AmeriChem Systems Inc. (ASI) is a custom process equipment fabricator for select multinational corporations and engineering, procurement and construction firms around the globe. Based in Aurora, Illinois, ASI specializes in developing customized chemical feed systems, boiler feed water systems and cooling tower water treatment packages for some of the largest nuclear power plants and oil and gas refineries around the globe. The chemical feed systems that ASI builds include the tanks, pumps, piping infrastructure, valves, flow meters and control systems needed to run large-scale industrial water treatment applications. An examination of chemical feed water treatment systems that ASI has delivered to various nuclear power plants in the U.S., as well as one of the largest oil and gas refineries in the Middle East, highlights the factors behind picking the right pumping technology for these sites.

Nuclear Power Plants
ASI’s water treatment applications in nuclear power plants throughout the U.S. feature rotary gear pumps that provide the chemical-dosing capabilities needed for both circulating water systems and service water systems. The purpose of a circulating water system is to provide cooling water for the power plant’s main condenser using a large heat exchanger that removes heat from the condensing steam exiting the plant’s main turbine. Nuclear power plants typically pump more than 500,000 gallons of water per minute (gpm) through the heat exchangers in circulating water systems, which is why most power plants are near an abundant water source, such as a river, lake or ocean.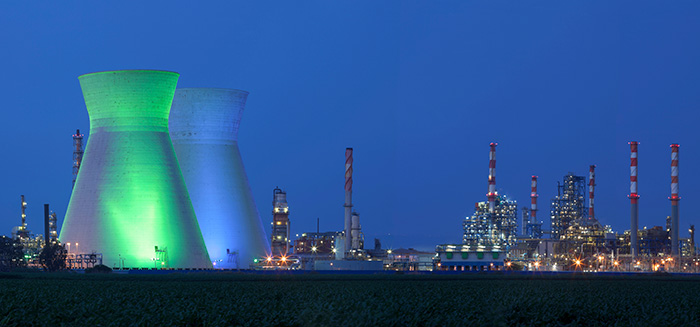
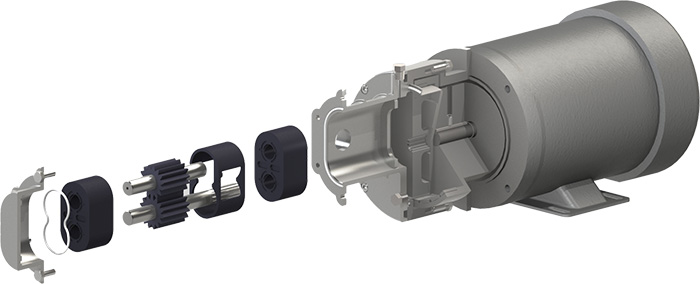
Picking the Pump
The requirements of exceedingly high-flow volumes and uniform, pulse-free dosing under low pressures prompted ASI’s distributor and authorized service center—Addison, Illinois-based Enpro (Engineered Products)—to recommend a specific type of rotary gear pump. Enpro’s John Nelson identified five primary benefits to using a rotary gear pump for these types of water treatment applications:- Performance: Gear pumps are designed to address high flow rates and deliver uniform, pulse-free dosing.
- Reliability: Chemicals such as sodium hypochlorite tend to off-gas when they come in contact with metal surfaces. Non-metallic gear pumps feature a simple design that helps prevent off-gassing, which minimizes disruptions and helps to maximize uptime for water treatment operations.
- Safety: Because exposure to the chemicals such as chlorine gas can cause respiratory issues for employees, great care should be taken to ensure that leaks do not occur when dosing hazardous chemicals. Sealless gear pumps offer fewer points of failure because there are no leak points for harsh chemicals to damage the pump or the surrounding equipment.
- Streamlined maintenance: Access to the inner workings of a pump is an important design feature that impacts maintenance. If a pump’s gears are not readily accessible, then engineers must decouple the motor, close the valves and remove the piping at the pump’s suction and discharge ports. Rotary gear pumps that feature a front pull-out design can be repaired in place. This minimizes downtime by eliminating the need to lock-out/tag-out the pump and move it to the repair shop.
- Smaller footprint: Rotary gear pumps are compact in nature, and they do not require as many ancillary items as diaphragm pumps (such as pulsation dampeners), so the equipment package’s overall size can be reduced.
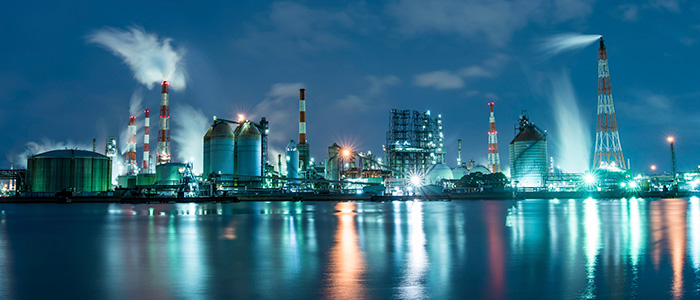
Oil & Gas Refineries
Oil and gas refineries use significant quantities of water for the processing and cooling required to turn feedstocks into fuel. As costs for feed water increase, refineries are focusing more on recycling and reuse. This places greater emphasis on treating water so that it does not damage or compromise the plant’s pumping and piping infrastructure. To clean water, refineries meter specific doses of sulfuric acid, sodium hypochlorite, phosphoric acid and amine (scrubbing) solutions to remove hydrogen sulfide (H₂S) and carbon dioxide (CO₂) from gases. For one of the largest oil and gas refineries in the Middle East, 30 chemical feed-water treatment systems using API-675-compliant metering pumps was built. These systems were designed to address variable flow rates from 1 liter per hour (l/h) to more than 200 l/h, and pressures ranging from 10 to 40 BarG. Designers integrated all of the required components, including tanks, pumps, piping, flow meters and control systems. Engineers coordinated with the various companies involved to finalize the mechanical and electrical design, including programmable logic controllers and control panels, and they completed the functional testing. For the 30 systems, Enpro’s Grant Cook standardized the pumping infrastructure on the selected API-675-compliant reciprocating diaphragm pumps for the following reasons:- Flexible configurations: The refinery required metering pumps in different materials, including 316 stainless steel, Alloy 20 and polyvinylidene fluoride (PVDF). The refinery uses dozens of chemicals, corrosion inhibitors and scale inhibitors with different characteristics that require different types of wetted ends. The ability to leverage a single pump family that could be configured with different materials helped meet the refinery’s delivery deadlines.
- Accuracy: The pumps provide 1,000-to-1 turndown capabilities, with steady-state accuracy down to +/- 0.5 percent. This is important because chemical costs are one of the larger expense items for refineries. The chemicals used are procured in concentration, and they must be metered accurately not just to save money, but to ensure that overdosing does not occur.
- Longevity and reliability: This refinery runs continuous operations, so downtime must be avoided. The metering pumps used for the water treatment applications feature hydraulically actuated double diaphragms with diaphragm leak-detection capabilities. Because the hydraulically actuated diaphragm (HAD) operates with equal pressure between the hydraulic and process fluids, it eliminates diaphragm stress because the pressure is essentially equal on both sides at all times. This balance provides longevity for HAD pumps, enabling them to operate for 20 years or more. The leak-detection system monitors the pressure between the two diaphragms and notifies plant engineers if there are changes in pressure or leaks.
- Local support: For this particular refinery, the pump manufacturer’s presence in the Middle East played an important role because local support teams were available to assist with maintenance and support.