Kids usually master new technology quickly. They use Facebook, iPhones, iPads, Xboxes—all things digital. Common to all these devices and technologies is the integrated chip (IC). Pump users, on the other hand, have not been as quick to adopt this new technology.
Egyptians were the first to use pumps to hoist water from the Nile River for drinking and irrigating their fields. In fact, pumps started the industrial revolution. Thomas Savery developed the first commercial steam-powered device—a water pump. These quintessential machines survived through the years. If these divergent technologies were married, a technology disruption may occur.
Michio Kaku, theoretical physicist and futurist, says in his book, Physics of the Future, that every time the IC has entered a product, it revolutionized that industry. IC entered large, unwieldy telephones, and the market for smart phones exploded. IC entered cameras and digital cameras, turning the industry upside down. Industry stalwarts were caught off guard and are fighting to retain and revamp their business models and market approaches.
Integrating pumps produces new technologies. An important one of these is smart pumps, which can sense, think and then act on their own. Another offspring—wireless and remote communication—gives pumps the ability to communicate with other systems and be remotely controlled. Together, wireless and remote communications form machine-to-machine (M2M) communication.
While smart pump technology is not yet widely in use, M2M is slowly transforming the way end users interact with their pumps. Frost & Sullivan’s recent “North American Machine-to-Machine Software and Services Market” analysis and upcoming research on intelligent pumps provide a detailed evaluation of these technology trends, the impact on the pump market and the growth potential for pump manufacturers. This article discusses excerpts from those analyses on M2M and pumps.
M2M Communications
M2M is defined as the transfer of data from an electronic device that is mounted on an asset—such as a pump or compressor—through a wired or wireless communication network, connected to a software platform or a centralized control system that translates that information into useful data for the end user. Solution providers are constantly developing platforms to extract raw data from devices to create business insights for end users who want additional functionality from their existing connected devices.
Several key advantages are associated with using M2M. One is the remote monitoring of assets. Users can track critical process equipment in remote locations. This creates multiple cost and safety benefits because personnel do not have to go to the site for information. Additionally, some technology allows the customer to remotely control the asset, saving companies money on service management. From monitoring assets in the oil and gas industry to remote health monitoring in the health care industry, the benefits of adoption are clear.
Another advantage is the increase in operational excellence and improvement in process efficiency. Operational efficiency and process optimization are key contributors to the success of any organization. Using M2M, end users can collect, store and analyze key information and performance metrics that can help enhance process efficiency and reduce costs, which in turn increases operational excellence. Streamlining operations is achievable not only within the organization, but also in their extended supply chain, which in the current market scenario is extremely complex.
Evolution of M2M
As seen in Figure 1, the evolution of M2M technologies resulted in several end user verticals that saw the benefits of adoption. Many industries that traditionally used M2M technologies to monitor their distributed assets (such as equipment, workforce and operations) want to use the raw data to analyze key performance metrics, further enhancing the productivity of their assets at the site. As digitization continues, M2M will play a key part in enhancing visibility across the enterprise by gathering relevant data from almost any asset, converting that data into actionable insights and mapping the data with other business systems.
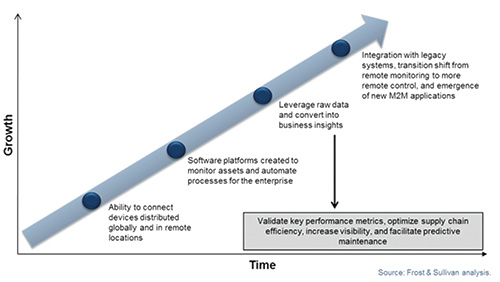
In general, the process industries harbor tremendous potential for M2M. A quick review is included in this section.
Oil & Gas Industry
Oil and gas in particular offers the highest promise as end users try to integrate process equipment for system control to ensure maximum profitability. For example, an international oil and gas major would have resources—such as subsea wells in the Gulf of Mexico, oil producing wells in the Middle East, gas wells in Qatar, oil wells in the North Sea and shale gas wells in the U.S. These are closely integrated with control systems—such as distributed control system (DCS) or supervisory control and data acquisition (SCADA)—which in turn are closely integrated with enterprise or business management systems, such as enterprise resource planning (ERP).
If the company determines that demand exists in Eastern Europe and more margins are to be made, then it might increase production in the North Sea while reducing production in the Gulf of Mexico. Conversely, if more demand for liquid natural gas (LNG) from Japan exists, it can increase gas production in Qatar. This integration helps them be agile and generate more profit based on rapidly changing market demand.
Other Process Industries
Process industries adopt M2M to reduce operational costs and improve process efficiency. Many process industries—such as chemicals and oil refining—are experiencing increases in investments because of shale activity in the U.S. The industry is faced with an aging workforce at the same time that new capacity is needed, placing significant pressure on industries to find and train the next generation of operations and maintenance personnel. In the near future, a larger number of employees are likely to retire within a short time span, and the need to find qualified employees to replace them will become acute.
M2M enables data collection and remote control from process equipment. Much of the maintenance can be completed remotely, reducing the requirement for onsite service personnel. Moreover, by connecting the process equipment to the automation control system, end users can optimize pump operation, increasing process efficiency.
Key Concerns
One of the biggest concerns in the M2M space is a lack of standards for the devices and software. Without clearly defined standards, costs incurred because of deployment and optimal use are restraining the adoption of M2M solutions. With many software providers present in the M2M space, end users have difficulty mapping their existing legacy systems to this new technology because of the different protocols with individual devices and platforms.
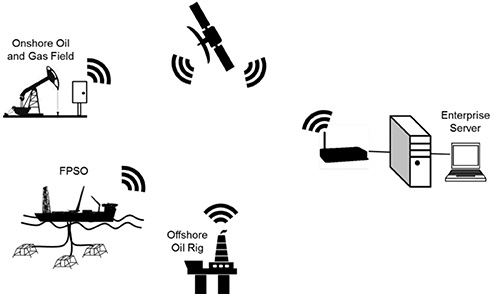
Application platforms are usually specific to individual vertical markets, and a customized, off-the-shelf solution that accommodates a number of vertical segments is needed.
Another key concern is security. As end users take advantage of their custom-built devices and software, they may have no way to ensure that the communication network is secure. Since the data is transferred across different media, permissions, controls and supports, major security issues can arise for data transfer between M2M devices.
The Future of Intelligent Systems
The M2M market for pumps is expected to grow rapidly. Unfortunately, many pump manufacturers do not have the ability to manufacture or integrate electronic solutions to their products. As a result, distributors and system integrators are currently filling the gap. This reduces pumps to a component in a large solution, decreasing competitive advantage and commoditizing the pump.
While large manufacturers acquired such capabilities, the way forward for smaller manufacturers is to partner with M2M solution providers. A major discussion thread in the industry right now is: how is this current model going to play out as adoption increases? Will manufacturers develop a larger role in creating, driving and selling intelligent pump systems? Or will the distribution channel build capabilities and expertise to own most of the intelligent pump revenues that are available? How this plays out is one of the most interesting trends in the pumps space today and will continue to drive thought leadership discussions throughout the industry.