product waste is one area of hygienic manufacturing that experiences extremely high costs. The McKinsey Quarterly Food Waste Alliance reported that, annually, more than $120 billion of product is wasted worldwide. The Natural Resources Defense Council also estimates that the U.S. loses 40 percent of its food from farm to fork to landfills. Between farm and fork are the processing plants that manufacture some of these products. These plants are the focus of this article.
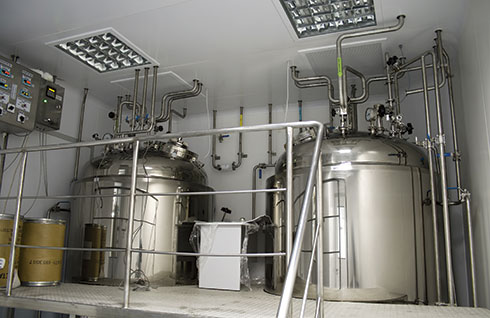
Determine High Product-Recovery Values
Three criteria are used to determine if high product-recovery values can be achieved in production processes that directly impact the manufacturing operation’s top and bottom lines:- Ingredients used in the raw materials for intermediate or final products that are both extremely expensive and valuable
- Product changeovers (switching between products) occuring frequently, such as one or more times per day
- Appropriateness of the product-recovery technique or technology for the ingredient or product
The Challenge
Incorporating increased energy efficiency into the hygienic-manufacturing process is one way to save operating costs, but it is not necessarily the best way. Table 1 shows how much money is consumed and potentially saved per positive displacement pump if the cost for energy is $0.10 per kilowatt hour (kWh).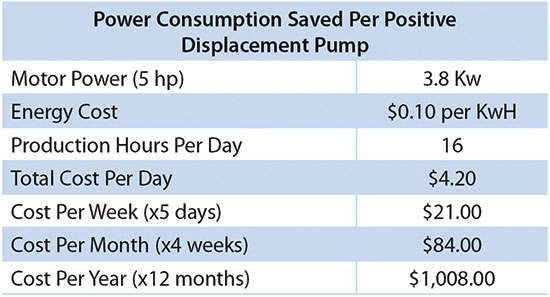
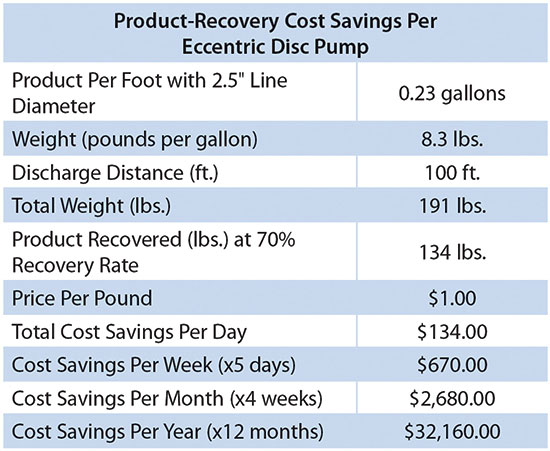
- More water to clean the lines
- Additional cleaning and treatment chemicals to clean the lines
- Sanitizing chemicals to sanitize the lines
- Energy to facilitate the cleaning process
- Labor costs/hours to perform longer cleaning operations
- Disposal costs of used water, chemicals and product
- Water treatment costs and associated treatment chemicals
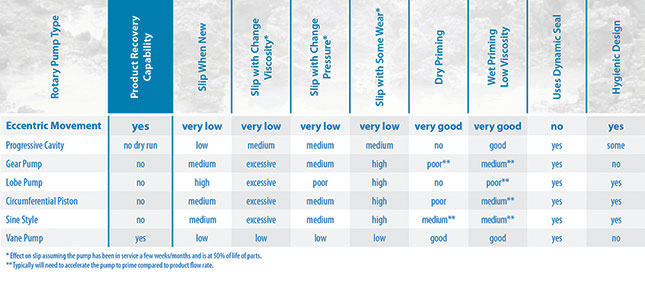
The Breakthrough
With the amount of potential savings achieved with adequate product recovery, eccentric disc pump technology sets a new standard in product-recovery capabilities in hygienic manufacturing operations. Eccentric disc pumps are the only hygienic pumps with this capability. The key to the eccentric disc pump’s heightened product-recovery capabilities is that it operates with a disc that moves on an eccentric plane within a circular channel, which gives the pump the ability to provide non-pulsing, low-slip operation with high volumetric consistency. Many liken this method of operation to a scroll-compressor effect. This design also means that flow rates vary minimally with changes in viscosity, temperature, system back-pressure and component wear. Most important for product-recovery considerations, eccentric disc pumps are efficient enough to pump air when no fluid is present. This creates a vacuum effect on the pump’s suction side and a compressor effect on the discharge side. Once the product runs out in the feed tank, the eccentric disc technology continues to pump air in a constant, non-abrupt, non-pulsating manner so that the surface tension on any remaining fluid is not broken. This produces a plug effect, which pushes out the product “plug” as a whole.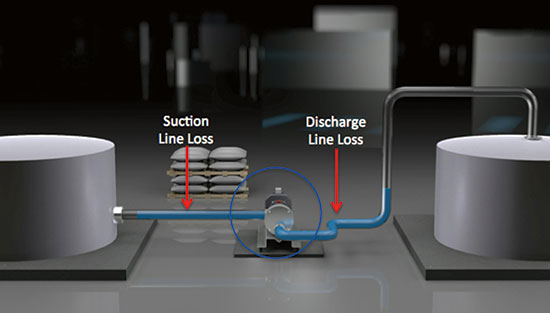
- A multinational, high-end cosmetic manufacturer recovered enough silicone-based product to immediately pay back the cost of the pump within a few short days.
- Two global yogurt companies with long transfer lines recorded 70 percent to 80 percent and higher product recovery rates, which resulted in the quick deployment of an additional pump in the process.
- An oral-care company upgraded from centrifugal pumps to quickly achieve product recovery targets with its low-viscosity products.
- A pharmaceutical company filled many oral medicines with frequent product changeovers.
- A large baked-goods company more effectively recovered the filling used in pastries, which also prevented injection nozzles blockages.
- Eccentric disc pumps can recover product from tank bottoms, inlet and outlet lines.
- Eccentric disc pumps can recover product from small-diameter lines where pigging is not possible.
- Eccentric disc pumps can recover product through ordinary valves, heat exchangers, magnetic traps, flow meters and other accessories found in the transfer line.
- Product recovery with eccentric disc pumps is seamless because no line interruptions will occur between normal production and the product-recovery phase.
- For the majority of the product-recovery process, air mixing is not a concern because most of the product recovered by an eccentric disc pump comes in the form of a product plug with no air mixed in. A simple flow switch can be used to shut down the pump before the air purge reaches the product’s destination.