First of Two Parts Operators in refineries or chemical/petrochemical plants must keep greenhouse gas (GHG) and environmental regulations for fugitive emissions in mind. One area in which this is extremely important is the processing of oil sands in Canada. Fugitive emissions are any chemical in physical form that can leak unanticipated within an installation. Knowing how to select valves that will meet or exceed volatile organic compound fugitive emission limits is critical. The costs are exorbitantly high if an operator fails to meet the requirements. End users should obtain test data that will allow for direct comparisons between valve packing, gaskets and other sealing components. Without data, end users are guessing which options are best for their applications. The operations/field data, including past experience, helps analyze the valve and packing options. Most companies require real-time testing, which will provide comparable fugitive emissions in parts per million (ppm) of hydrocarbons and chemicals. These tests include multiple test cycles that represent the plant conditions within a laboratory. These tests can be conducted at reasonable costs and within a reasonable timeframe. A few laboratories in North America are qualified and have developed a simple test procedure that can be adjusted to accommodate any off-the-shelf valve and provide the fugitive emissions in ppm, which is needed to understand how a valve will perform once it is in service. Part One of this series discusses how to eliminate fugitive emissions in valves already in service. Part Two will cover the current standards and testing procedures to ensure compliance with these standards.
Why Focus on the Fugitive Emissions of Valves?
The industry statistics indicate the importance of discussing the fugitive emissions of valves specifically. Valves account for more than 51 percent of fugitive emissions, and GHGs are part of this (see Figure 1).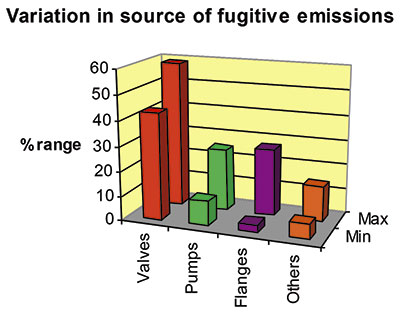
- Design of sealing components
- Selection of materials
- Prototype qualification of valves
- Production test of valves
- Fugitive emission compliance onsite
Control Strategies
The key elements for effective, long-term control of fugitive emissions are:- The application of the best available technology and standards, including the development of monitoring programs, operating procedures and performance objectives for controlling fugitive emissions Implementation of management systems
- Corporate commitment to the implementation and maintenance of a directed inspection & maintenance (DI&M) program to detect and prevent leaks
- The first step in controlling fugitive equipment leaks should always be to minimize the potential for leaks at the beginning by applying proper design and material-selection standards, following the manufacturer’s specifications for the installation, using and maintaining the components, and implementing practical control technologies (such as reduction, recovery and treatment systems).
DI&M Program
The first step is to determine which types of components will be targeted for regular leak screening. The objective is to minimize the potential for leaks in the most practical way possible. This is accomplished by focusing the efforts on the types of components and service applications most likely to offer significant cost-effective control opportunities. Non-target components are subjected to coarse or less frequent screening. Typically, a facility will phase in the DI&M program across a certain number of years by progressively adding to the list of targeted components until all key components are targeted. Once a leak is detected, regardless of whether it is a target or non-target component, the decision must be made whether to repair the leak. Once the maintenance professionals or operators have decided to repair a leak, the repair should be completed within a reasonable period of time or at the next facility turnaround if a major shutdown is required. A facility may simply choose to repair or fix the leak. If it is not a simple repair, an operator may choose to schedule the repair during the next shutdown without quantification, or alternatively, the leak should be measured or estimated to determine if it is economical to repair or too dangerous to wait for repair. If an operator determines that repairing the leak is not economical, this should be documented based on reliable quantification of the amount of leakage and the repair costs. If a leak poses a health, safety or environmental concern, then it must be repaired regardless of economics. Fugitive emission control is becoming more common as a condition of a facility’s operating approval. Accordingly, it is useful to consider a definition that corresponds to those typically applied in other industries. A leak may be defined as a screening concentration of 10,000 ppm or more for the purposes of deciding whether to measure the emission rate and evaluate the practicality of making repairs. Below this threshold, the emissions generally become too small to quantify. Moreover, only the top 5 to 10 percent of leaking components usually account for 80 to 90 percent of the emissions at a facility. As a result, limited value is achieved in dedicating resources to measure or estimate emissions from components that do not meet the screening value identified. However, facilities may still choose to repair leaks that are below 10,000 ppm. Several emerging technologies have the potential to improve the efficiency and effectiveness of leak detection programs and replace U.S. EPA Method 21. These technologies include:- Differential lasers to measure atmospheric concentrations of component gases
- Computer analysis of ambient air sample trends to estimate leak source location and volumes
- Infrared optical technology to visually inspect the components
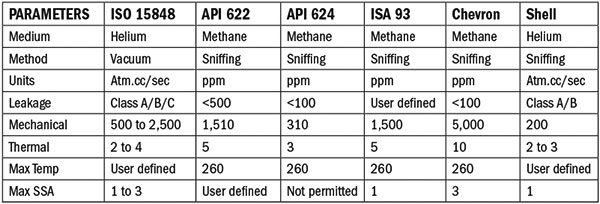