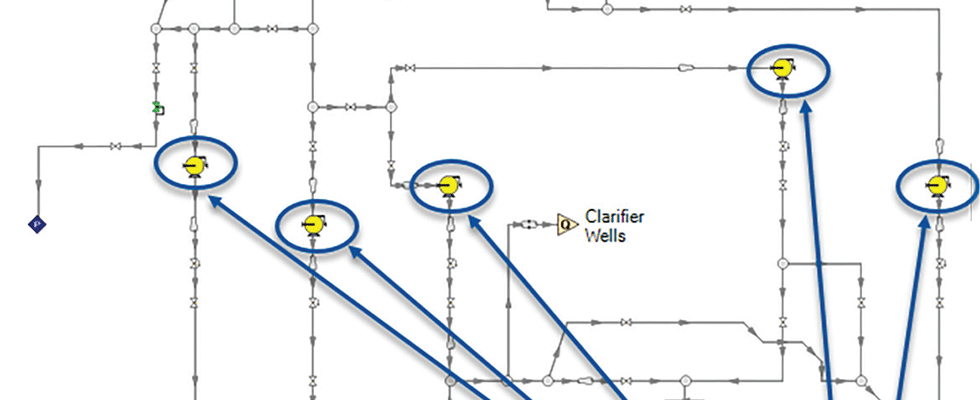
Choosing the best pump for a system can be a challenge. At minimum, the pump needs to deliver the required flow rate—but be careful not to make hasty decisions. System designers should understand a better pump will not only operate at the required flow rate, but it will also be reasonably priced, cause minimal downtime, be easy to maintain and have
a long operational lifetime. All these points are important to ensure safe and profitable operation.
Pump Best Efficiency Point
High efficiency impacts the energy costs for operating a pump as well as the wear on the pump. Operating at flow rates above the best efficiency point (BEP) can result in cavitation, as well as excessive vibration and heat at the pump. When operating below BEP, there are risks of pump seizure, low flow cavitation, fluid recirculation and high temperatures. All these situations can damage the pump, which in turn will decrease the reliability and lifetime of
the pump.
Since it is not practical to operate directly at BEP, a preferred operating region is provided by American Petroleum Institute (API) 610, API’s published standard for the petroleum, petrochemical and natural gas industries. Operating within the preferred operating region will minimize the negative effects caused by operating away from BEP. Section 6.1.12 of the standard defines the preferred operating region for pumps to be within 70% to 120% of the BEP flow rate.
There are a few exceptions to this, as are mentioned in the standard. For low specific speed pumps, it is noted the pump may not be able to operate above 105% to 110% of BEP. This will be clearly specified on the manufacturer’s provided pump curve. The standard also allows for pumps that operate outside of the preferred operating range if they have been proven to operate reliably in similar systems.
Determining an Accurate Operating Point
Choosing an effective pump based on BEP requires the engineer to determine the required head, flow and power based on the system. This is simple for a relatively new system with information available on the pipes and components. The process becomes more complex when there is not much information available, the system is old and when there are branching points in the pipeline.
To get the best estimated operating point, several factors should be taken into account:
Consider both maximum and minimum cases
Designing a pump for the maximum flow case is important, but this does not mean other flow cases should be neglected during the sizing process. If variable demand is anticipated due to factors such as the market demand, then considering the full range is important to ensure the pump operates within the preferred operating range for all conditions.
For systems with a large range of flows, a variable speed drive may be useful to keep the pump operating within the preferred operating region at reduced flow rates. Though this is more expensive than simply using a valve to throttle the pump, the maintenance costs over time will be significantly decreased.
Use design factors wisely
There are uncertainties in all engineering calculations when determining the system loss. Generally, the way to account for this is to design conservatively and overestimate head loss in the system. While it is good engineering practice to make conservative estimates, be careful not to overestimate. Exceeding the preferred operating region can be as damaging as operating below the required flow.
Use pipe system modeling software to simplify calculations
A good hydraulic simulation software can provide a more efficient process for evaluating the proposed pump and system. This reduces the possibility for error when compared to spreadsheet calculations. Simulation software can also be a good tool for evaluating different operating cases for a single system. Automated sizing tools may be considered to further speed up this process.
Case Study
A case study that involved a raw brine injection system for a North American chemical plant can provide an example of the problems a system can face when pumps are sized without keeping pump efficiency in mind.
In this case, the pumping system was being used to deliver product from underground caverns and clarifier wells. Over the course of five years of operation, 41 repairs were required on the system costing over $1.23 million. A model of the pump system can be seen in Image 1. A consulting group was requested to perform a reliability study on the system and found the current pump configuration was causing the pumps in the system to compete hydraulically and to operate in the range of 30% to 50% of BEP.
Modeling different combinations of pumps allowed the consulting company to recommend an alternative method to operate the existing pumps in order to achieve the desired flow rate. The proposed combination allowed the operating pumps to achieve a flow rate at 75% of the BEP flow rate for each of the pumps.
Maintaining a high standard for pump efficiency has many clear benefits. To reach these goals, a thorough understanding of the operating system is important. Using poor estimates for the system resistance can lead to the pump operating far from the preferred operating region. Investing the time into properly sizing pumps for oil and gas systems must be a priority to make these systems safer and maintain low costs over the system’s lifetime.