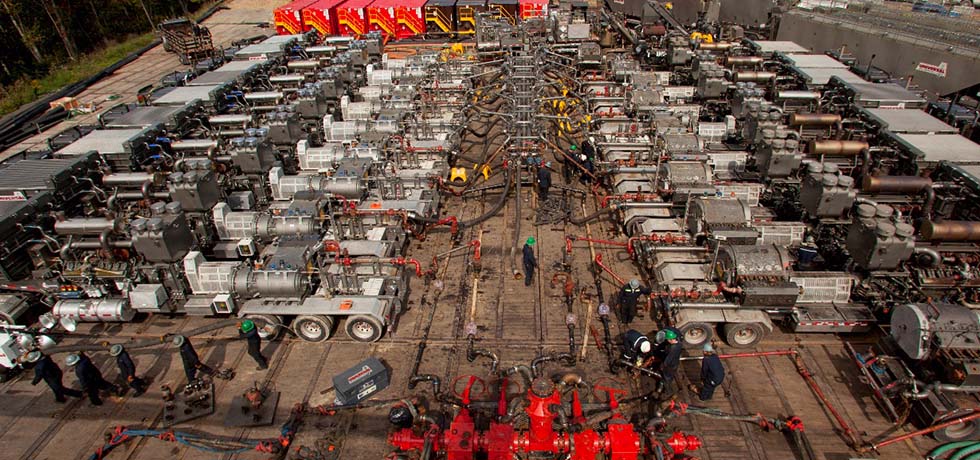
Before 2005, natural gas production was declining in the United States. With incentives from the U.S. government, such as tax credits, industry had experimented in the 1970s with tight gas or sandstone layers that had low flowability, or permeability, to gas. This arrested the gas shortage for a decade or two. Same thing for coalbed methane or natural gas that was trapped in coal seams. This took off in the 1980s and eased the shortage for a couple of decades.
But the U.S. appetite for natural gas kept growing—industrial manufacturing, gas-fired power plants, gas heating in homes and offices and plastics that are made from natural gas liquids such as ethane and propane for use in offices, homes, clothing and drugs. As a last-ditch effort, horizontal wells were drilled into shale layers with essentially zero permeability.
Like most vertical wells, the new horizontal gas wells needed to be fracked, but how many frac treatments were needed for a long horizontal well? Operators needed a robust and reliable source of pumping power to inject enormous volumes of frac fluid under challenging pressure conditions.
(Images courtesy of the author)
The Key to Shale Fracking
Conventional fracking methods and fluids did not work well enough.
Then, an engineer in the Barnett shale out of Fort Worth decided to pump straight water instead of conventional gelled water as the frac fluid. Gas flow rates improved and water was cheaper, so shale wells finally made a profit.
The key was to crack up the shale rock all around a horizontal well. In fracking, water is forced down a vertical well and then along a horizontal well. Small holes called perforations direct the water into the shale layer, and if the force is great enough, it splits the rock like an ax splits a log of wood. This is where the frac pumps come in, and a massive pumping system is required.
The result is a network or mesh of tiny cracks in the shale layer. If several separate fracking operations are conducted along a horizontal well, the well can be surrounded by a mesh of tiny cracks. In this way, the operator has enhanced the permeability of the shale layer and gas molecules can flow more easily to the horizontal well after the fracking campaign is over. By 2003, shale wells became profitable enough to open the door to a shale revolution that includes shale oil as well as shale gas; the new technology worked well for both.
Pushing the Limits
Adventurous oil and gas companies pushed the limits. They drilled horizontal wells up to 2 miles long and conducted up to 40 separate fracking operations along each horizontal well. It is a large operation requiring many huge pumping units to be synchronized.
First, to force the water to crack the shale rock, the pumps have to overcome the natural stress in the rock at depths up to 12,000 feet underground. This means roughly 12,000 pounds per square inch (psi). The pressure would be like crushing your hand under a steamroller building a highway.
Second, in a typical shale well, the volume of water used would fill a football stadium to 40 feet over the grassed area—and that is just for one well.
Third, the frac pumps must deliver tiny sand grains, as well as water, in the later stages of a frac treatment. These sand grains lodge in the cracks that have been created around the horizontal well and prevent the cracks from closing after the fracking operations have been completed. In a typical shale well, about 100 railcar containers of sand are pumped down for just one well.
