Minimizing total cost involves trade-offs between the elements of LCC analysis.
11/22/2013
Pump users and industry leaders have increased the emphasis on reducing the life cycle cost (LCC) of industrial pumps. Organizations with a matured procurement division do not purchase pumps based on their initial purchase and installation costs. Instead, they focus on the total life cycle cost of a pump, which is five times greater than the initial and installation costs. The key objective of analyzing total LCC is minimizing total cost, which involves trade-offs between the elements of LCC analysis. This analysis is a strategic tool to determine whether the initial cost is worth it after major future costs—such as maintenance, energy and downtime—are considered.
What Is the life cycle cost of a pump?
LCC is the total cost associated with an industrial pump from the point of procurement up to the point of decommissioning and disposal of the installed pumping system. It is an important tool to help plant managers choose between alternative resources and decide between repairs versus new purchase. Figure 1 shows the different costs incurred during the life of a pump, based on the assumption that the service life of the pump is 20 years. Of these eight major elements of LCC, energy, maintenance and repair account for approximately half the total LCC. These costs can be divided into the following three groups which are based on the buyer’s control over costs: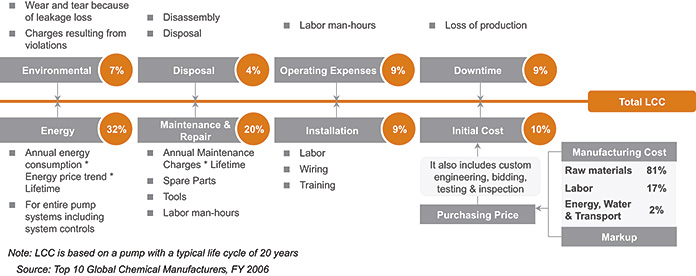
- Lower control comprises environmental and disposal costs.
- Moderate control comprises initial, operating and installation costs.
- Higher control comprises energy, maintenance and repair, and downtime costs.
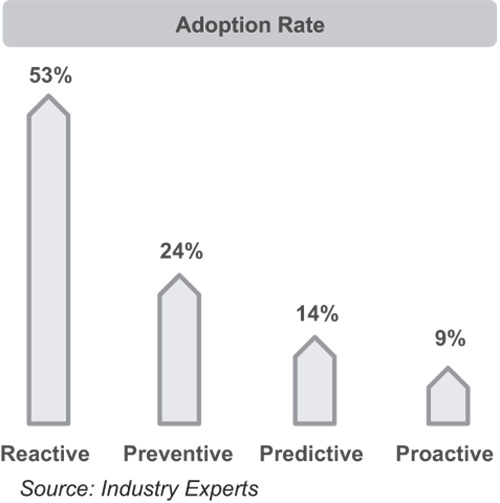
Why Should Pump Users Care About LCC?
Pumps make up a major portion of capital expenditures (CAPEX) in any processing industry, especially the chemical industry. It accounts for up to 20 to 25 percent of all the components used. The purchasing price is only a small part of the total LLC of any industrial pump, but other operating costs—such as maintenance, repair and energy—account for nearly half of it. Despite this, purchasing managers often make decisions based on the initial investment instead of overall operating costs. In the end, a plant manager must decide between an overhaul and purchasing a new pump for the application. To do so, LCC analysis is an important tool for plant managers.LCC Analysis Benefits
Most pump users make procurement decisions based on the initial purchase cost which is often only 10 percent of the total LCC. LCC analysis provides the trade-off point between the initial purchase cost and the other cost elements that occur during the pump’s life. This assists in deciding whether to pay a higher initial cost to avoid unwanted and unexpected maintenance and other costs. Users have little control over many of the inevitable costs—such as environmental, disposal and installation costs. However, maintenance, energy and downtime costs can be managed, and potential cost-savings are associated with these factors.Maintenance Cost Reduction Methods
Generally, pump users do not choose maintenance strategies based on the type of equipment. Reactive maintenance is not always the wrong maintenance strategy. Implementing predictive and proactive strategies on less critical pump systems may not be cost effective.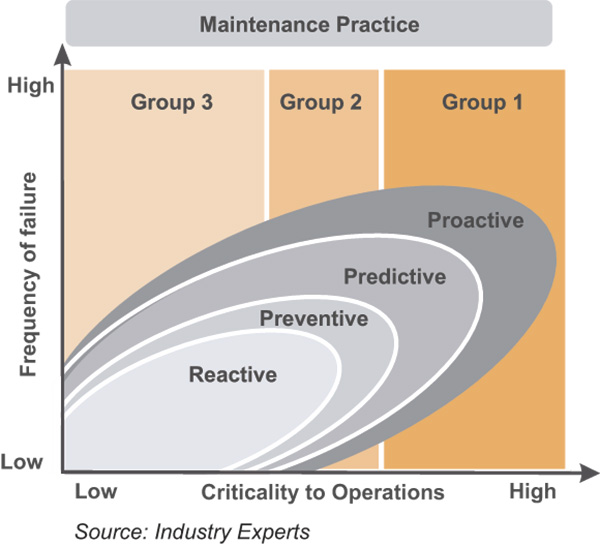
Energy Cost Reductions
Energy cost accounts for a higher portion of the LCC of an industrial pump than any other cost. Buyers look for energy-efficient options to reduce the pump’s energy consumption. Table 1 shows the possible reasons for higher energy consumption and ways to mitigate them.Reasons for Higher Energy Usage
- Installing oversized pumps into the system causes the system to operate at a higher flow rate. It will lead to increased energy consumption and reduced life.
