Energy efficiency and minimal replacement parts make waste heat desalination a cost-effective solution to potable water making needs.
10/22/2013
The combination of vacuum enhanced distillation and waste heat recovery is a proven concept that has been used for more than 60 years. This tried-and-true method of desalination is making a comeback. Advances in technology have resulted in evaporators that:
- Are more energy efficient
- Offer a reduction in weight and installed spare requirements
- Are more reliable
- Offer a clear green advantage
How Heat Recovery Evaporators Work
Waste heat evaporators use waste heat from engine jacket water, engine exhaust, steam or other heat sources to transform seawater, brackish water or contaminated feed water into pure potable water that is suitable for human consumption, industrial processes, agriculture and many other applications. Operational efficiency can be further enhanced by adding additional evaporation stages and/or effects to increase the amount of fresh water produced using a reduced amount of heat.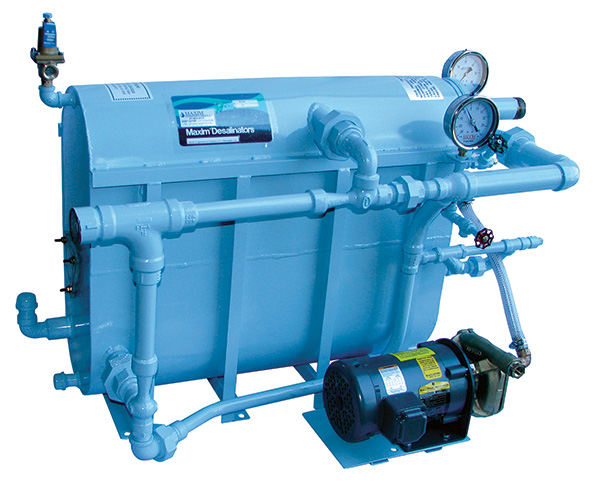
Applications
Heat recovery evaporators/watermakers extract high-quality salt free water from seawater using waste heat. Watermakers are used in the commercial shipping industry on oceangoing tankers and cargo vessels. The military has applications on aircraft carriers, destroyers and submarines in which highly reliable water production is critical for the mission. The oil industry also uses this technology on offshore oil and gas drilling rigs, production platforms and supply vessels.Advantages
Compared to other desalination technologies, heat recovery evaporators are advantageous for a multitude of reasons. Heat recovery evaporation is the most energy efficient desalination technology. Waste heat, normally discharged to the surrounding atmosphere, is used, which provides the bulk of the process’ energy requirements. Fuel efficiency on vessels is enhanced because the transportation of large tanks of potable water or bottled water is not required. More cargo space is also available when large amounts of water do not need to be stored. The water produced is high quality, containing less than 4 parts per million (ppm) of total dissolved solids, compared to other desalination technologies that contain 300 to 500 ppm of total dissolved solids of which at least 50 percent is salt. Heat recovery evaporators operate under vacuum conditions at low boiling temperatures, which minimizes the scaling of the heat transfer surfaces and the maintenance associated with cleaning. There are no high-pressure (700 to 1,000 psi) hydraulic components. Low-pressure systems, fewer moving parts and simple designs make these systems reliable. A heat recovery evaporator requires less maintenance than other technologies.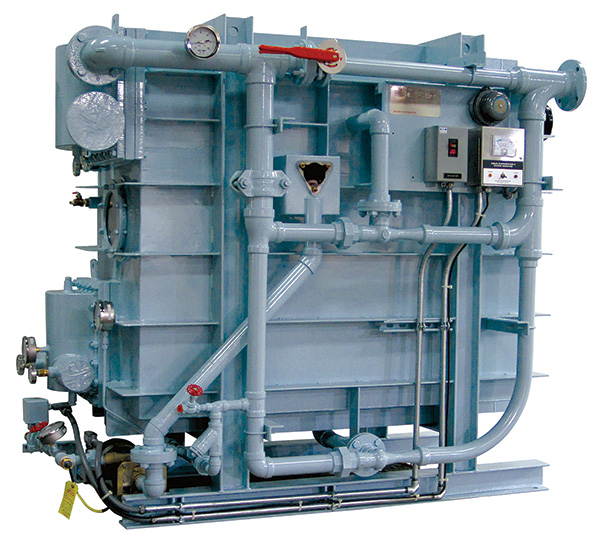