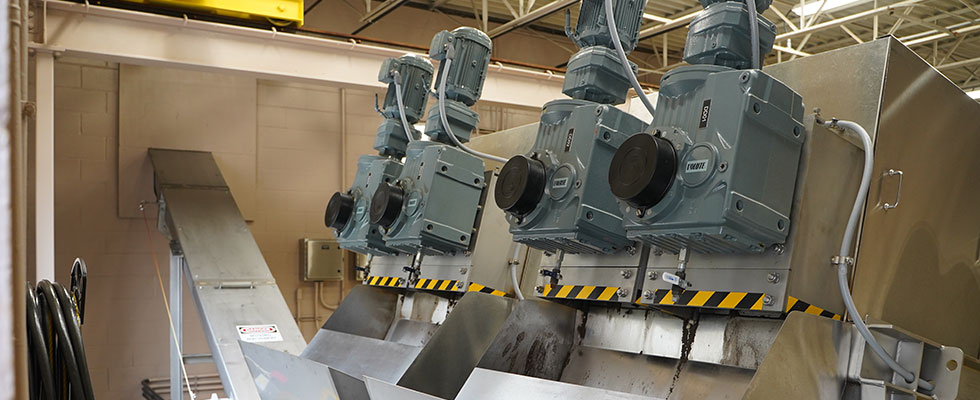
Long before the Clean Water Act required communities to treat wastewater, the city of Bentonville, Arkansas,
recognized wastewater treatment as a viable option for replenishing fresh water supplies and protecting waterways from harmful pollutants.
The Bentonville Wastewater Treatment Utility has successfully treated wastewater in a single location since the 1940s. The latest renovation to the location, in 1985, created an Activated Sludge-Extended Aeration plant still in use today.
The current wastewater treatment plant employs more than 20 professionals, including operators for 24-hour coverage, 365 days a year.
The Belt That Ran Its Course
When Bentonville built its most recent plant in 1985, the city purchased a traditional belt filter press to dewater waste bio-solids sludge. The belt press served its function well for many years; however, recently, the press required increasingly frequent repairs, even with proper preventative maintenance, and the plant had few options for parts.
Chris Earl, the manager of the Bentonville Wastewater Treatment Utility, explained the challenges of the aging technology:
“The belt press was about 35 years old, the last of a discontinued model,” Earl said. “It was starting to show its age and become a maintenance nightmare, so we decided to start looking at some different technologies.”
Screw Presses Meeting Modern Demands
Bentonville hired an engineering and environmental services firm to research practical alternatives for bio-solids dewatering systems.
Options included modern belt filter presses, screw presses and centrifuges, yet the most appropriate option is not simply a matter of preference. The best choice is often based on the specifications of a plant, including the main plant processes, hydraulics and loading rates and even the unique nature of the local sludge.
When evaluating dewatering technologies, Bentonville was attracted to the screw press. Like a traditional belt
press, a screw press uses a polymer to flocculate the solids and then squeeze them to create a semi-dry cake. Whereas the belt press sends the solids through multiple rollers fitted with filter belts, the screw press sends the solids through a porous casing using an auger.
After examining Bentonville’s needs, it was suggested that two screw press systems were needed for a pilot test: a traditional design screw press and a more modernized version that employs a dewatering drum. The modernized screw press design (sludge dewatering press) achieves thickening and pressing in one compact operation.
In Bentonville’s pilot tests, both screw presses performed well. However, the traditional press required a greater investment in infrastructure and installation ($9.1 million) compared to the sludge dewatering press, which better fit the belt filter press’s existing footprint and required minimal construction and installation costs ($1.1 million).
The city of Bentonville installed the sludge dewatering press in two months with little to no construction or installation challenges. The city completed the system and started service in January 2019.
The Results: A Piece of Cake
Bentonville was attracted to the design of the sludge dewatering press. The key feature is a drum design, which thickens and presses sludge in one compact operation. The design is an efficient means of dewatering, transforming feed sludge as low as 0.1% into cake, often over 20% solids. The efficiency has already created savings for Bentonville. The new screw press only requires nine days of usage per month (12 hours per day) compared to the old belt press, which required 22 days per month.
Additionally, to evaluate the effectiveness of the sludge dewatering press, Earl compared the average solids produced between the final year of the belt press and the first year of the volute dewatering press. In its final year, the belt press produced an average of 13.25% daily solids. In its first year, the volute dewatering press produced an average of 18.66% daily solids for a 28.5% increase in solids.
The new screw press translates to a dryer cake, which offers a benefit for disposal. The dryer cake means Bentonville is paying less to haul a greater percentage of solids. Earl also notes that currently, after fine-tuning the new machine, the city now produces 22% solids. Also, in its first several years of usage, the sludge dewatering press has required only minimal preventative maintenance.
“We’ve only needed to change the oil in the gear boxes and grease the things that need to be greased,” Earl said.
For the city, the benefits translate to more clean water in the environment and cost savings.
Finally, since installing the sludge dewatering press, Earl has enjoyed the pristine nature of the fully enclosed stainless-steel unit.
“Anybody who has ever dealt with a belt press knows there is always a mist in the air, a water in the air,” Earl said. “With this new machine, none of that is happening. It is so clean out there, you can almost eat off the floor.”