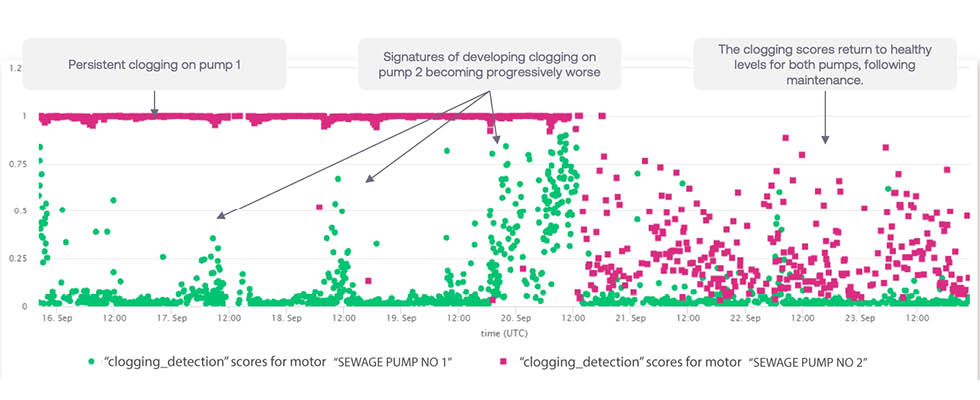
Water and wastewater companies across the world are facing considerable challenges. Aging assets, the ongoing energy crisis, increasing regulatory and sustainability requirements, as well as the impact of climate change, are all factors that are putting a lot of stress on existing infrastructure and the maintenance teams that are tasked to take care of it.
In response, many organizations are investing in improving and optimizing operations. New technologies and approaches are converging to transform the performance, efficiency and reliability of pumps and other industrial assets.
In particular, the use of condition-based monitoring strategies is increasing, as they allow users to estimate the actual condition of machines in order to plan and schedule timely maintenance interventions. Yet, certain asset types like submersible pumps present a unique condition monitoring challenge.
Understanding the Challenges of Maintaining Submerged Equipment
The first—and perhaps most obvious—is access. Pumps operating in water boreholes, for example, can be 150 to 200 meters below ground. In parallel, a company’s fleet of submerged pumps may also be distributed across a wide geographical region, turning travel time into a significant cost factor. The access challenge is compounded by the fact that lifting submerged equipment is also cost- and resource-intensive, requiring specialized equipment, skilled personnel and extensive downtime.
The advent of wireless sensing and the internet of things promised to overcome these challenges, enabling organizations to continuously monitor the condition of assets in real time using vibration and thermal analysis.
Any sensors deployed on submersible pumps, however, must be able to function in waterlogged conditions for extended periods. Where such sensors even exist, they are prohibitively expensive and wholly unsuited to cost-effective, scalable deployments.
These considerations have historically inhibited a proactive, condition-based monitoring approach. This has pushed organizations toward less efficient time-based maintenance strategies at best; however, in most cases, run-to-failure approaches still linger. A recent survey of industrial organizations found that 66% are still reliant on these reactive maintenance strategies.
This is leading to significant operational issues. The water industry, for example, is facing increased regulatory and public pressure to prevent sewage spills into the environment, many of which are caused by damaged or clogged submersible pumps at wastewater pumping stations.
Similarly, climate change is increasing the prevalence of extreme weather events and extended drought periods. During prolonged dry spells, decreased availability and increased demand mean that shallower boreholes inevitably dry up. Subsequent failures of operating borehole pumps can lead to major water supply interruptions.
This means that remotely capturing accurate, usable asset health data from a submersible pump, without deploying sensors on the asset itself, can unlock significant benefits and should be seen as mission-critical.
The good news is that a technology called electrical signature analysis (ESA) makes reliable, remote monitoring of submerged pumps possible.
How ESA Is Transforming Submersible Pump Maintenance
ESA measures the current and voltage being supplied to the motor driving the pump. Because it captures the electrical signals, ESA sensors are current and voltage probes that are installed in the motor control cabinet. This bypasses the need to install sensors on, or even near, submerged pumps.
This is a game-changer for industrial organizations, enabling access to valuable asset health data that was previously challenging, expensive and sometimes even impossible to obtain. When powered by artificial intelligence (AI) and machine learning (ML) algorithms, gigabytes of raw asset health data can be translated into comprehensive performance insights to inform and support a condition-based monitoring approach, allowing users to schedule maintenance at a convenient time and avoid unplanned downtime.
An associated benefit, which is a direct consequence of capturing electrical data, is that ESA systems can report on pump performance. This information enables organizations to make data-driven decisions to raise pumps’ efficiency and extend their lifetime.
Leveraging ESA Systems Across the Water Industry
As a reliable and proven condition monitoring technique for submerged assets, ESA is increasingly being deployed at scale by water and wastewater companies as part of a proactive maintenance strategy. This is helping to address one of the key challenges: improving reliability of critical infrastructure.
Take this real-world example from a United Kingdom (U.K.) water provider. One of its two co-located pumps at a sewage pumping station demonstrated signs of clogging. With one other working pump at the station, it was determined to continue to monitor the situation closely for 48 hours to understand if a site visit was necessary. When this timeframe passed with no improvement, a medium-priority maintenance visit was planned.
A week later, however, data indicated signs of developing clogging on the other pump. This created an emergency response situation due to an increased risk of a pollution event. A maintenance team was immediately dispatched and lifted both pumps out of the pumping station, confirming that both were partially blocked. After the blockages were cleared and the pumps were back in operation, electrical data returned to healthy levels.
Similarly, another U.K. water provider leveraging ESA technology to monitor borehole pumps was immediately alerted by the system to a sudden mechanical imbalance at one specific pump. This triggered a maintenance visit which addressed the issue, preventing serious pump damage and significant water supply disruptions.
Looking Forward to a New Era of Maintenance Through Drive Integration
With 60% of industrial organizations planning to increase their investment in reliability and maintenance in the next three years, the vast potential of condition-based monitoring is starting to be realized. One of the various returns organizations expect to see from this increased investment into new equipment and related digital services is improved energy efficiency. This view is particularly prevalent within the water industry, with 77% seeing this as the main benefit.
One solution utility operators are increasingly deploying to improve the energy efficiency of pumps are variable frequency drives (VFDs). VFDs are a type of motor controller that drive an electric motor by varying the supply frequency. By matching fluctuating load and demand requirements, organizations can operate pumps more efficiently, saving energy and extending their lifetime.
Given the proven benefits of ESA technology, increasing adoption of VFDs presents a powerful opportunity to provide enhanced condition monitoring data to offer a complete insight into the health of the asset’s full drive train. VFDs already generate electrical data relating to the control and operation of the motor and the load it is driving, such as current, voltage and supply frequency. Since ESA measures high-quality current and voltage data generated at the motor’s supply,
there is a clear path to integrating the technology into the VFD to enable remote condition monitoring into the drive, motor and the pump.
This integration makes it possible to control and operate the equipment in the most efficient manner and enables a move toward a proactive, condition-based maintenance approach. Other benefits include a simplified onboarding process, reduced upfront costs and increased scalability, as there is no need for additional sensor hardware.
Looking ahead, organizations are expected to continue to move toward more proactive maintenance. A key emerging trend on the horizon is increased interest in outcome-based maintenance agreements, where organizations pay service partners based on achieved outcomes such as increased uptime and energy savings.
For this approach to be feasible at scale for manufacturers and service providers, predictive maintenance technologies will become an important enabler.