One of my previous Pumps & Systems columns expounded on an urban myth that all centrifugal pumps arrive on the jobsite ready to operate—“plug and play.” In almost every case, this myth is “busted.” Most every pump requires at least five areas of attention prior to startup, including setting the impeller clearance, which is the focus of this month’s column.
This example uses the most common type of pump—a B73.1 ANSI pump. Most manufacturers include an instruction manual and warning tag that advise the following information about the startup process:
Alignment: The alignment (driver to pump) as received is probably not correct, and it is surely not the final alignment that would satisfy acceptance criteria. Even if the factory completed an accurate alignment, it will change during the transit and installation phases. When the base is installed on the foundation and the piping is bolted on, the alignment will change.
Bearing housing: There is a 98 percent chance that no oil is in the bearing housing.
Mechanical seal: The mechanical seal is not set to the proper dimension. It may be in a safe (sleeping/transit) position with shipping clips installed. The mechanical seal may not even be installed. These are additional reasons why the coupling is not installed (fully) at the factory.
Phase rotation: Assume the driver is a 3-phase motor and the factory has no data in reference to your electrical system phase rotation. There is a 50-50 chance the factory will have the phase rotation correct. If it is wrong, you risk destroying your new pump.
This is another reason why the coupling is not installed.
Impeller clearance: Last but not least—the focus of this month’s column—is setting the impeller clearance. I continually witness this step ignored or completed improperly more than any of these mentioned issues.
Even if the purchase order specified for the factory to set the impeller clearance at a certain dimension, why would you not check the clearance in the field to verify the setting is correct? Unless there is an unbroken chain of custody with the pump, you cannot be positive and, besides, it is easy to check.
Why do you care if the impeller is set incorrectly? In addition to reduced efficiency, you are effectively reducing the impeller’s size. Just 0.015 to 0.020 inches off the correct clearance can reduce the performance of a 10-inch impeller to perform like 9.5 inches.
There are primarily two main styles of ANSI pump impellers. This article will not address the subsets of low flow/high head (constant velocity) and recessed impeller (vortex) designs.
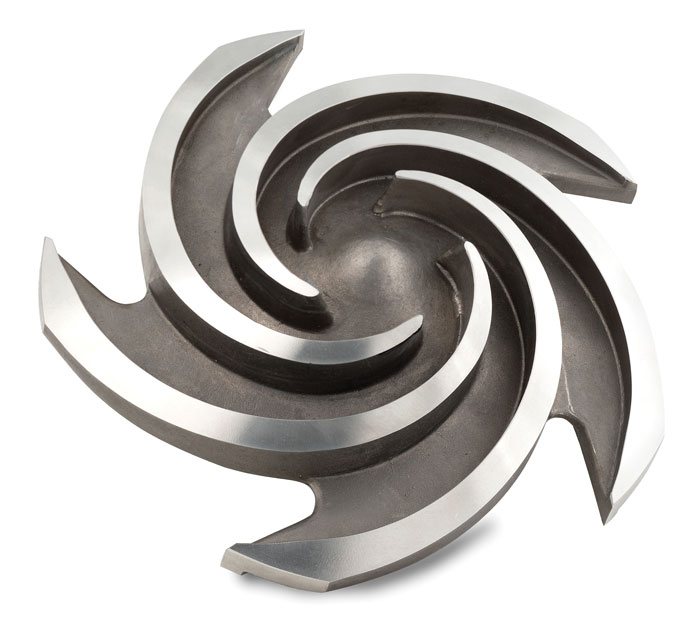
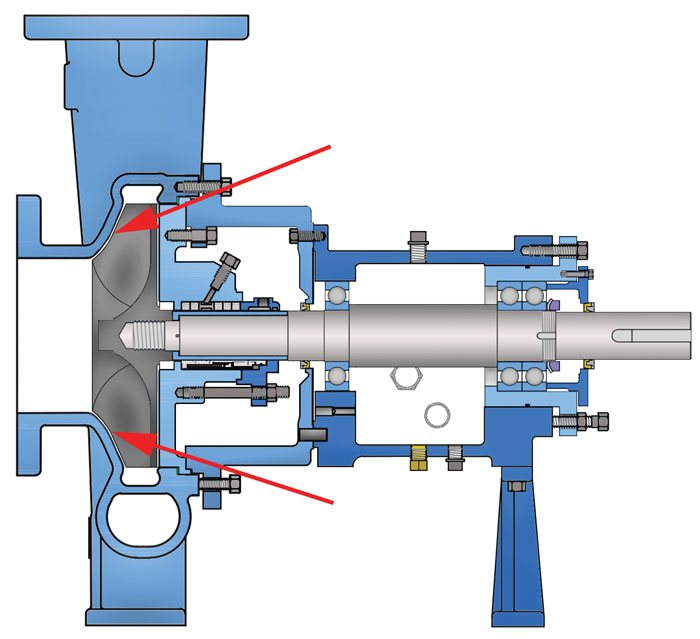
Impeller Designs
There are two main styles of pump/impeller arrangements: open impeller and reverse-vane impeller.
