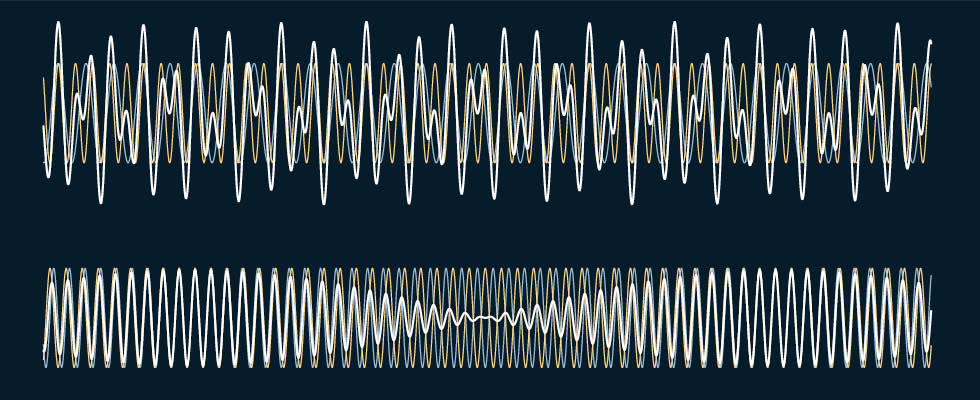
In pumping applications, maintaining efficiency and reducing energy consumption is crucial for both cost savings and environmental sustainability. However, one often overlooked challenge in these systems is the presence of harmonics, which can lead to decreased equipment life span, increased maintenance costs and reduced power quality. Fortunately, there are cost-effective solutions available that can effectively mitigate harmonics while optimizing pump performance.
What Are Harmonics & Why Are They a Concern?
Harmonics are unwanted electrical frequencies that occur in power systems, typically as multiples of the fundamental frequency (e.g., 60 hertz [Hz] in the United States). In pumping applications, these can be caused by various factors, such as the nonlinear behavior of power electronics like variable frequency drives (VFDs).
Cost-Effective Solutions Using Drives
VFDs offer a cost-effective and efficient solution to control motors in a variety of pumping applications. Here is how they work and why they are beneficial:
Variable speed control: VFDs allow precise control over the motor speed by adjusting the frequency and voltage supplied to the motor. This means pumps can operate at the most efficient speed, reducing energy consumption and wear and tear.
Built-in harmonic mitigation: Many modern VFDs come equipped with built-in harmonic mitigation technologies. These include passive and active filters that help reduce harmonic distortion and ensure cleaner power delivery.
Soft start and stop: VFDs offer soft start and stop capabilities, which reduce mechanical stress on the pump and eliminate the inrush current associated with direct-on-line starting. This leads to longer equipment life.
Energy savings: By running pumps at the optimal speed, rather than continuously at full capacity, VFDs
can result in substantial energy savings, often paying for themselves over time.
Improved power factor: VFDs can also help improve the power factor of the system, which can lead to reduced utility costs and penalties for poor power factor.
Customizable control: VFDs can be programmed to meet the specific requirements of the pumping application, allowing for fine-tuned control and optimization.
Extended equipment life span: By running the pump at optimal speed for the process application, VFDs help extend the life span of critical equipment, reducing maintenance and replacement costs.
The Impact of Harmonics
Harmonics can have several adverse effects on pumping systems:
Reduced efficiency: Harmonics can increase energy losses in motors and other electrical components, leading to reduced overall efficiency.
Increased heat: The additional power losses can result in higher temperatures in equipment, which can lead to premature wear and failure.
Voltage distortion: Harmonics can distort the voltage waveform, potentially causing malfunctions in sensitive equipment and even damaging other connected devices.
Power quality issues: Harmonics can affect the power quality within the facility, causing problems for other equipment and potentially leading to penalties or fees from utility companies.
Installation Considerations
While VFDs offer an effective solution for motor and pump control, their installation and configuration require careful consideration:
Sizing: Properly size the VFD to match the motor’s capacity, ensuring it can handle the load and operate efficiently.
Installation location: Install the VFD in a well-ventilated area with proper cooling to prevent overheating.
Maintenance: Regularly maintain and monitor the VFD to ensure it continues to operate optimally and efficiently.
Harmonic distortion and resonance: Evaluate other sources of harmonics and capacitors on the system to avoid harmonic resonance, which can cause damaging escalating currents and voltages at the resonant frequency. A harmonic analysis study can ensure proper selection and design of VFDs and harmonic filters for safe system operation.
In pumping applications, the use of VFDs is essential for maintaining equipment efficiency and prolonging the life span of pumps and motors by providing precise control over motor speed and energy-saving capabilities. When properly installed and maintained, VFDs can contribute to substantial energy savings and mitigate harmonics, making them a valuable investment for any pumping system. By adopting these solutions, industries can achieve their goals of cost reduction, improved equipment reliability and enhanced environmental sustainability.
Solutions for Harmonic Mitigation
The following solutions can be considered to mitigate harmonic distortion at the individual drive/load level:
Line reactors and drive-dedicated filters: Installed at the front-end of a VFD, a line reactor is a three-phase series inductance that impedes the flow of harmonic current onto the system. A dedicated filter is connected in parallel to absorb harmonics from the drive.
Isolation transformer: Installing an isolation transformer offers inductive reactance similar to a line reactor, but it has the added benefit of electrical isolation from high frequencies originating from other electronics from the utility or other loads.
Higher order drives: 12-, 18- or 24-pulse VFDs use phase shifting to cancel out lower order harmonics and reduce the total harmonic distortion from the VFD on the system.
The following solutions can be considered to mitigate harmonic distortion at the system level:
Tuned harmonic filters: A combination of a reactor and capacitor in series installed at a common bus is “tuned” to provide a low impedance path for certain harmonic currents. A harmonic study is often required for proper filter design and specification.
Harmonic mitigating and phase shifting transformers: K-factor rated transformers are designed to withstand excess harmonic currents, and multiple phase-shifting transformers can be used to cancel out harmonics on multiple parallel circuits.
Active filters: These advanced filters use sophisticated electronics and insulated-gate bipolar transistors (IGBTs) to inject equal and opposite harmonics into the power system to cancel out harmonics generated by other loads.
Harmonics pose a challenge in pumping, leading to increased operational costs and potential equipment damage. However, with advanced harmonic mitigation technologies, energy savings and improved process control, drives ensure the efficient and reliable operation of pumping systems while reducing the impact of harmonics.