Q. What is water hammer, and what is its impact on a pumping system? A. Water hammer, or hydraulic shock, is a condition that exists when a column of fluid changes velocity quickly in a piping system. Water hammer has several causes, such as a pump start or stop or a rapid change of valve position. The velocity change results in a pressure wave that is above and below the normal pressure in the piping system. These pressure waves are called surge pressures or water hammer (when water is the fluid), and their magnitude can be sufficient to burst or collapse piping, valves, machinery casings and other devices. The pressure wave’s magnitude can be calculated with reasonable precision if the user knows the configuration of the piping, the size of the pipes, the materials of the piping, the properties of the fluid, and how quickly the pump and/or fluid accelerates or decelerates. When the column of fluid in the piping is either started or stopped, the energy of the system is transformed from velocity energy to head or pressure energy. Because the fluid and piping material are not completely incompressible, they absorb a fraction of the energy. Cast iron, for example, is a rather brittle material and is more susceptible to failure from sudden impact of a pressure wave that is well above its normal internal pressure and traveling at the speed of sound. Other materials that are more ductile may absorb the shock waves without cracking but still risk permanent deformation and failure. The pump is not the only component that is affected by this phenomenon; valves, sprinkler heads and pipe fittings are also at risk of catastrophic damage. Water hammer can adversely affect pipe hangers and pump foundations. Polyvinyl chloride (PVC) pipe and fittings are especially susceptible to damage from water hammer. Surge analysis is necessary because surge will occur in every pumping system. Water has mass. One cubic meter of water at 15 C (59 F) weighs 1,000 kilograms (kg) (1 cubic foot [ft3] of water weighs 62.4 pounds, or 1 gallon weighs 8.3 pounds at sea level). Moving water has momentum, which is directly related to both the mass and the velocity of the liquid. The faster the liquid flows, the greater its momentum. The greater the momentum, the more damage water hammer can cause if the liquid is suddenly stopped. Surge pressure will be maximized when the fluid is stopped in less time than it takes for a pressure wave to travel from the equipment that stopped the flow to the other end of the piping system and back. Water hammer can be understood through proper surge analysis and controlled through proper valve closure rates (with slow-closing valves), controlled starting and stopping of pumps, the addition of diaphragm tanks to absorb the pressure surge, and relief valves to release the pressure. For more information on water hammer, refer to ANSI/HI 9.6.6 Pump Piping for Rotodynamic Pumps. Q. How does the elevation from the suction gauge affect the NPSHA calculation? A. The NPSHA is the total suction head available over the vapor pressure of the pumped liquid corrected to the centerline of the impeller (or impeller inlet vane tip datum if vertically mounted) as shown in Figure 9.6.1.1a and measured at the inlet to the pump. An NPSH margin may be required for several reasons related to pump performance and service life.
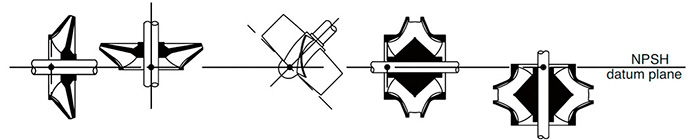