10/27/2014
Q. What are the effects of viscosity on rotary pump and system performance? A. The viscosity of a pumped fluid typically affects pump ratings in the following ways:
- The net positive inlet pressure required (NPIPR) increases with increasing viscosity (see Figure 1).
- The required pump input power (Pp) increases with increasing viscosity (see Figure 2).
- The maximum allowable pump speed (n) decreases with increasing viscosity (see Figure 3).
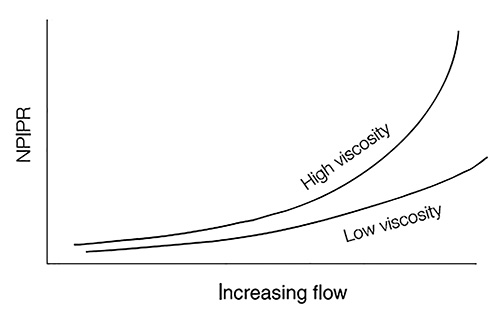
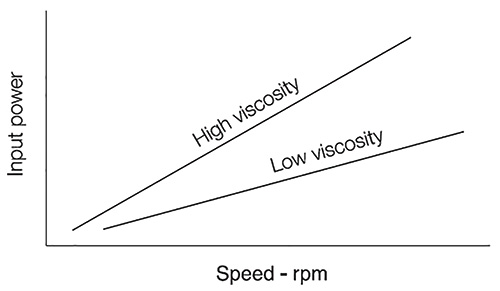
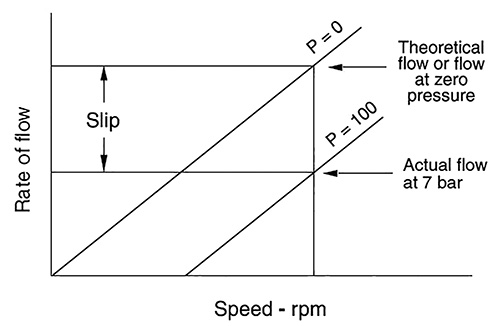
- Valves—Select low-noise type valves. Use two or more throttling valves in series to reduce the differential pressure across the valve. Locate valves as far away from the pump as possible. Avoid putting them between the microphone and the pump. Cover noisy valves with an acoustical barrier.
- Piping—Use pipe and fittings that are sized 1:1. Avoid situations that cause a change in velocity. Use straight runs of pipe from the pump to the supply tank. Cover noisy piping with an acoustical barrier material. Gears—Avoid high-ratio reducers and increasers. Cover test gears with an acoustical enclosure or barrier material.
- Test foundations/bases—Use rigid foundations and bases to support the pump. Avoid using large, flat, thin material that vibrates and radiates noise.
- Torque meter—An installed torque meter with integral speed pickup between the driver and the pump is the most direct method for monitoring power. This system directly senses the speed and torque required by the pump. Some torque meter readouts calculate the actual power transmitted.
- Power meter—This instrumentation is useful if the pump is driven by an electrical motor, either directly coupled to the pump or through a gearbox, belt or hydraulic coupling. Electrical transducers are typically installed in the electrical motor starter to measure voltage, current and phase angle. Multiplying them results in the power supplied to the motor. This approach monitors the power increase or decrease in the pump as parts deteriorate or drag and indicates if anything changes in the general health of the electrical motor and/or the gearbox, belts or hydraulic coupling.
- Electrical current—This device is similar to a power meter, but only the motor current is monitored. The line voltage and power factor are assumed to remain constant, allowing the end user to calculate the power supplied to the motor. While this method monitors the condition of the pump and motor, it is susceptible to error caused by variations in the electrical supply grid.
- Strain gauges—Strain gauges applied to either the pump shaft near the coupling or the drive output shaft with proper telemetry or slip ring equipment will indicate the torque required to drive the pump. This approach is similar to using a torque shaft, except a longer baseplate is not required to accommodate the length of the torque shaft. However, some accuracy is sacrificed. If the pump speed is constant or known, the power required can be calculated. Use caution when applying electrical power monitoring techniques to pumps exhibiting flat power curves (such as when the power changes little across the operating range). In these cases, setting alarm points can be difficult because of the detection of small power changes resulting from operating point changes and discriminating them from power changes caused by other reasons, such as temperature changes in the motor or pump and normal process fluctuations.
- Measurement practice—Monitoring the pump power usage alone only indicates whether the power changes. Power changes can also result from changing the hydraulic operating conditions and mechanical or hydraulic deterioration.