The treatment of municipal drinking water demands precision and consistency. The Environmental Protection Agency requires that exacting chlorine disinfectant concentrations be maintained to ensure water quality, so utility managers are quick to replace unreliable equipment. That’s what happened at a water utility district in rural Illinois, where repeated pump failures had raised the cost of maintaining chlorine residual levels—until a smart digital dosing pump solved the problem. The troubled chlorine dosing pump at one of the water district’s booster stations could not handle the continuously high water pressure and was developing repeated leaks. These leaks caused insufficient levels of residual disinfection at customer taps, adding maintenance/labor costs while also posing a safety hazard to the plant’s maintenance staff.
Big Challenge for a Small Town
Following a sand filtration system that removes mud and other particulates, the water supply operation adds chlorine disinfectant to inactivate any disease-causing organisms. The treated water is then pumped four miles to the booster station, where a second dosing pump adds additional sodium hypochlorite disinfectant to maintain EPA-mandated levels throughout the utility’s water distribution system.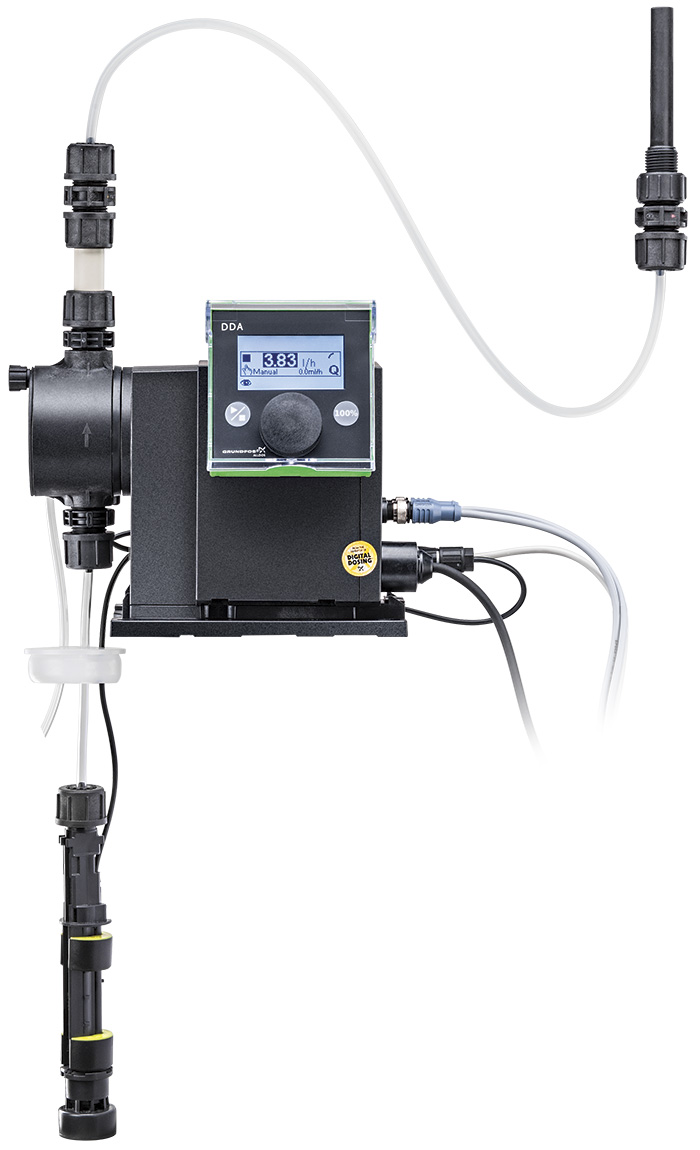
Water Down the Drain
When water quality was compromised—about once every month—the utility was required to dump the nearly 100,000 gallons in the pipe between the booster station and the remote customer taps. This was done by flushing it through a fire hydrant at the end of the line. The flushed water also had to be dechlorinated, at an additional cost. The plant manager sought guidance from a pump supplier, who recommended a smart dosing pump. The pump is designed to accurately inject chemicals into system pressures up to 232 psi without losing prime. In other words, the pump could accurately meter gaseous fluids without vapor locking and its pressure capacity was nearly twice that required by the utility station. Still, the plant manager had his doubts. “I was skeptical about trying another diaphragm pump because of our prior experience,” he said, noting that the vapor lock issue is what led him to install the peristaltic model in the first place.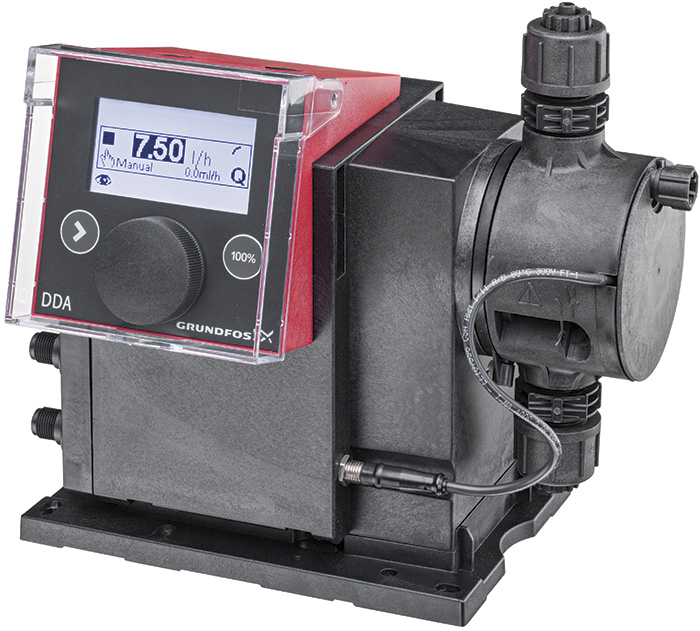
Smart Pump Technology
But the smart dosing pump has some important differences. Neither a conventional solenoid actuated diaphragm nor a peristaltic style pump, this particular pump offers the ability to build high pressure without vapor locking. While most diaphragm pumps vary output by adjusting the length and frequency of the pump stroke, the electronically controlled stepper motor in the smart dosing pump allows the duration of each discharge stroke to vary according to the set flow capacity, while keeping the speed and duration of each suction stroke constant. Said differently, the pump always operates at full stroke length, regardless of injection volume, ensuring optimum accuracy, no loss of prime and no suction disturbances. An intelligent drive and microprocessor controller ensure that each dose is performed precisely and with low pulsation, even when pumping high-viscosity chemicals or those with off-gassing properties. Metering accuracy is further increased by a 3000:1 turndown ratio to provide increased flexibility at small volumes. What is most impressive is the stepper motor’s ability to operate in multiple positions that allow it to start and stop precisely, and even to operate in reverse. The stepper motor’s reverse capability enables a feature called auto-deaeration, which causes the diaphragm and check balls to flutter, removing air from the suction side of the pump before the pump starts cycling. This is what eliminates the possibility of vapor lock or priming failures. The pump will alert operators if there are air bubbles inside the pump during operation or while it is in standby, and it offers standard features that display and/or correct failures such as:- overpressure
- underpressure
- valve leaks
- air bubbles