Q. What dynamic analysis considerations are recommended for the petroleum market? A. End users should evaluate their need for dynamic analysis by considering the level of proven field experience available for any given configuration. The vendor and user should agree on which types of analysis should be performed at any level. Lateral, torsional and structural analyses are three identifiable and normally separable deliverables. In all cases, it is the user's prerogative to specify additional tests, validations and/or analyses to further mitigate risk. Historically, dynamic analysis trends have developed within the various pump application markets because of the types and characteristics of equipment typically used and as a result of past experiences. In the oil and gas industry, single-stage overhung horizontal pumps and between-bearings, one- and two-stage pumps must be designed to be classically rigid, which can eliminate the need for lateral dynamic analysis. Multistage pumps identical to pumps proven in-field are also not subject to lateral analysis. Vertically suspended pumps are required to be designed with established limits on bearing spacing to ensure suitable lateral rotodynamic performance. Drive system configuration and power levels determine the need for torsional dynamic analysis. High-energy, high-speed, critical-service and unspared machines are subject to high levels of customer intervention and scrutiny, with the user having varying definitions of these terms. For more information on dynamic analysis, refer to ANSI/ HI 9.6.8: Rotodynamic Pumps Guideline for Dynamics of Pumping Machinery. Q. What piping installation recommendations are important to consider for rotary pumps? A. Because rotary pumps are designed with close running clearances, clean piping is a must. Dirt, grit, weld bead or scale, later flushed from an unclean piping system, will damage and may seize the pump. Figure 3.4.3.11 illustrates pipe-to-pump alignment considerations.
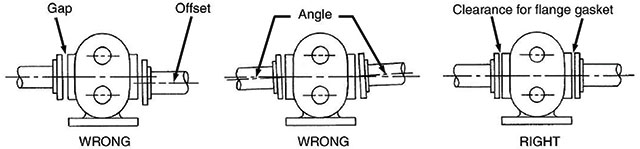