As part of a project to save energy costs in its jet array system that clears sediment, the Port of Grays Harbor is saving more than 1.3 million kWh per year.
Fluke Corporation
07/06/2017
The Port of Grays Harbor in Washington is a bustling center of shipping on the West Coast of the U.S. Only two hours from the deep waters of the Pacific, the 1,400-foot-long (430-meter [m]) Terminal 4 is capable of handling heavy industrial equipment and other large cargo such as automotive imports and exports. Water depths of about 40 feet (12 m), on-dock railroad access to BNSF and Union Pacific lines, and covered warehouse spaces, among other features, make the port attractive to shippers from as far away as Asia and Africa.
.jpg)
.jpg)
Tracking Energy Use on a Compressor
As part of the project to save energy costs in the jet-array system that clears sediment at the Grays Harbor port, the team recommended a smaller, variable speed drive air compressor along with a dryer system. Baseline data was taken over a number of weeks. The baseline, captured in 2013, showed the compressor with an average power demand of about 17 kW. After installation of a new variable frequency drive and smaller compressor, data showed a lower power demand of about 9 kW. The data, captured on an energy logger, confirmed the energy draw to project stakeholders and was used to project energy savings of more than 30,000 kWh per year. In addition to energy savings, the new system is helping with maintenance problems the port was having with moisture buildup in the compressed air system piping.
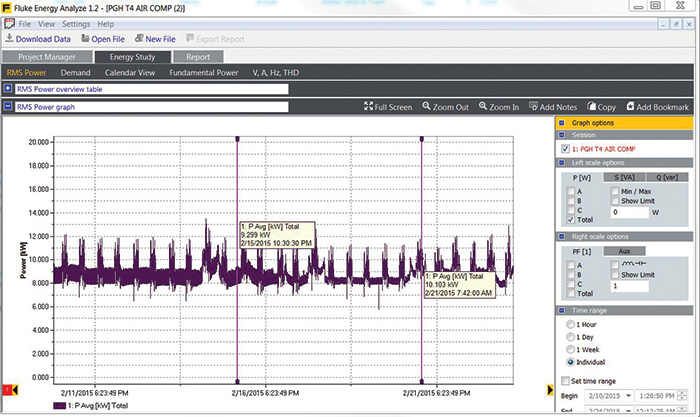