- Piping work with more twists and turns requires more energy to run the pump.
- Energy use depends on the nature of the liquid being pumped. When the viscosity changes or the amount increases, the energy requirement increases.
- Corrosion on pipe walls may increase energy use.
- Energy use may increase when the performance of pumps is not monitored and controlled properly or when the pumps are not maintained.
- When the pump system operates far away from its best efficiency point, maintenance and energy costs will increase.
How to Mitigate Higher Energy Usage
- Select the pump system wisely based on flow rate and liquid characteristics.
- Do not use oversized or undersized pumps. Instead, install two or more pumps in parallel based on system requirements. Run these pumps based on the system requirements. It helps reduce energy costs by as much as 20 percent.
- Use variable speed drives, also called variable frequency drives (VFD).
Table 1. Possible reasons for higher energy consumption and ways to mittigate them.
Reduce Downtime Costs
To reduce machinery downtime, all the spare parts required for operation-critical machinery need to be kept onsite. Usually, buyers purchase larger amounts of high-critical spare parts to prevent equipment downtime. As a result, they tend to pile up more spare part inventory when the demand for spare parts is fluctuating. As a result, the buyer pays higher inventory holding costs. For a pump original equipment manufacturer, 40 percent of its revenue comes from spare parts sales. To have a win-win situation for the buyer and the supplier, a consignment stock option is a preferred solution. Consignment stock is an inventory of spare parts that is stored at the buyer’s location but is still the property of the supplier. The buyer is required to pay for the parts only when he /she picks it up from the stock to use. Therefore, the buyer pays later, but the stock is readily available at his/her plant to reduce downtime. This type system benefits the buyer and supplier because the buyer has the spare parts onsite whenever the demand arises, and it is another avenue of profit for the supplier.Consignment Stock Model
If end users are able to segregate the kind of spare parts to be kept at the consignment stock versus the supplier warehouse, they can save on the following:- Storage space
- Premium to be paid
- Insurance cost
- Scenario 1—In the case of customized and high-critical spare parts, buyers should choose a consignment stock model with their supplier to keep parts onsite and available around the clock, which can reduce downtime.
- Scenario 2—The critical but standard spare parts do not need to be kept onsite at all times because standard parts are easily available. In such scenarios, buyers can eventually save on insurance costs and inventory holding costs when they adopt a just-in-time sourcing practice. However, this depends on the proximity of the supplier to the production site.
- Scenarios 3 & 4—When the spare parts are non-critical, buyers are advised to order standard spare parts when demand arises and non-standard parts based on their historical demand pattern.
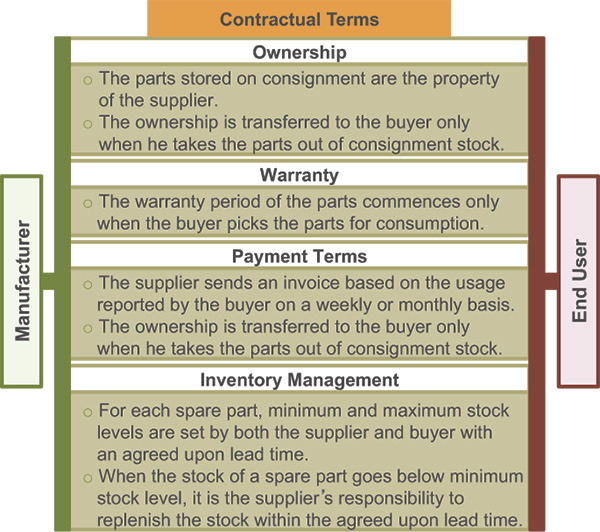