Within the general classification of external gear pumps, precision gear metering pumps are a specialized subset providing accurate, reliable and pulse-free metering performance over a wide range of applications and process fluid conditions. While many gear pump applications are designed for simple transfer of viscous liquids, others are manufactured with extremely close tolerances, allowing for much higher pressures and the extremely accurate flows required of precision metering type applications. They differ from the pumps used for transfer applications in that internal operating clearances are much tighter, minimizing internal fluid slip and allowing for highly accurate and measured amounts of fluid to be metered and transferred. Due to their extreme close tolerances and smaller gear sizes, these pumps are capable of flows as low as 0.5 cubic centimeters per minute with pressures to 10,000 psi and temperatures from -40 F to 950 F.
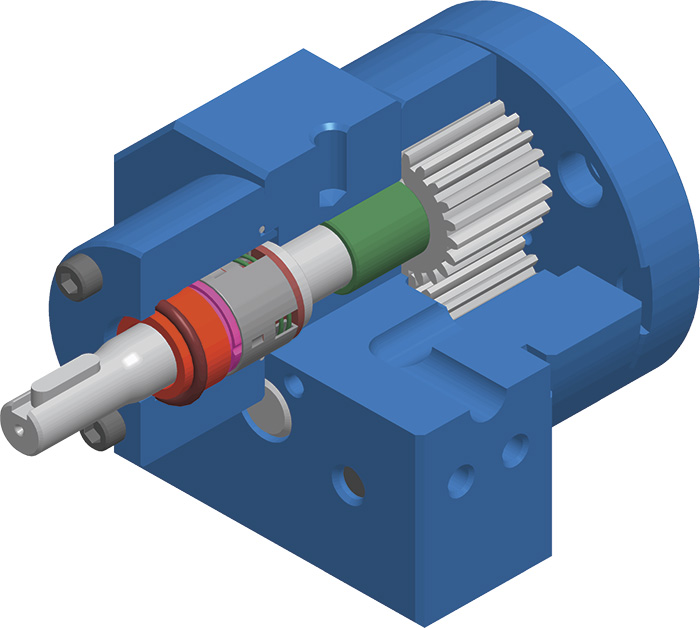
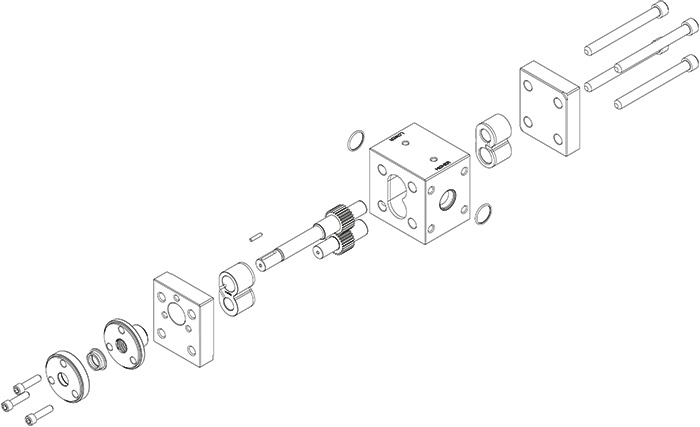
- overspraying/overdispensing resulting in excessive material waste and increased manufacturing costs
- overfeeding additives to account for under-dosing resulting in extra cost and effect on product appeal
- difficulty controlling extruder variations such as pressure fluctuations, viscosity inconsistencies and density changes
- inefficient pressure and volume variations in paint spray equipment applications, affecting quality and productivity on the line
- overfeeding expensive process chemicals to prevent the under-dosing that would affect the finished product quality irregular, pulsating delivery of expensive additives
Accurate Delivery
The volumetric output of a fluid is metered and moved with precision at a constant speed, with minimal pulsations, according to the size of the gear teeth and the speed at which they rotate. Precision metering gear pumps can achieve the tightest pumping clearances, measured in microns, to minimize fluid slip. Clearances between the gear teeth tips and the side wall can be as low as 0.00015 inches (0.0031 millimeters). These clearances are 20 times thinner than an average sheet of paper. Manufacturing tolerances on many parts to +/- 50 millionths of an inch with surface finishes as smooth as 4 micro inches or better are possible. A continuous, pulseless stream of dispensing or dosing results as the gear pumps move many small cavities per revolution. Sustained linear flow can be maintained even during changes in operating speeds, pressures and temperatures. The drive system and incorporation of closed loop speed controller can maintain speed accuracy at 0.1 percent levels.Reliable in Service
Metering gear pumps can be made of many variations of stainless steel for corrosive or sanitary applications, but they are commonly made of hardened tool steel for abrasive applications. Maintenance on a metering gear pump is typically much lower than with other technologies due to the rugged construction and limited number of moving parts. In many cases there are only three moving parts—the drive shaft, the drive gear and the driven gear. Fewer parts means reduced, as well as easier and faster, maintenance. Conversely, many other metering pump technologies contain as many as 16 moving parts, all subject to wear. In addition, most have check valves that risk failure due to erosion, corrosion or foreign particles caught between the valve ball and seat. Further, these check valves create restrictions increasing the net positive suction head (NPSH) required for the pump. Should your process require an accurate, reliable metering gear pump, it is important to keep the following tips in mind. 1. Get the application data right. As with all pump applications, it is imperative to convey correct and complete application data to the pump manufacturer. Doing so will help the pump work correctly and with minimal maintenance. This data should include but not be limited to:- flow rate (minimum, normal, maximum)
- inlet and discharge pressures (minimum, normal, maximum)
- viscosity
- temperature (minimum, normal, maximum)
- the fluid being handled as well as elastomer and metal preferences if this is not a common liquid
- whether any solids are present, and if so, the percent of solids, the maximum particle size of solids and the hardness of solids
- motor data (phase, hertz, voltage) and the area classification
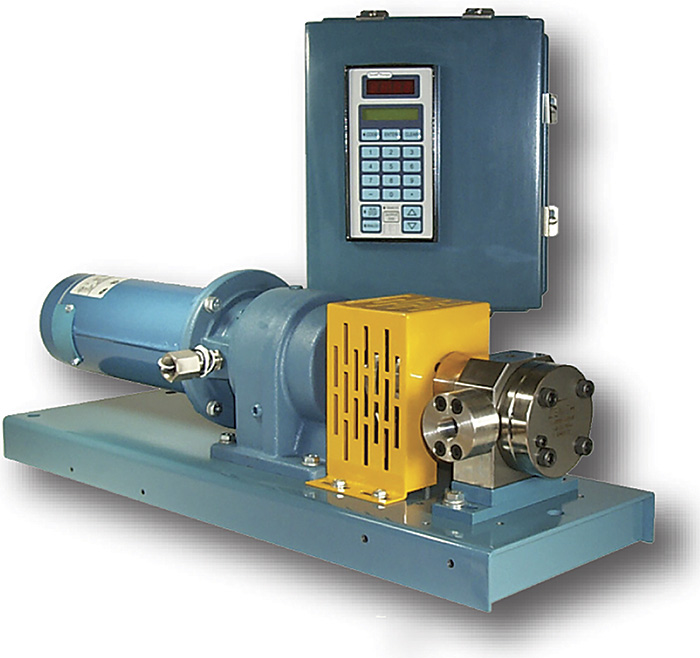