Not all valves are made for every application, but some valves are best at handling the worst conditions. For this reason, a standard process valve may not function well in difficult, abrasive or harsh applications. Finding the best valve for more difficult applications may be a time-consuming and costly exercise.
In many process plants, standard valves may be installed in challenging applications, and they may perform horribly, needing frequent repair. Those same valves may be modified to improve performance, or perhaps plant personnel should search for a better designed valve specifically for the application.
Heavy slurries present challenges in many process industries. Slurries typically involve minerals that can be abrasive to traditional valves. Abrasive slurries are difficult for conventional valves.
Lime slurry is common in many industries—such as chemical processing, steel manufacturing, pulp and paper, mining, and power generation. It can be found in a powder or liquid form. Lime has different characteristics compared to clean or pure chemicals. It is abrasive and tends to scale in pipelines, valve components and instruments.
Lime Slurry Characteristics
Limestone is mined from quarries as calcium carbonate (CaCO3). It is then crushed and fed into a kiln at approximately 2,000 F, where the carbon dioxide is burned off (calcining) to make calcium oxide (CaO).
The CaO is ground into a powder in either a tower mill, spiral classifier or a slaker. Milk of lime is used for many industrial purposes, such as:
- pH control
- Paper filler
- Power flue gas cleansing
- Calcium extraction in food and pharmaceutical applications
- Glass manufacturing
Lime particles do not dissolve but are suspended in solution. The particles are jagged and abrasive. Because lime is suspended in solution, any cracks, crevices or void areas in valves and piping systems allow for lime particle accumulation. Lime further aggravates this situation because it hardens in these collection points. The lime changes to a solid mass of material commonly referred to as scaling. Scaling causes a pipeline’s inner diameter to become progressively smaller and often causes valves to freeze in position because of material buildup on the seats and other surfaces. Because of these characteristics, the use of lime often leads to a long and potentially expensive trial and error approach to find the best process equipment to handle this substance.
Valve Requirements
Valves and instrumentation that will be used in lime slurry applications should have limited cavities, cracks and void areas. Even a small collection point can cause certain equipment to seize and become inoperable, which creates downtime and maintenance issues. Some plant operators oversize the actuator of plug and ball valves with the hope that this will improve the problem. They may increase the actuator size so it is capable of having an output that is roughly two times the normal manufacturer’s recommended torque requirement in clean liquids. This size increase may improve performance and downtime that results from sticking valves, but it will not solve all the maintenance problems.
Ball & Plug Valves
Many ball and plug valves will be severely affected by lime. Using a cobalt-alloy-coated ball or other hardened materials can help protect valves against abrasion. Valve seats can also be a major concern, and hardened steel seats with a scraping edge are the best alternative in lime applications. Scraping hard-coated metals will improve the equipment’s performance and reduce scaling by removing material buildup from the ball and plug surfaces.
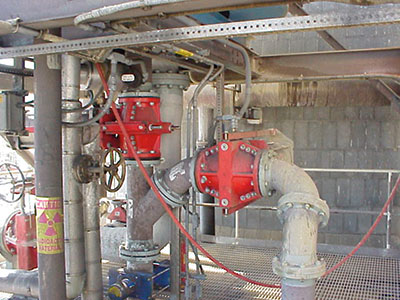
Most polymeric seats will not stand up over time in lime slurry. The scaling that occurs in these valves is like a wrecking ball to most polymeric seats. The ball or plug is turned with the scale buildup through these seats, and their lifetime is usually short because of this wear. Because these valves have cavities in which the ball or plug is housed, substantial material may accumulate there with time. If possible, flushing ports should be installed in the valve so that water cleans the accumulated material out of the body cavity after each cycle.
To summarize, if ball or plug valves are oversized to double the actuator torque, end users should include cobalt-alloy seats and all ball or plug surfaces should be made of a cobalt-alloy as well. The use of effective scraper seats and flushing ports would also improve the valve’s function.
Building a ball or plug valve including all these features can be expensive. The cost of a ball or plug valve equipped with these features may be five to six times more expensive than a traditional polytetrafluoroethylene (PTFE) seated ball or plug valve. Unfortunately, most PTFE seated ball or plug valves will not perform satisfactorily in lime slurry.
Gate & Knife Gate Valves
Gate valves or knife gates can be used in slurry service. With many gate valves, end users must be willing to sacrifice tight shut-off when they are used in lime slurry. Most gate valves have a wedge in which the gate is forced to close the valve. Knife gate valves have a sharpened edge to improve the ability to cut through solid particles. In lime service, the seating area will accumulate material/scale, making valve operation and sealing completely against line pressure difficult.
The most effective gate valve for lime slurry is a push-through valve with substantial rubber seats that allow the accumulation to be discharged from the bottom of the valve (see Image 2). These knife gates using rubber sleeves are unique, and the rubber sleeves are the only components that contact the medium when the valve is open. In some cases, the leading edge of the knife can be hard surfaced—cobalt alloy or some other material—that is capable of protecting the softer steel blade.