The Shale Revolution
The success of shale fracking enabled the U.S. to become self-sufficient in oil and gas—the first time since 1947 (Image 1). The shale revolution led to cheap gasoline, inexpensive power for industry, cheap plastics and other manufacturing benefits for the U.S. Around the world, cheap and reliable oil and gas energy have lifted world populations to a higher standard of living.
In February 2022, the U.S. became No. 1 in liquefied natural gas (LNG) exporters, beating out Australia and Qatar. The hope is that this will help countries like China and India switch from coal-burning power plants to natural gas and reduce their greenhouse gas (GHG) emissions (gas burns much cleaner than coal).
The Pumping System
Traditionally, high-pressure, high-volume water fracs require diesel-fueled combustion engines. A frac pump has to inject frac fluid, mostly water and sand, under huge pressure to crack up the rock deep underground to allow oil or gas easier inflow to the well.
A normal frac fleet is limited to 15,000 psi but there are several fleets within the U.S. capable of 20,000 psi. The typical injection pressure for shale wells is about 8,000 psi.
Typically, each separate fracking operation pumps water and sand at a rate of 30 to 75 barrels per minute (bpm) but this can be as high as 150 bpm. After two to three hours of pumping, the injection moves one stage back along the horizontal well and the next frac operation begins.
Frac pumps are reciprocating positive displacement (PD) pumps that contain a fluid end and a power end. A mixture of sand and water has to be forced down a well and through small perforations so the pumps have to endure abrasive fluids. The pumps also must deal with pressure extremes, especially if the fracking pressure gets so high it threatens to split the well casing.
A diesel fleet of pumps typically needs 20 separate pump trailers at the well site. If there are multiple wellheads at a fracking site, frac pumps can run without interruption. Each fracking fleet requires a crew of about 30 people, about 15 for each 12-hour shift. Total power can reach 20 million horsepower (hp).
There is a trend in the industry to go to a technique called simul frac, which means the frac fleet is fracking two wells at the same time. This cuts the completion time in half and improves operational efficiency.
In the Marcellus shale (Image 2), eight to 14 gas wells can be drilled on each pad location, with 40 separate frac stages deployed in each well. By doing six fracking operations per day, the time elapsed is 53 to 93 days. So approximately two to three months of rig activity at each pad site is not uncommon.
Quintuplex pumps have achieved higher hp. One company reports an 11-inch stroke rated at 5,000 hp. This can mean a lower operating speed to reduce fatigue cycles, extended pump lifetime and fewer pump trailers.
Fracking pumps must be rugged and reliable. Downtime is expensive, so operational efficiency is highly desirable.
E-Fracking
The world is entering a gradual transition from fossil fuels to renewable energies, driven by climate changes attributed to greenhouse gas emissions. Fossil fuels provide 83% of the world’s energy and 73% of the world’s GHG emissions.
In the oilfield, one way to reduce GHG is by companies greening their own operations by using wind or solar electricity to pump fracking operations. Alternatively, diesel-fueled combustion engines can be replaced by e-frac systems where electric pumps are driven by gas turbine generators that use LNG, compressed natural gas (CNG) or flared gas.
Gas turbines are much lighter than diesel engines, which allows for two turbines on one chassis. This means half of the trucks normally required on location are no longer needed. A typical diesel unit will supply 2,200 hydraulic horsepower (hhp) whereas a typical gas turbine will supply 4,400 hhp with the same GHG footprint.
One fracking consultant said the e-fleets he had seen were using field gas to generate electricity that power the fleet. This reduces the GHG footprint by two-thirds and allows the operating company to complete many more wells under the same GHG emission license.
E-fracs are only 10% of the market now but this stands to increase because of worldwide demand to lower GHG. GHG is typically reduced by 50% by using e-fracs. Cost savings exist in fuel and pump engine repairs but upfront costs are higher than a new diesel system. One oilfield services operator reported a longer life for components of his e-frac system versus a diesel system. The electric motor, transformer and variable frequency drives (VFDs) replace the engine and transmission in the diesel system, meaning fewer moving parts and longer maintenance intervals.
While a diesel fleet typically needs 20 pump trailers at the well site, an e-frac system requires only eight. Another e-frac advantage is noise reduction—95% less frac pumping noise.
The author would like to give grateful thanks to Carl Montgomery for input on frac pumping systems.