With an open (semi-open) impeller (see Image 1), the clearance is indicated (set) off of the pump casing to the front side of the impeller (vane tips). With a reverse-vane impeller (see Image 2), the clearance is set off of the stuffing box to the back side of the impeller.
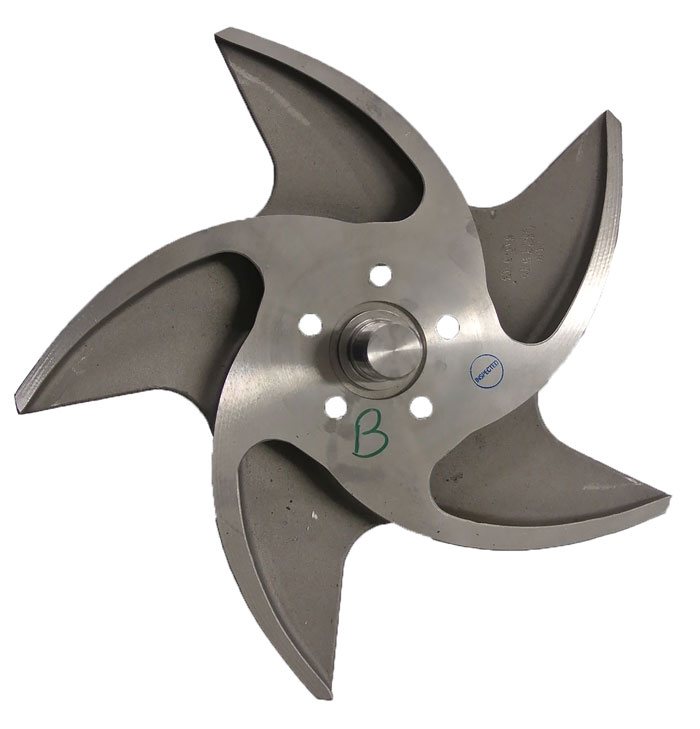
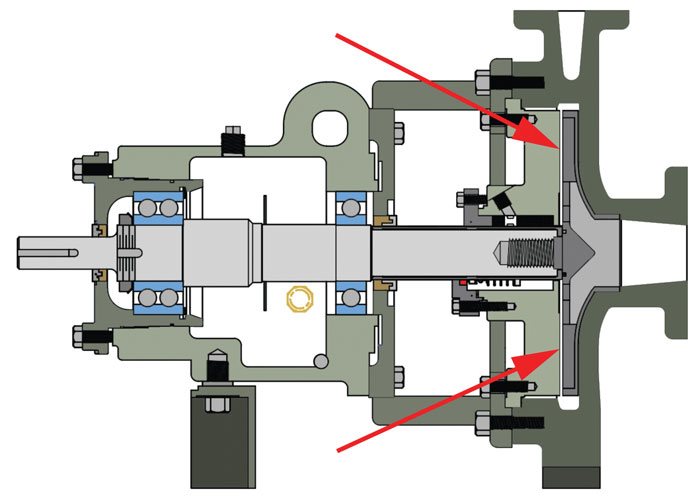
Both are good designs, but determining which one is better depends on the fluid properties you are pumping and perhaps the hydraulic conditions dictated by the system design. If the question of which design to use was up for debate, I would gladly accept a position on either side.
