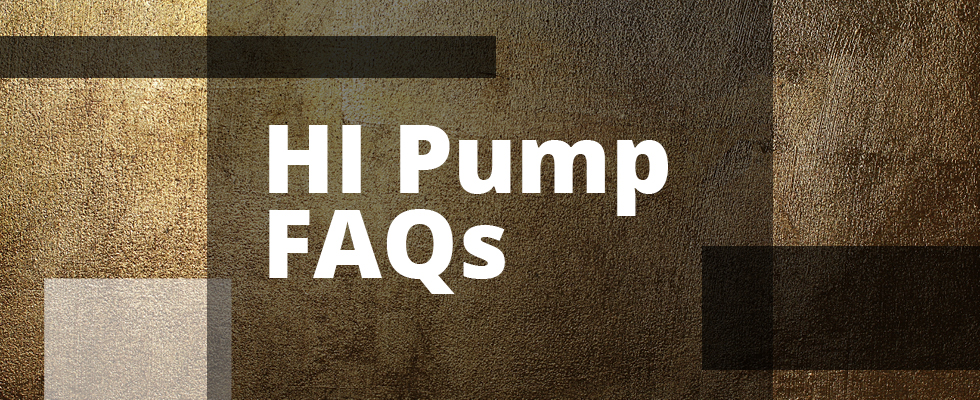
How is bearing wear monitored in sealless pumps?
Product lubricated sleeve/journal radial and thrust bearings are typically used in sealless magnetic driven and canned motor pumps.
These bearings are located within a containment shell with no shaft exposed to atmosphere; therefore, they are typically lubricated and cooled by the process fluid. Since the shaft is not exposed to atmosphere, traditional proximity probe monitoring of the shaft movement is not easily accomplished.
Detection of sleeve bearing wear in sealless pumps can be conducted by visual inspection and dimensional verification during pump disassembly periods or by special instrumentation while the pump is in operation. Instrumentation used to detect bearing wear falls into two categories: progressive wear monitoring and detection of component contact.
r1 = 26.98 mm (1.062 in)
r2 = 31.75 mm (1.25 in)
h = 0.254 μm (total surface roughness) (10 μin)
ΔP = 1.8 MPa (265 psi)
η = 1.0 x 10–3 Pa·s (1.45 x 10–7 lbf-sec/in2)
Proximity sensing devices can be used to monitor the position of the rotor within the containment device. Positional changes of the rotor are then used to determine the direction and amount of bearing wear. This method permits wear to be detected prior to contact between the rotor and the containment device or other part of the assembly (bearing holder) designed to prevent or limit rotor contact with the containment device.
The proximity sensing technologies, when used, are incorporated by the pump manufacturer, and may detect both radial and axial positional changes of the rotor. Progressive wear monitoring is not usually applied to bearings constructed from “nonwearing” materials, such as hard ceramic bearings.
Excessive bearing wear or failure of ceramic bearings will allow positional changes of the rotor to cause contact (impacts or rubbing) between the rotor and the containment device or other part of the assembly designed to prevent or limit rotor contact with the containment device.
Contact may be detected using a suitable acoustic detection device, power monitor, vibration sensor conditioned to detect impacts and rubbing, containment shell temperature probe, continuity probe or contact switch.
For more information about seal leakage and monitoring bearing wear, refer to American National Standards Institute (ANSI)/HI 9.6.5 Rotodynamic Pumps–Guideline for Condition Monitoring, and HI’s “Mechanical Seals for Pumps: A Cost-Saving Guide to Proper Selection, Installation & Operation” at www.pumps.org.