In the sealing industry, compatibility influences the ability to form a chemically stable system. Using the wrong hydraulic fluid could result in a violent reaction that is disastrous for the entire hydraulic assembly. The fix is not simple; it could cost thousands of dollars in repairs and lost production time. To avoid these problems, users should ensure that the lip material or sealing material is compatible with planned media. Any biodegradable upgrades or media improvements must also be compatible with the sealing elastomer.
Each year the U.S. uses about 200 million gallons of hydraulic oils. Of this volume, approximately 165 million gallons are mineral-based fluids. These types of mineral-based oils function at temperatures as low as -40 C to as high as 150 C with some exceptions. When choosing the right fluid, it is essential to assess physical and performance properties along with any original equipment manufacturer (OEM) approvals or specifications. Most fluid suppliers should be able to provide a product data sheet so that the design engineer can discern the best solution for the application.
Mineral-based fluids include specialty fire-resistant hydraulic fluids and environmentally friendly, biodegradable fluids. The International Organization for Standardization (ISO) acknowledges four major groups of fire-resistant hydraulic fluids: high-water containing fluids (HFA), invert emulsions (HFB), water glycols (HFC) and water-free fluids including synthetics (HFD).
Along with being fire-resistant, the chemical characteristics of HFA fluids are almost identical to that of plain water. As a result, this type of fluid is typically used in equipment that has been intended for use with water and is subjected to an open flame. HFA fluids are most commonly used in steel mills and coal mines. However, because these are fire-resistant fluids and not fire-proof fluids, HFA fluids can still ignite and burn, given the right conditions.
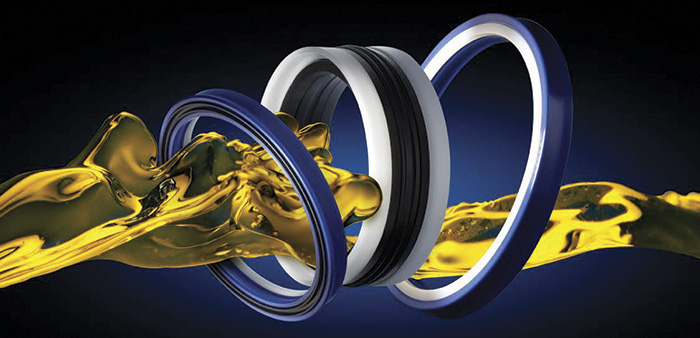
HFB fluids are made up of emulsions of water caught in oil with 60/40 oil-to-water composition. This type of fluid can sometimes perform to the level of petroleum oil and offers greater lubrication and corrosion resistance compared with HFA fluids. Its water content also acts as an extinguisher in case of a fire.
The most frequently used fire-resistant hydraulic fluid category is water glycols (HFC). While these fluids are comprised of only 35-45 percent water, they also include unique thickeners that boost viscosity. While HFC fluids can be used to run equipment designed for oil, severe damage to machine parts can occur due to an overwhelming environment if the speeds, temperatures or pressures are not monitored properly.
HFD fluids are classified as synthetic because they contain neither petroleum oil nor water. Polyol esters have an organic makeup that is biodegradable. HFD fluids are also compatible with system materials and provide exceptional hydraulic fluid performance. However, HFD fluids are more than double the cost of petroleum oil and are typically only used when the situation demands fire resistance and biodegradability.
Because governments have become more vigilant with environmental regulations, it is increasingly important to use a more eco-friendly fluid. For a product to be labeled an "environmentally acceptable fluid," more than half of it must decay within 28 days of exposure to the atmosphere. The fluid must be nontoxic after passing a series of aquatic toxicity tests on fish. The most common base for these environmental fluids is vegetable oil (or more specifically canola/rapeseed oil). Although they cannot be used as a direct replacement, the lubrication and anti-wear properties will be comparable to those of petroleum oil.
While eco-friendly fluids are becoming more available, the problem is that none of the current options can be used as a direct replacement in hydraulically powered equipment. There are drawbacks to using a minimally toxic hydraulic fluid. These fluids may be more vulnerable to oxidation and have a poor performance record in extreme cold weather, resulting in coagulation and problems cold starting. To increase stability and prevent problems with viscosity, vegetable oil producers have turned to genetic engineering to alleviate problems with biodegradable fluids.
If a plant decides to change the hydraulic fluid used in an assembly, personnel must consider the compatibility of the replacement fluid with the internal components of the machinery, ensuring that the seal lip material is compatible with the chosen application media. These materials range from standard nitrile Buna rubber, Viton and ethylene propylene diene monomer rubber to polytetrafluoroethylene (otherwise known as Teflon). Understanding how a seal material will interact with various fluids is the first step to finding the right match.
When choosing hydraulic oil, consider both viscosity and temperature. To prevent early internal component failure, the viscosity grade must match the operating temperature. The quality of the hydraulic should not be a factor; if it is not compatible, a system failure could result.
If the operating temperature of a hydraulic system is below the suggested level for the viscosity grade, the fluids can congeal. Solidified oil will not flow freely through the system, which can cause component seizures. The solidification can cause media to lose the ability to lubricate the hydraulic piston and increase the coefficient of friction undergone by the seal lip. The increased wear and heat will cause the seal lip to quickly deteriorate.
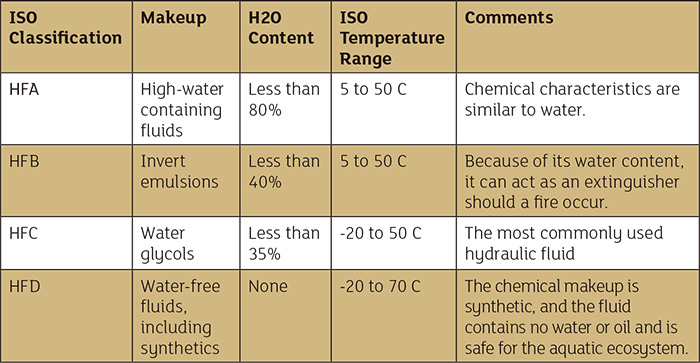
When switching to an eco-friendly hydraulic fluid, be prepared for different results from the interaction of the seal lip material and the fluid. Eco-friendly fluids can cause a shorter life for a traditional nitrile seal. Fluorocarbon is the best material for users who go this route. Always check with the fluid supplier before switching. Because biodegradable fluids have a different chemistry composition than petroleum-based fluids, the interaction with the seal lip materials could be an issue.
In a real-world example, a user experiencing premature hydraulic seal failure thought he had been sent either the wrong seal or the incorrect seal material. The seal provider discovered that the user had switched to a fire-resistant hydraulic fluid so that he could create a safer working environment. No research was done on how this change would impact his machinery and its components, including the seal.
The result was that the ethylene propylene diene monomer seal was not compatible with the new fluid. The seal was absorbing the fluid at an accelerated rate, causing the seal lip to swell. This swelling caused increased wear on the seal, resulting in decreased seal life and unacceptable leakage.
Contact your fluid or seal supplier for reference charts. They will have first-hand compatibility knowledge.