The concern is that many mechanics do not set the impeller to the proper clearance no matter which style of pump and impeller is used. On either style, the entire rotating assembly (shaft, impeller and bearings) can be moved axially utilizing design features at the coupling end of the pump bearing housing. In both cases, with the pump assembled you can move the impeller (the entire rotating assembly) toward the suction end of the pump until you touch the casing and in the other direction until the impeller touches the stuffing box (sometimes called the sealing chamber or back plate).
The difference is that with open-style impellers the correct running clearance is set off of the casing (see Figure 1), and with reverse-vane impellers the clearance is set off of the stuffing box or back plate (see Figure 2).
The actual impeller clearance dimension will vary by manufacturer, but more so by pump frame size and the temperature of the fluid being pumped. Refer to the manufacturer’s instruction book for the correct clearance based on frame size and temperature.
If using dimensions that are dated—for example, a shop “cheat sheet” posted near the workbench—you will want to update your data. Most manufacturers have closed (reduced) the clearances in recent years as a technique to increase pump efficiency.
The detailed procedure for how to properly set the clearance will be covered in the instruction book. There are usually at least two acceptable methods to accomplish the task. I prefer the dial indicator method because of the accuracy, reliability and validity. As an experienced engineer, I will acquiesce that feeler gauges can work just as well in the hands of a good millwright.
The common mistakes I see when the mechanic sets the clearance incorrectly include: not choosing the correct clearance for the pump size and temperature; setting an open-style impeller to the stuffing box; setting a reverse-vane impeller to the casing (volute); and setting the impeller in the middle of the travel.
Correctly Setting Your Impeller
If rebuilding the pump, always check the following factors prior to setting the impeller:- Using a dial indicator: Check for runout on the back edge of the impeller shroud. Consult with the manufacturer for acceptable tolerances. On an open-style impeller, one vane tip that is sticking out will yield a false setting clearance and can easily affect the pump performance.
- Rotor travel: Whether a rebuild or a new pump, measure the total travel of the rotor and record that dimension. At a later date (months or years), again measure the total travel without taking the pump apart. The new (larger) dimension compared to the original will reveal how much the impeller vanes and casing (or stuffing box) have worn. It will not show exactly how much on each component, but it will give the amount of total wear. Most manufacturers do not record this dimension when the pump is manufactured. Also, it will be slightly different for every pump due to acceptable and non-critical dimensional tolerances in the castings. Stack and dimensional tolerances will yield the range. Most manufacturers will not give out the drawings/dimensions, but with some prodding they will advise the expected travel range.
- Shipping clips: The mechanical seal should have the shipping clips in place during this procedure. Otherwise, the seal settings will be incorrect and/or the seal faces can be damaged.
- Rotor turning: The rotor should turn freely by hand with no rubs or binding.
- Casing gasket: Use the correct thickness casing gasket or the impeller may be too far or too close to the casing or stuffing box.
- Skim cut: More than once I have witnessed a repair shop take a “cleanup” or “skim cut” on the casing or the stuffing box without proper compensation on the corresponding component.
- Casing clearance: When reassembling the pump, make sure the rotor travel is set back so that when the casing is installed and bolted up, it does not put the rotor in a bind that will damage the impeller.
- Wider clearances: It is an acceptable practice to open the clearances more than required when pumping fluids with air entrainment. The pump will be less efficient, but will be more reliable.
- Clearance and efficiency: As a general rule of thumb, the pump’s efficiency will drop by 1 point for every one-thousandths of an inch the clearance is opened beyond the initial clearance for the first five- to 10-thousandths. After that, the efficiency will drop exponentially. (For more detail, see the Common Pumping Mistakes column in the January 2016 Pumps & Systems.)
- Replace O-ring: As a final tip, always replace the impeller O-ring no matter how new or old. These are typically made from Teflon™ material, which has low resiliency and will take a compression set rather quickly. When the reused O-ring seal leaks, the resulting effects will make it difficult to remove the impeller at the next maintenance interval.