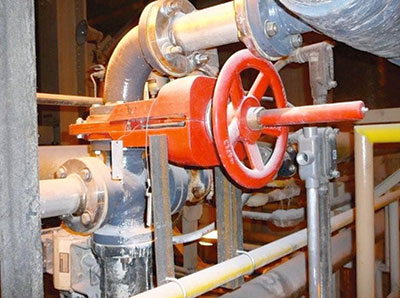
In traditional metal-to-metal seating knife gate valves, the actuator forces should also be increased to allow the valve to cut through or close tightly against the lime buildup in the wedge. Finally, a PTFE-coated gate may be desirable to help prevent the lime from scaling on the gate and the sticking of the gate itself.
If the gate is not coated with PTFE, end users may experience scale buildup on the knife, and this will most likely result in packing problems. The scale will accumulate on the knife, and as the knife is opened, the scale buildup will be dragged through the packing. This will result in increased forces required to open the valve. Also, the packing may be severely damaged as this material is dragged across it. In most knife gates in lime applications, end users will experience significant packing leaks.
Pinch Valves
Because of their straight-through design with no crevices or cavities for material collection, pinch valves are a good solution for lime service. A pinch valve is an effective device that self-cleans scale. How does a pinch valve self-clean? Inside a pinch valve, a rubber tube or sleeve is pinched by steel bars on the centerline of the valve to close it. To close the pinch valve, the rubber sleeve, which is full bore, begins to stretch. As it begins to stretch, the material or scale buildup begins to flake. As the sleeve continues to close the valve, the flaking increases, but the fluid velocity also increases substantially. Therefore, the flaked material/scale is blasted with higher velocity flow from the elastic surface of the rubber sleeve.
Pinch valves also help prevent abrasion. Rubber is often used in handling abrasive materials. Common uses are in rubber lined pipes, pump linings and wear points or high velocity points in various processes.
When selecting equipment for systems moving abrasive media, designers and end users have two options. The first is to make the valve and piping materials of construction much harder than the pumped media.
The second approach is to make the construction materials softer. Softer materials allow the abrasive particles to bounce off the surface without damaging it. For this reason, pinch valves have been used in mining applications that involve very coarse slurries. In any mineral based slurry, pinch valves are a viable option for protection against abrasion.
Also, a pinch valve offers the greatest protection against the clogging or jamming that occurs with other valves. Many valves—such as ball valves with harder coatings—may be able to withstand the abrasiveness of lime slurry. However, they are prone to jamming or clogging from material collection or scaling.
Pinch valves must be selected carefully. All pinch valves are not created equally. With ball valves and plug valves, stainless steel or carbon steel does not vary greatly from one reputable manufacturer to another. As long as end users select a reputable ball or plug valve provider, they will probably have a valve that is free of porosity or imperfections. Some ball or plug valves have modified designs that enhance performance in difficult services.
A pinch valve or diaphragm that has a preset weir may decrease valve performance substantially. A nonflexible weir will accumulate scale, and since it does not flex, it will result in increased wear to the rubber sleeve. Also, the nonflexible weir defeats the self-cleaning effects of pinch valves. The ideal solution is a pinch valve or diaphragm valve that pinches or closes from both the top and bottom simultaneously, meeting at the center line. This will ensure the proper cleaning of any scaling. A diaphragm valve’s diaphragm is typically one-third the thickness of a typical pinch valve sleeve. In addition, a diaphragm only has a fraction of the reinforcement cords found in pinch valve sleeves.
Pinch valves can differ greatly. Their rubber quality and properties can vary from one manufacturer to another.
A good analogy is the purchase of automobile tires. A driver has the option to purchase either a 40,000-mile rated set of tires or an 80,000-mile rated set of tires. Side by side these tires will look almost identical. However, the life of the 80,000-mile rated tire will certainly cost more and provide more than two times the useful life.
Regarding pinch valves, if end users have tried them in the past and have been unhappy with their performance, then perhaps they selected a poor-quality pinch valve. They should try again with a different manufacturer, because not all pinch valves are poor quality. A high quality pinch valve can typically handle lime slurries without any special product enhancements.
The Price of Poor Valve Choice
Many companies try to force their standard valves into applications in which they do not belong. Obviously in a large process plant, standardizing products as much as possible is desired.
This cuts costs in spare parts, the training of plant personnel and the ease of continued operations. What many of these large process plants fail to recognize is that this practice may cost more.
By using a product more suited to a slurry process, one process plant was able to double its mean time between failures. It had 22 control valves in its process. The five-year operating costs—excluding the cost of downtime of the previously used 22 control valves—was $242,000. By replacing these valves with better-suited pinch control valves, the five-year cost was reduced to only $55,000. The maintenance staff could then focus on more critical process improvements.
The financial ramifications of poor valve selection, instrumentation and piping for slurry processes can have a long-term negative impact on most operations. Even though a simple lime slurry control loop for pH control in many chemical plants is a small portion of the process, it may be a large drain on maintenance costs. Process valves and instrumentation for this part of a process should be chosen carefully.
Process plants can select from a wide array of valves to be used in lime slurry. This article did not exclude any types of valves intentionally. Instead, it focused on the types of valves that are more commonly used in lime slurry and those that also offer recommendations that may help improve valve performance regardless of the type selected. A little time invested on the purchase of the correct valve for slurry service can result in substantial savings in the future.