One of the major problems facing industry is the limited number of people with sufficient skill and experience to diagnose and rectify the basic problems plaguing centrifugal pumps. Another difficulty is that the same lack of skill and experience is creating many of these problems in the first place. A detailed evaluation of a pump problem requires a depth of knowledge which usually surpasses that to which most people are ever exposed. Most pump engineers, operators and maintenance people develop their knowledge base from the same "school of hard knocks." While this on-the-job type of training has much to commend it, unfortunately it exposes the pupil to the opportunity of learning the mistakes and misconceptions of others. At best, it only teaches what is necessary to execute a particular job function in exactly the same manner as it was previously performed-good or bad!
The ramifications are generally imposed on the maintenance department, where the training is usually limited to the physical change-out of the parts when a breakdown occurs. As the underlying cause of pump failure often extends beyond the failed item, these maintenance methods will effectively reinstall the same old problem.
This is particularly concerning when we realize that over 80 percent of all pump failures tend to manifest themselves at the mechanical seal or the bearings, which then act in a manner similar to a fuse in an electrical system.
When a fuse in an electrical system fails, it does not mean there is anything wrong with the fuse. In fact, we understand that the problem is almost always somewhere else in the system. Despite this, when a seal or bearing fails, we rarely look for the real problem. Instead, we simply replace the offending part. While that will occasionally solve the problem, simply replacing a seal or bearing rarely provides long-lasting relief from the problem.
The extent to which this happens varies from industry to industry, as some are more aware of the root causes of pump failure than others.
Pump Failure Analysis
As there are only a few symptoms with which to recognize a troubled pump, the key to failure analysis lies in understanding how the combinations of symptoms identify the underlying cause of the problem.
Speed of Problem Occurrence
An effective pump troubleshooting tool will always begin with the question, "When did this start?" If the problem has only suddenly appeared, it is likely to have a different cause than a similar problem that has been developing over time. It is also fairly obvious that a sudden appearance of the problem is probably caused by a sudden change in the condition that created the problem. Therefore, it is highly unlikely that such a problem can be attributed to normal wear and tear. It is much more probable that an inappropriate action has been initiated.
It can be argued that the exception to that concept is where wear gradually takes place until the point at which failure suddenly occurs. In this case, however, the wear is usually indicated by a gradual reduction in performance until the breaking point is reached, which provides some prior notification of imminent failure. This type of condition underscores the need for constant performance measurement as it relates to temperature, pressure, flow, vibration and power draw.
Frequency of Problem Occurrence
A typical example of this problem is when a mechanical seal in a particular pump fails every six months, regardless of the type of seal used in that pump. Maintenance may have tried many different models, types and face material combinations, but the seal fails with the same frequency every time. As it is logical to expect different seals to last different periods of time between failures, it becomes evident that this is a situation where the seal is simply acting as the "fuse" in the system. Consequently, the underlying problem is obviously elsewhere in either the pump or the system.
Skill and experience come in to play here. The above condition is one where the experienced troubleshooter would immediately consider either the pump shaft or the piping arrangement, depending on the pump model in question.
Hydraulic Imbalance in a Double Suction Pump
A horizontal, double-suction pump may be fitted with a 90-deg elbow mounted on the suction nozzle in such a way that the line leading to the elbow is parallel with the axis of the pump shaft (see Figure 1). When the liquid sweeps round the elbow, it is centrifuged out towards the long radius and feeds the eye on one side of the impeller, effectively starving the opposing eye. This creates an imbalance of the liquid in the pump casing that can cause an excessive axial thrust to be imposed on the impeller.

The normal outcome of such an arrangement is a consistently frequent failure of the mechanical seal or bearing (when packing is fitted) at the end of the shaft closest to the suction source. Such failure will normally occur at approximately 6-month intervals regardless of the type of seal or bearing installed.
Undersized Shaft in an End Suction Pump
In a horizontal, end suction centrifugal pump, frequent and regular seal failure with different seals indicates an undersized shaft subjected to excessive deflection.
The same thing is true of a packed pump that cannot maintain a minimal amount of leakage for any length of time and seems to be constantly leaking excessively regardless of the amount of time and expertise spent on minimizing the leakage. This problem is frequently blamed on the last individual who repacked that pump, or even on the type of packing used, resulting in many different packing styles being tried. In this case, the underlying source of the difficulty is also an undersized shaft that is subjected to excessive deflection.
Under ideal operating conditions where the pump will be running at the Best Efficiency Point, the radial forces exerted on the shaft through the various hydraulic loads on the impeller will be minimal and not affect the shaft. However, when a pump is not operating close to the BEP, the radial forces exerted on the shaft through the various hydraulic loads on the impeller will be excessive and have a tendency to deflect the shaft.
