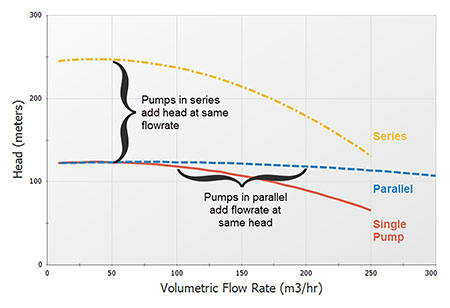
The energy to power pumps is often a significant but overlooked operating cost in a hydraulic system. While pumps themselves have become more and more efficient over the years, putting an efficient pump in an inefficiently designed system leaves many operational benefits on the table. Similarly, relying on a single pump for a system’s needs can lead to large capital costs from redundant back-ups, inefficient operation under diverse operating conditions, and challenging system requirements for successful operation. As with system design, considering pumping station configuration can reveal approaches to make a pumping system more efficient.
Why Consider a Multi-Pump Configuration?
There are many benefits to configuring multiple pumps instead of relying on a single pump for a system. By approaching pump sizing with these alternatives in mind, there are more opportunities to capitalize on cost savings and improve pump operations, as well as create additional flexibility in the operation of a system.
The primary benefit of using a multi-pump configuration is spreading the system’s workload across many smaller pumps instead of relying on a single large pump. In circumstances of large flow rate and large head requirements, a custom single pump may be more expensive than a collection of smaller pumps. These smaller pumps are more likely to be off-the-shelf components, more reliable, more cost-effective to maintain and easier to install. Similarly, a smaller motor would be needed, again improving capital costs and hopefully creating long-term energy savings over the life of the system. Often, software can simplify analysis on the recurring and capital costs of different pump alternatives, informing an engineer’s economic decisions during the design process.
During operation, multiple pumps create flexibility in a system by providing several potential operating points. A collection of pumps allows for a single pump to meet low flow demands, while several pumps together could meet higher flow demands. Designing for multiple pumps running continuously also allows for improved redundancy measures. In a single-pump system, a fully redundant pump is required to maintain flow during maintenance or emergencies. Multiple pumps ensure the majority of a flow requirement is met if one pump has issues or requires maintenance. This is also more cost effective than a fully redundant pump, especially in the case of massive high-head or high-flow rate pumps. In many cases, the analysis of design alternatives is expedited by software to compare different operating conditions and test pump operation in imperfect scenarios.
Series vs. Parallel Pumping
Pumps can be oriented in series, parallel or a combination of configurations. Pumps in series add each individual pump’s head rise as the same flow rate passes through each pump. Pumps in parallel operate at the same head rise with potentially variable contribution to flow. Each pump in parallel generally sees the same inlet and outlet conditions, thus requiring the same head rise to be effective. As will become evident through some examples, combining differently sized parallel pumps can cause operating issues due to this head rise requirement. Image 1 demonstrates how operating pumps in each configuration contribute to a composite pump curve. Pump and system curves prove useful when comparing configurations and determining potential operating conditions.
System Aspects of Pump-System Interaction
In nearly all cases, flow will increase by running an additional pump. The amount that flow rate increases is determined by the pressure demands of the system and the composite pump curve. The system’s demand, characterized by a system curve, has two main components.
The first component, static head, describes head the pump must overcome regardless of flow rate. Static head can include changes in elevation or difference in pressure from system inlet to system outlet. The static head requirement is where the system curve has zero flow.
The second component, friction head, increases head demand with increasing flow rate. Friction head also captures losses due to components, indicating the slope of the system curve can shift with changing operating conditions such as valve position.
The effectiveness of an additional pump largely depends on the system. For cases with low friction head and, thus, a flat system curve, operating pumps in parallel should increase flow rate more than operating the same pumps in series. In cases of high friction head (such as narrow, rough pipes with many components), operating pumps in series can provide more head to meet system demands at a higher flow rate.
The resulting flow rates from each configuration in each system can be found in Image 2. Notice in all cases, flow rate will increase slightly compared to the single pump curve but with a drastically different return on flow rate for running an additional pump.
Extrapolating the pump-system concept reveals the various operating conditions a system can achieve by staging several pumps. There are energy savings by selectively running pumps at various system demands.
Dissimilar Pump Configurations
There are also benefits from using dissimilar pumps in parallel or in series. While the concept of staging applies largely to uniform pumping stations where each parallel pump is identical, different pumps can similarly provide additional operating points for a variable demand system. For example, operating a large pump parallel to a small pump ensures flexibility as demand shifts. By shifting which pump operates, the small pump can meet small demand while the large pump can meet large demand. This creates energy savings while also providing operational benefits as each pump can operate closer to its best efficiency point (BEP).
While having dissimilar pumps in parallel can improve operation when each is run independently, improvements by running both at the same time largely depend on each pump’s respective pump curve and the system curve.
Imagine a case where a low-flow, low-head pump is competing with a larger high-flow, high-head pump. In parallel, these vastly different pump curves will be summed at the same head rise as before. Image 3 demonstrates the limited contribution a small pump can make when operating dissimilar pumps in parallel and system requirements exceed the small pump dead head.
In severe cases, the larger pump’s lowest head may exceed the dead head of the smaller pump, indicating that the small pump cannot contribute to increasing flow while the large pump is running. This mismatch can also lead to backflow issues through the small pump if not addressed with a check valve or similar isolation valve.
Multiple dissimilar pumps can also be used in series to solve operational problems during pipeline distribution. For example, imagine a long pipeline with severe changes in elevation. Since pressure requirements increase with pipe length, a single pump would need to add massive amounts of pressure right at the pump discharge. With this high pressure as a basis, there can similarly be high pressures when the line drops in elevation.
The fluid may experience cavitation from the drop in pressure at high elevations further down the line. Rather than relying on a single pump, booster pumps can help avoid exceeding the pipe’s pressure limitations or ensure there is sufficient pressure to avoid cavitation in the middle of the line. Similarly, booster pumps can help an undersized pump meet system requirements in other contexts.
How to Consider Pump Configurations
While it is conceptually easy to combine composite pump curves, it can often become difficult to manage configuration alternatives, pump options, system conditions, etc. As with many engineering issues, considering software is a viable method to quickly and adequately size pumps. In many cases, software can generate the composite pump curve and the system curve from user input, reassigning the operating point automatically from system changes. With pump operating points determined automatically, it is also convenient to check the BEP proximity at each operating condition. Software can provide insight into design flaws before implementation, addressing issues before they occur.