“For every complex problem, there is a simple solution…and it is wrong,” said the author H.L. Mencken. Although he was not referring to cost reduction opportunities in pump systems, the concept still applies. During the last several years, manufacturing executives and plant managers have focused on reducing operating costs to stay competitive in the global industrial marketplace. Many plant managers have adopted lean initiatives to optimize assets and streamline work processes with the hope of lowering operational expenses. Others have chosen to lower their costs by outsourcing for less expensive, non original equipment manufacturer (OEM) products and parts that may not offer the same quality or efficiency as the OEM equipment. While these solutions can lower initial costs, many “quick fixes” may lead to increased cost of ownership and lower institutional knowledge. What options remain for executives and managers who want to reduce operational costs without sacrificing critical plant equity? Fortunately, a fruitful area has been largely overlooked by plant personnel and consulting companies. Life-cycle optimization of pump systems, including supporting infrastructure, can significantly decrease the total cost of ownership. Life-cycle cost reductions far outweigh initial cost considerations, often by 10-to-1 or more.
A Holistic & Effective Path to Cost Reduction
To achieve the most substantial and lasting cost reductions, end users must first recognize the primacy of ongoing, recurring costs versus the initial purchase price of pump systems and parts. The equipment’s purchase price represents only about 10 percent of an industrial pump’s cost of ownership. When plant operators first recognize that a pump system’s total cost of ownership (TCO) is the higher impact metric than initial purchase price, they are well on their way to managing their costs, but they are by no means finished. Second and equally critical is the recognition, measurement and coordination of the factors that affect ongoing ownership costs. Some industry experts have begun to focus on energy and maintenance when evaluating life-cycle costs. While these two elements are certainly important, a plant manager must avoid taking too narrow an approach when evaluating a system. A holistic approach ensures that the big picture is not missed and that all potential opportunities for cost savings are identified. Taking a comprehensive approach when evaluating a pumping system is important. The process and tools can vary depending on the operator’s objectives. Four critical areas that should be evaluated in a plant environment are energy efficiency, reliability, training and asset management. The scope of cost-reduction projects should not be defined too narrowly, or substantial cost savings may be missed. Taking too narrow a view with any one of these areas will cost a plant money, time and effort in the long run..jpg)
A South American Copper Mine Elevates Efficiencies and Saves Millions
A great example of the need to evaluate both energy efficiency and reliability improvements occurred in a large copper mine operation in South America. The mine was using seven vertical-turbine pumps to move refino, an acid used in the extraction process. In this reclaimed water system, these critical pumps were not reliable. The plant approached a local pump repair shop to evaluate and modify these pumps with a request that the repairs improve reliability. The non-OEM supplier missed a key opportunity to fully evaluate the situation by deciding to focus solely on the reliability issue. Its solution was to increase critical tolerances, which in turn improved the mean time between failure (MTBF). However, these adjustments delivered a much lower efficiency and decreased throughput. Performance faltered, and plant operators saw flow reductions of more than 20 percent, while the pump head diminished more than 15 percent. Solving only a portion of the problem did not address the plant’s overall objectives. This adjustment to operations was counterproductive. Another repair service team evaluated the entire system and ultimately uncovered the root cause of the problem. The team worked with the mine operators and soon realized that the pumps were operating at an efficiency of only 64 to 68 percent, with a much higher potential. During the analysis, the team learned that the modifications by the local, non-OEM supplier, intended to improve performance, cost the plant millions of dollars per year in lost production. Furthermore, the parts and repairs did not meet specifications and created additional inefficiencies that cost the plant more than $500,000 per year in excess energy costs. To test theories on the plant’s problem, the repair service team built a precise pipe-flow model. They used identical parallel pumps and corresponding elevations, pipe fittings, valve flow coefficients, and pipe relative roughness and measurements showed that the model was 99.8 percent accurate. The repair service experts also advised the plant on how changing distribution nozzles at different elevations would affect flow. These changes allowed the team to increase and refine flow by almost 1,000 cubic meters per hour. With this approach, the result was a synergistic combination of increased efficiency, reliability and throughput for the plant’s pump system. The repair service team’s holistic approach convinced the mine operators to restore their pumps to OEM specifications and make other system changes to solve the original reliability problem. The elevated efficiency delivered substantial bottom-line benefits. Increased efficiency and higher flow rates increased mine production revenues by $10 million and delivered energy cost savings of $500,000 annually, demonstrating the payback of a thorough, multifaceted approach to cost reduction and productivity.Maintenance & Training
While critically important, correcting reliability and efficiency problems alone is not sufficient if a plant is to fully realize its cost-saving opportunities. Once the systems are optimized, changes must be institutionalized through effective training programs. Without education, unreliability and inefficiency will return.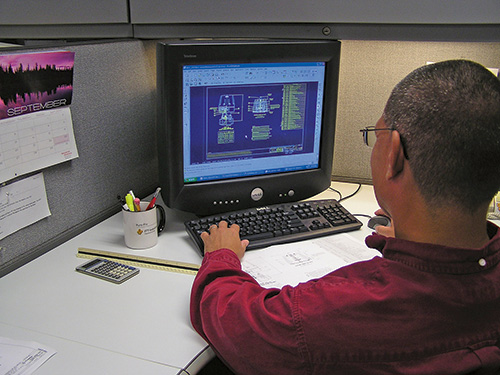
Problem-Solving in a Pulp & Paper Mill
Evaluating energy efficiency and reliability together is a comprehensive approach to identify problem areas. A repair and efficiency service company evaluated a large North American pulp and paper mill to find ways to reduce its energy and maintenance costs. The operators had previously attempted to reduce costs by implementing a repair program through a non-OEM shop. The OEM team conducted a plant-wide optimization assessment with targeted energy and reliability studies. The team worked with the operators to evaluate a system of more than 50 pumps and identify maintenance practices, pump configurations and energy savings opportunities. The result was that the team found numerous opportunities for energy reduction and reliability improvement, netting more than $750,000 in annual savings across the plant. The consultative and holistic approach to evaluating the mill’s reliability problems avoided a limited focus of only looking at energy. By evaluating the whole spectrum of operating costs, the team delivered a trifecta of reduced energy and maintenance costs with higher runtimes, saving the plant thousands of dollars annually in energy and reliability.Effectively Managing Assets
Large cost reductions can also be achieved through proper management of assets. Poor record keeping or a lack of any record keeping can cause plant managers to make costly, uninformed decisions. Often the financial implications of these decisions can ripple through a plant and add up to substantial losses.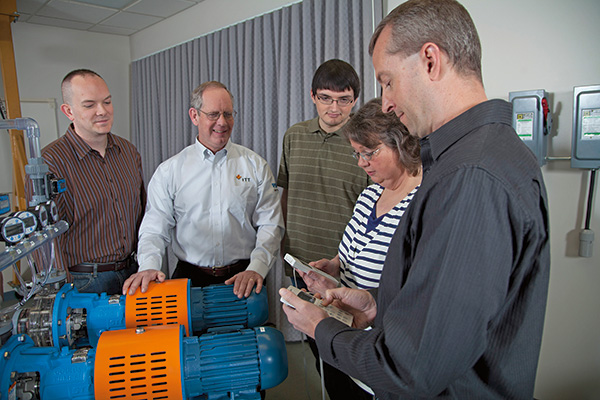
- A description of the work requested
- A description of the actual work completed
- The number of hours required to complete the work
- The parts used
- The total cost
- All failure codes and causes
- Recommended follow-up actions