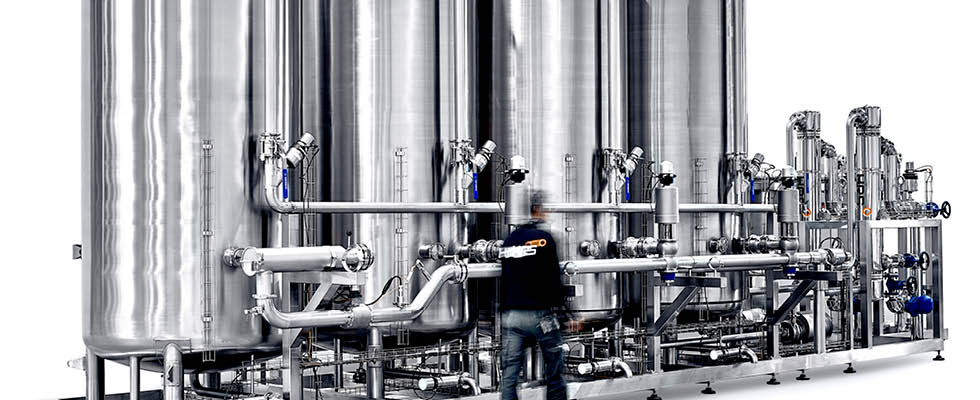
The production of safe food and drink products is important to producers, and maintaining hygienic—in some cases sterile—production environments and equipment is a key requirement for modern food processing machinery. Apart from the simplest systems, most equipment today (particularly that which contains pipework, enclosed spaces and small apertures) is cleaned on site without the need for dismantling or opening, and with minimal operator intervention—a technique which is known as cleaning-in-place (CIP).
CIP has been around since the 1950s and can be defined as a method of automated cleaning of the interior surfaces of equipment without major disassembly. One of the most widely quoted definitions is taken from the 1990 edition of the Society of Dairy Technology (SDT) manual Cleaning in Place, which defines CIP as: “The cleaning of complete items of plant or pipeline circuits without dismantling or opening of the equipment and with little or no manual involvement on the part of the operator. The process involves the jetting or spraying of surfaces or circulation of cleaning solutions through the plant under conditions of increased turbulence and flow velocity.”
Advantages of CIP
CIP offers several advantages over other cleaning systems that require manual intervention or the breakdown of component parts in order to access them. As well as obvious savings in terms of the labor required for the cleaning process (and associated nonproductive downtime), water, energy and chemical use is also reduced in CIP systems. Repeatable cycle controls reduce the amount of water required for effective cleaning, and this also reduces the amount of effluent generated and discharged to drains, reducing wastewater treatment costs.
Another benefit is equipment that is properly cleaned on a regular basis has the potential to run longer between maintenance periods, increasing equipment productivity. CIP also has implications for traceability and food safety. Manual cleaning routines also require manual record keeping, which is both onerous and time consuming. In contrast, a well-designed CIP system will include full traceability recording, potentially with the ability to download records of cleaning cycles to external quality management systems.
A final benefit comes from improved employee safety. Firstly, workers are not exposed to aggressive or potentially harmful cleaning chemicals (particularly in their undiluted forms). Also, depending on the nature of the equipment or system, operators are not required to enter confined spaces or vessels to clean them. Not only does this reduce the risk to the employee, but it also removes a management burden in terms of the need for safety procedures and safe work systems to cover such activities.
The 2011 Food Safety Modernization Act (FSMA) increased the powers of the Food and Drug Administration (FDA) and placed a particular emphasis on preventing practices which can lead to foodborne illness. CIP systems represent a major element in meeting these requirements, particularly where they are chosen to comply with Code of Federal Regulations (CFR) Title 21 and American National Standards Institute/International Society of Automation (ANSI/ISA)-88 (S88) standards.
Design Considerations for CIP
The main purpose of CIP is to remove physical dirt and residues, as well as bacteria. It is commonly used for equipment such as piping, tanks and fillers. CIP employs turbulent flow or spraying and can also be accomplished with filling, soaking and agitation.
As well as ensuring production equipment is hygienically clean and suitable for use, CIP plays a number of other important roles. CIP systems should ensure no cleaning fluids or contaminants remain in the equipment, ensuring food safety. By reducing the effort and downtime required for cleaning, they also ensure production cycles are efficient and cost-effective. Because of the automated or semi-automated nature of CIP systems, they provide improved control of the cleaning parameters to ensure consistent results, as well as automatic record keeping for traceability and due diligence purposes. Being automatic also reduces the need for human contact with potentially harmful cleaning agents or other chemicals.
However, if CIP is to be effective, not only does the CIP system itself need to be well designed, but the production equipment needs to be designed from the beginning with effective CIP in mind. Equipment and machinery must be hygienically designed and easy to manage, maintain and audit. Because of the specialized and custom nature of much food and drink processing machinery, some CIP systems are designed specifically for a particular system or piece of equipment, although with careful design it is not uncommon to install a dedicated CIP system.
The design process must not only ensure effective cleaning but should also be as efficient as possible in terms of water, chemical and energy use. Considerations for the equipment itself include areas such as surface roughness, clean welding and the prevention of inaccessible areas or corners where dirt and/or cleaning chemicals may build up. Reliability is also an important consideration, and CIP systems must be designed to function for as long as the working lifetime of the equipment involved. It is also important to consider how user-friendly the control systems for the CIP system are.
For example, are they part of the overall control interface or a separate system? Another key element of an effective system is monitoring and validation of the cleaning results for traceability and due diligence purposes, and from the beginning, the design of the equipment should allow this to be done in an effective manner.
Typical CIP Processes
Most CIP employs a similar set of operations, including:
Pre-rinsing: to remove large debris and residues
Detergent cleaning: to remove attached dirt and soiling using a caustic detergent
Rinsing: to remove detergent and dirt
Optional acid cleaning: if required, to remove scaling or alkaline residues
Rinsing: to remove the acidic cleaning agent
Disinfection: heat or chemical treatment to disinfect the equipment
Final rinse: to remove all traces of chemicals and prevent contamination
These steps may be combined or used in different ways. For example, using detergent at high temperatures may clean and disinfect equipment at the same time, and using steam may reduce the need for chemical detergents. Depending on the design of the system and the risk of contamination, cleaning solutions may be reused multiple times or discarded immediately. There may also be differences between CIP and sterilize-in-place (SIP) systems. For example, many SIP systems add a sterilization step, killing microorganisms still active in the system with hot water or steam.
While the actual cleaning regime used will depend on several factors, including the risk category of the food or drink product, the physical and chemical properties of the product and the design of the machinery in question, it is often preferable to rely on water alone (together with temperature, pressure and agitation) rather than additional cleaning chemicals which could present a contamination risk. In general, the higher temperatures and greater kinetic energy provide more efficient cleaning, but the duration of the CIP cycle will be optimized according to the properties mentioned above.
Where detergents are required, one of the most common is caustic soda (NaOH), although many other alkali- and acid-based chemicals are available depending on the nature of the product and residues that need to be cleaned. Alkali materials are generally more effective against proteins and fats, while acids perform better where salts need to be removed. For sugars, water remains one of the most effective cleaning mediums.