CFD and engineered improvements assist designers in their quest to produce more work from less energy.
11/22/2013
Pumping fluids with sediment, chemicals, slurry and inks has always been an air-operated double diaphragm pump’s (AODD) domain. Offered in many different construction materials, AODDs can be built to pump virtually any fluid, in most volumes. AODD pumps are the picture of simplicity. Diaphragms move inside fluid chambers to intake and expel fluid while check valves keep the fluid motion flowing in the right direction. These pumps operate solely by the back and forth oscillation of a single rod connected to two horizontally opposed diaphragms. How is the rod moved?
Powering the Pump
While multiple options for powering a diaphragm pump are available, pneumatic is the most common and typically optimum for most installations and applications. The humble beginnings of compressed air date as far back as 2000 B.C. when bellows were used to stoke the flames, as man forged iron and steel into the shapes upon which he would build his future. Today, the modern uses for compressed air are staggering. Everything from dental tools to modern robots relies on compressed air power.Engineering Air Flow
Efficiency is critical in any air-operated appliance. Compressed air is used so extensively in the industry that it is often regarded as a fourth utility—such as electricity, natural gas and water—but when evaluated on a per unit energy delivered basis, it is the most expensive. Therefore, an AODD pump that performs at lower pressures saves energy (and money) by consuming less compressed air. It also makes more air available for other equipment. Converting pneumatic energy to mechanical energy in the most efficient manner is the engineer’s goal. Installing sliding valves and seals that direct the air as desired is easy, but the real engineering occurs when determining how much air should go where, when and for how long. An engineer must decide whether to fall back on old technology or forge ahead into uncharted theoretical territory in search of the next great breakthrough. Often, to perform a complex task, engineers will design a complex circuit. One chemical transfer system provider decided to keep it simple, with fewer moving parts.Engineering Down the Rabbit Hole
A team of chemical transfer pump engineers tried a different approach, starting with where the air enters the pump and begins its work. This chemical pump provider wanted to address common problems experienced with AODD pumps—such as freeze up, stalling and lack of efficiency.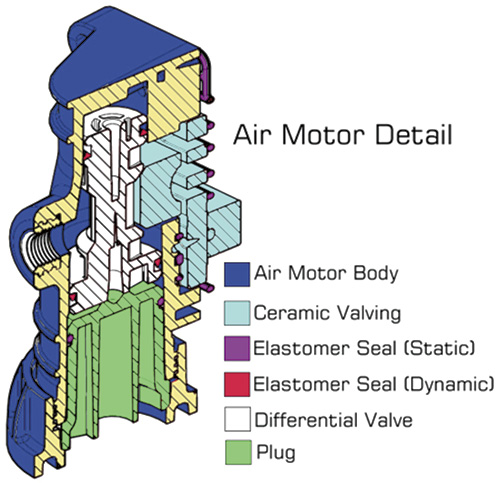
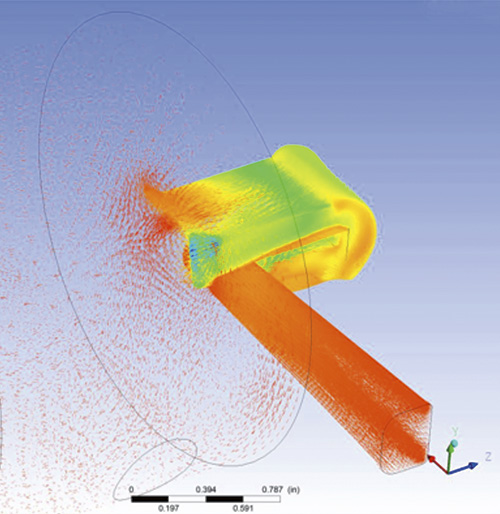
Challenging Fluid Dynamics
The dynamics of moving fluid are complex. Making the diaphragms move fluid as efficiently as possible is a challenge.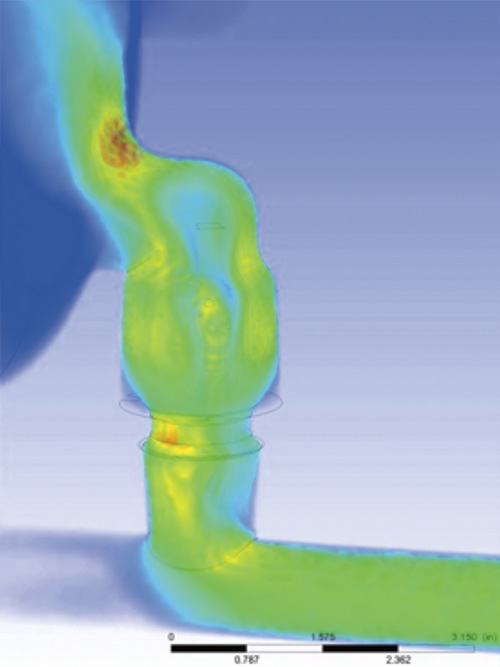
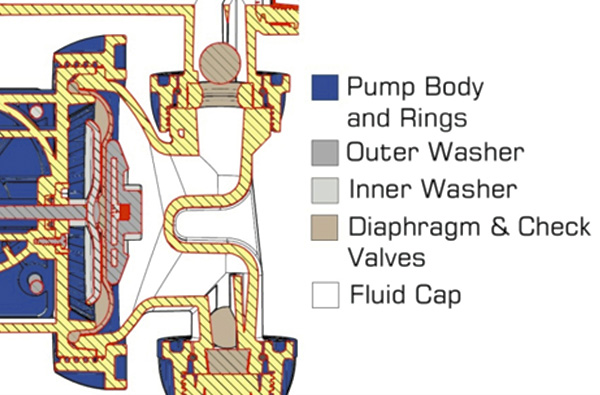