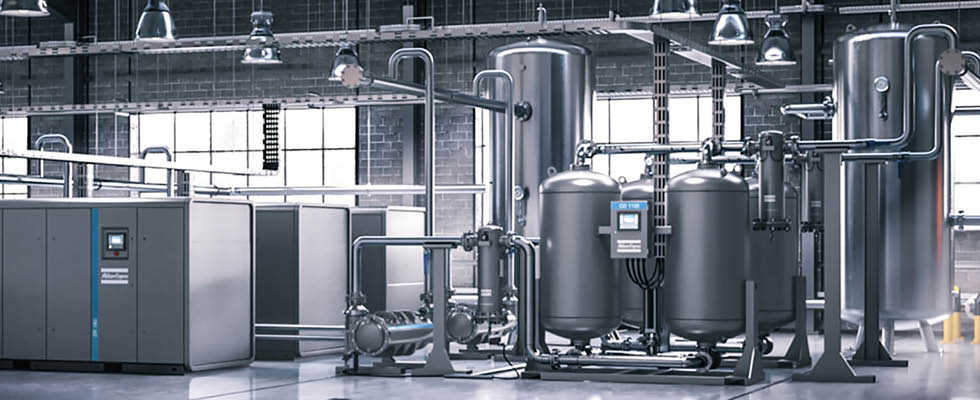
Efficiency is one of the most used terms across industrial companies throughout the United States and around the world. When it comes to air compressors, efficiency should never be limited to energy efficiency. This is prefaced by acknowledging that up to 80% of the life cycle costs of a compressor come from energy usage.
One analysis of the market by a compressor manufacturer concluded that U.S. manufacturing has a compressed air installed base of at least 15 million horsepower. Based on looking at various air audits across different user types, sizes and segments, the analysis concluded that the U.S. could save around 13 billion kilowatt hours (kWh) annually in electricity associated with compressed air, which would save U.S. manufacturers over $1 billion in energy costs annually. Importantly, this would remove approximately nine million metric tons of carbon dioxide (CO2) annually—equivalent to more than one million homes’ annual electricity usage.
Across several industries, a variable speed drive (VSD) rotary screw compressor can generate energy savings. Ideal for many applications, this technology offers a wide range of volume and pressure bandwidths, yielding efficiency and flexibility. While a great option, screw technology should not be a default choice without first auditing the facility.
Detailed supply and demand-side audits always need to be conducted on-site. The term audit is also often used for more straightforward studies that involve data-logging machines and monitoring performance over a defined period, referred to more as surveys than audits. The simple installation means the equipment needed for a survey can be sent to the end user without the need for somebody on-site to set it up. Then the hardware is returned, and the data is put into a modeling system to produce graphs and see where savings can be made. This can all be done remotely if that is the end user’s choice.
Air quality testing is something which continues to gain significance and is even mandated inside critical industries like food and beverage. This will always involve gaining an air sample on-site while making sure not to contaminate the sample before it is sent away for testing.The focus then shifts to service efficiency, which encompasses time, money and downtime. Like most machinery, the time between service intervals has increased on many compressors due to continued improvements in designed components. When choosing a compressor, it is critical to calculate return on investment (ROI) or total cost of ownership (TCO).
Considering handling some service procedures in-house? If so, consider the physical time required, whether some parts need removal, any specialized equipment or tools needed and the cost of the components. Finally, note that saving a few dollars on non-OEM or guaranteed parts is generally one of the least efficient practices, as it can limit the energy performance of the machine or lead to failure, which brings up the last point on efficiency: the cost of downtime.
Every facility manager knows the cost of downtime. Keeping up with service needs when relying on a single machine is challenging. These days, it is possible to build a system that is not all or nothing—for example, by easily adding a second machine or running two smaller ones in parallel using simple (but advanced) sequencing tools to ensure harmony and efficiency. To aid with this, more end users are purchasing air like they do gas, electricity or water. So, in essence, they are buying air and not the actual compressors. For the right user, this has several advantages, including not needing a capital expenditure at the start of the project and having no maintenance responsibility for the equipment, as that is taken care of by the OEM.
Remote monitoring and 24/7 connectivity are offered by many OEMs with just about every new compressor (and often can be retrofitted to older ones). This gives peace of mind to ensure a user can always be in control, no matter where they are working from. The supplier can see the same messages that users are seeing in real time and can guide users in proactive steps. Lastly, users can also think of remote monitoring as an ongoing audit that happens 24/7, offering constant visibility to flag issues before they become serious problems.
To put it simply: efficiency is an all-encompassing topic. Energy efficiency is nothing without the efficiency of uptime and reliability. The challenge of looking at an energy bill is that it might have always been the same. It is accepted as the cost, and the cost has been built into your budget for years.
Simple air studies have never been easier to benchmark and understand savings, but here are five things that might indicate it is time to look at the system.
- You see the manufacturer’s compressor service team more often than your dentist.
- You feel like you need to wipe your feet when leaving the compressor room.
- You need to shout if chatting to a colleague when standing near your compressor.
- You can’t monitor your compressor system unless you are standing next to it (no remote access).
- You are not able to view simple energy output graphs for the performance of your compressor.