This problem is negated when the pump in question is of a double volute design in which the radial loads are balanced and have minimal effect on the shaft.
In most end-suction, single volute process pumps, the amount of deflection that will take place will depend on the effective diameter of the shaft. If the effective diameter is large enough, the deflection will be minimal. However, if the effective diameter is too small, then the deflection will be excessive and cause premature seal and packing failure, as described above.
If the shaft sleeve is shrunk onto the shaft, the effective diameter will be the sleeve diameter. However, if the sleeve is secured by a hook design or is keyed to the shaft, the effective diameter becomes the diameter of the shaft under the sleeve. This results in a much weaker shaft that is almost twice as susceptible to deflection in the event of a hydraulic upset condition such as that which may occur close to the shutoff point on the curve.
Cavitation
A predominant condition requiring troubleshooting expertise in centrifugal pumps is referred to as cavitation. More paragraphs have been penned on this topic than on every other aspect of pumping combined, yet the vast majority of the world's pumps have never experienced the problem. However, there are enough pumps subjected to cavitation for us to review the matter in some detail.
To anyone who works with pumps, the symptoms of cavitation are relatively familiar: a unique rumbling/rattling noise and high vibration levels. Closer inspection will also reveal pitting damage to the impeller and a slight reduction in the Total Head being developed by the pump. To consistently avoid or cure these problems, it is important to understand what cavitation really is and what causes it in a centrifugal pump.
Cavitation is a two part process caused by the changes in pressure as the liquid moves through the impeller. As the liquid enters the suction nozzle of the pump and progresses through the impeller, there are a number of pressure changes that take place, as shown in Figure 2.
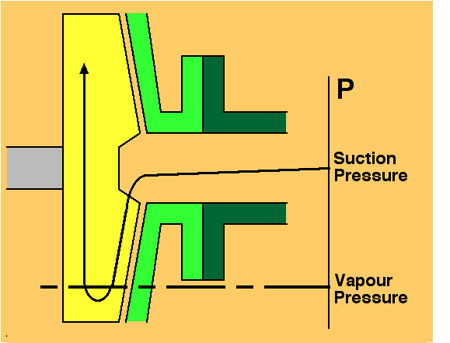
As the liquid enters the pump through the suction nozzle, the pressure drops slightly. The amount of reduction will depend on the geometry of that section of the particular pump and will vary from pump to pump. The liquid then moves into the eye of the rotating impeller where an even more significant drop in pressure occurs.
The first part of the cavitation process occurs if the pressure falls below the liquid's vapor pressure in the eye of the impeller. This causes vapor bubbles to be created in that area (in other words, the liquid boils!). The second part of the process occurs as the centrifugal action of the impeller moves the bubbles onto the vanes where they are instantly re-pressurized and thus collapse in a series of implosions.
While a single such implosion would be insignificant, their increasing repetition and severity develops energy levels well beyond the yield strength of most impeller materials. At this stage, the impeller starts to disintegrate and small cavities are created in the metal. This condition also creates the noise and high vibration levels mentioned earlier.
When considering Figure 2, it is evident that the problem results from the pressure of the liquid dropping below its vapor pressure in the eye of the impeller. This is what creates the vapor bubbles in that area. Consequently, cavitation can usually be avoided or stopped by simply increasing the pressure of the liquid before it enters the suction nozzle of the pump. This will ensure that the pressure in the eye area does not fall below the vapor pressure, so no vapor bubbles will be created and no cavitation will exist.
Much of the critical pressure drop that is created as the liquid moves into the eye of the impeller can be attributed simply to the loss of energy of a liquid moving from a static environment (the pump suction) to a dynamic environment in the rotating impeller. However, it has been suggested that other design factors may occasionally play a part, such as the entrance angles of the impeller vanes as they relate to the velocity of the liquid.
Confusing Conditions
The reason cavitation continues to be a difficult problem to correct on a consistent basis is that its classic symptoms are shared by three other conditions. This means that when we experience the unique noise and high vibration levels, they could also be caused by suction or discharge recirculation or by air entrainment, all of which have little to do with cavitation or suction pressure.
Suction Recirculation
This condition results from various types of instability such as turbulence, backflow circulation and swirling actions that can occur in the impeller when operating the pump at a low flow rate. Sometimes referred to as "separation" or "hydrodynamic" cavitation, these flow patterns tend to double back on themselves under low flows. Unfortunately, the flow rate at which this occurs will vary from one impeller to the next. Frequent occurrences at flows lower than 30 percent of the BEP have been identified, while others have it tagged as high as 80 percent.
While some industries favor a model that identifies recirculation occurring at the eye of the impeller, physical evidence in other industries shows the pitting damage almost halfway along the vane. It would also appear as though the impeller design contributes to a condition where that damage could be on either the leading or the trailing side of the vane.
