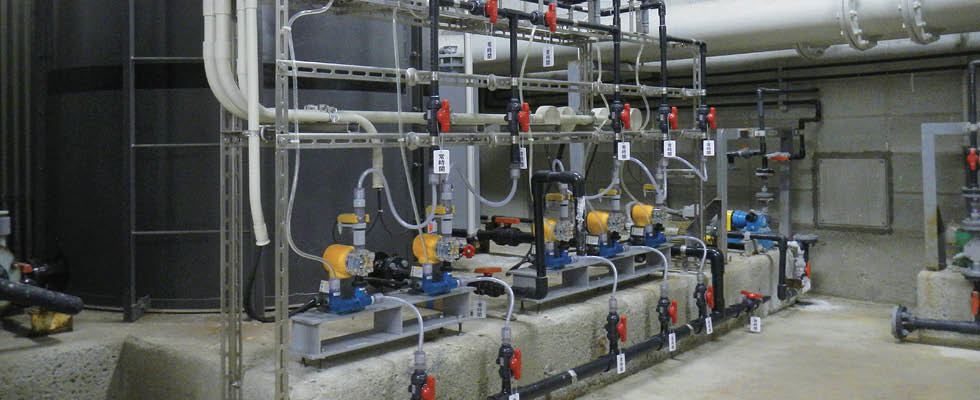
Used for water and wastewater treatment, sodium hypochlorite is usually a powerful, effective solution. It is known as
a common household liquid solution—bleach or liquid chlorine—but how it is used in a water or wastewater
application is much different than in a household environment.
This is often due to how it is applied to the stream being treated. Its primary purpose is to disinfect water and wastewater, as it effectively destroys microorganisms (bacteria, protozoa) and viruses residing there. With an effective application of sodium hypochlorite, the risk of waterborne diseases such as cholera, typhoid and hepatitis is eliminated.
Common Uses
There are three water or wastewater applications where sodium hypochlorite is widely used:
1. Drinking water treatment:
Sodium hypochlorite can inactivate a broad spectrum of microorganisms, so the operator can use one chemical rather than multiple solutions, each targeting a smaller number of microbes. This is usually added in the final stages of treatment to ensure the finished product is free of any waterborne diseases that could harm the end user.
2. Wastewater treatment:
Sodium hypochlorite is used to eliminate pathogens and control odor. Typically, it is applied in the final disinfection stages to hold microorganisms in check throughout the entire distribution process, not just when the chemical is added to the water.
3. Swimming pool disinfection:
Pools are the last place where you would want untreated or undertreated water. The fact that sodium hypochlorite acts quickly and is compatible with pool water greatly benefits those who treat the pool and those who use it. Sodium hypochlorite has the benefit of being inexpensive compared to other chemicals. Chlorine gas is much harder to handle and has vastly higher risks associated with its usage, and ultraviolet (UV) disinfection is much more expensive and complex to maintain.
As sodium hypochlorite remains in the water or wastewater throughout the distribution cycle, its long-lasting effects ensure safety for communities—both in drinking water and treated wastewater fed into the respective receiving streams.
Safety Considerations
What if users cannot properly inject sodium hypochlorite into the water, which then goes untreated or undertreated? This creates a huge risk for a community’s population, who expect proper treatment for drinking water, treated wastewater and pool water. One common issue with sodium hypochlorite is known as gas locking.
Gas locking occurs when sodium hypochlorite off-gasses for various reasons. These include elevated process fluid temperature or even the natural degradation of the fluid itself, as sodium hypochlorite loses effectiveness as it breaks down and releases its stored chlorine gas.
In almost every case, the sodium hypochlorite solution is injected into the water stream to be treated, creating a natural back pressure. The pump delivering the sodium hypochlorite must overcome the process system’s back pressure to effectively treat the water.
Herein lies the problem: Gas is more compressible than liquid. When enough gas has entered the flow path of the pump, the pressure created by the pump is not enough to overcome the compressibility of the gas, and gas locking occurs.
This prevents the pump from delivering the chemical needed for proper disinfection, as air often becomes trapped in the pump head and blocks the product from being delivered. What does that do to the disinfection process? It totally shuts it down and causes it to be ineffective at best, creating an unsafe environment for end users.
Solution Options
Gas locking is almost inevitable when using sodium hypochlorite for water treatment. So it is critical to have a solution capable of releasing large volumes of air from the pump, preventing gas locking. If it does not release the trapped air, it will shut off the flow of sodium hypochlorite, and the disinfection process will be compromised. A user could use a high-compression method, but this can still be an issue if a large amount of air is introduced into the pump head. The pump would not be able to produce enough pressure to overcome the gas lock.
Users may also use an automatic air release valve, but this is also problematic. It takes time for this valve to release the air completely, making the pump unable to discharge the needed disinfectant. In addition, it would need another line to return the discharge from the air release valve to the tank. What is needed is a way to allow the pressure in the pump head to equal that in the discharge-side piping. When the diaphragm is pushed forward, the pressure in the pump head increases, expelling the product and any entrained air. Technology is available to sustainably and viably address these issues with internal automatic air release mechanisms. There is no need for return piping as it is all internal to the pump.
Another feasible option is a pump inlet device combined with a pump type that automatically releases air in the system. This innovative device allows only fluid to enter the pump by first relieving any trapped air. This system is a good solution for reliability and process stability. Constant monitoring is also unnecessary, as little maintenance is required after the fact.
When choosing the best solutions for handling sodium hypochlorite, can users expect their capital cost to be higher? Yes, but they will find that the total cost of ownership is greatly reduced, concerns about adequate disinfection are vastly mitigated and their maintenance crew can work on other tasks.