In a nutshell, suction recirculation happens when the pump is operating at low flows, and the pitting damage normally occurs about halfway along the vanes.
Discharge Recirculation
Discharge recirculation is a similar occurrence that results in pitting damage at the tip of the vanes and sometimes at the cut-water of the casing. It can also be caused by operating the pump at low flow rates.
Air Entrainment
Air entrainment defines a variety of conditions where the vapor bubbles are already in the liquid before it reaches the pump. When they arrive in the eye of the impeller, exactly the same thing happens as if they were created at that point. In other words, the vapor is subjected to the increasing pressure at the start of the vanes and is thus imploded, causing the identical damage as cavitation, and at the same location.
This condition can often be a result of pumping fermenting liquids or foaming agents found in a wide variety of industries. It can also be a result of pumping a liquid, such as condensate, that is close to its boiling point.
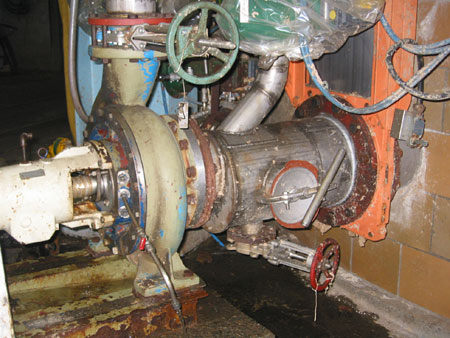
However, air entrainment is most frequently caused by turbulence in the suction line, or even at the suction source. For example, the kind of inappropriate piping conditions in Figure 3 will cause turbulence in the suction line that will create vapor bubbles moving into the pump suction.
A similar condition can occur if the pump is drawing suction from a tank in which an agitator or fluid mixer is operating. These problems can frequently be minimized by the use of appropriate baffles in the tanks, if such a condition is feasible.
Turbulence in the suction lines to a pump can also be created by using too many elbows in the line. Even one elbow located directly onto the suction flange of the pump can create enough turbulence to cause air entrainment. If there are two elbows close to each other in the suction piping in different planes, the liquid will exit the second elbow in a swirling fashion that will cause considerable turbulence. This will create an air entrainment problem for the pump by causing pockets of low pressure in the liquid flow in which vaporization can occur.
The ideal situation is to provide the suction side with a straight run of pipe, in a length equivalent to five to 10 times the diameter of that pipe, between the suction reducer and the first obstruction in the line. This will ensure the delivery of a uniform flow of liquid to the eye of the impeller and avoid any turbulence and air entrainment.
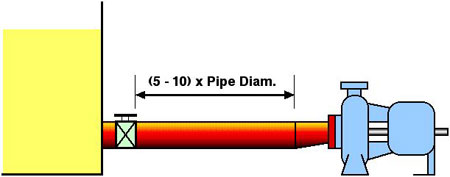
As air entrainment causes the same pitting damage to the impeller in precisely the same location as cavitation, it can be a little confusing, particularly as both can occur simultaneously in the same service. However, a quick comparison of the NPSHA and NPSHR, combined with a visual review of the piping characteristics will usually help identify the root cause of the so-called "cavitation" and solve the air entrainment problem.
Similarities and Differences
Cavitation, air entrainment and recirculation all result in pitting damage on the impeller caused by the formation and subsequent collapse of vapor bubbles. The difference between them lies in the method by which the bubbles are formed and the location of the resultant impeller damage.
As the severity of all these conditions increases, the noise, vibration and impeller damage will also increase. Under severe conditions, the pitting damage will spread throughout the impeller and may also extend to the casing.
All these conditions share some similar symptoms. As a consequence, they can be diagnosed incorrectly. However, they are caused by three separate conditions and, by focusing on these root causes, an accurate diagnosis can be simplified.
It must be recognized that the harmful effect on the impeller is only one consequence of these conditions. The bigger problems come from the subsequent vibration and its detrimental effects on seals and bearings.
Cavitation Troubleshooting
The biggest problem overall is identifying which of three hydraulic conditions are present when the common symptoms of noise and vibration are experienced.
This is accomplished by the throttling of the discharge valve, which reduces the flow through the pump and creates three possible scenarios:
With the first result, the pump will be operating at a lower flow where a lower level of NPSH is required, and the quieter, smoother operation identifies that cavitation is being eliminated.
If the noise and vibration gets worse, it indicates that the pump is moving into a worsening condition of low flow which demonstrates a problem with recirculation.
When little difference is experienced, that indicates an air entrainment problem that is not immediately susceptible to changes in flow rate.
Conclusion
In general, it can be stated that any troubleshooting exercise must be undertaken with an open mind and a principle desire to find a solution and fix the pump, not simply to assign blame. Excellent observation and communication skills are necessary in all such endeavors.
This article first appeared in Pumps & Systems, November 2008