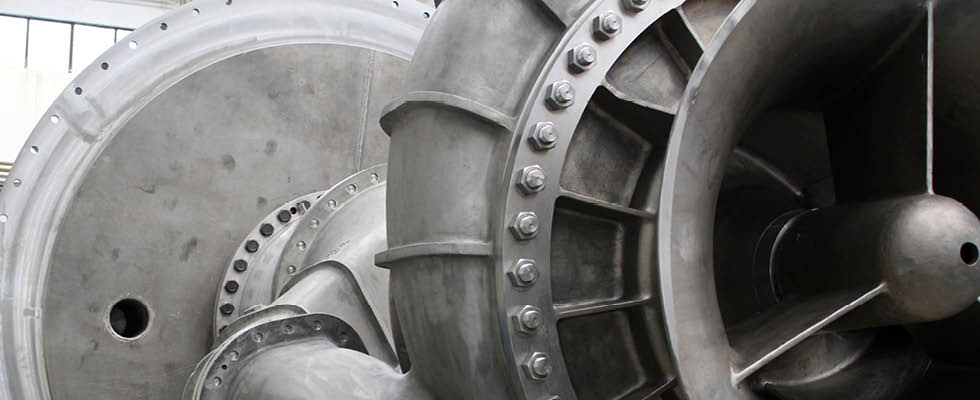
Energy efficiency has become increasingly vital for plant operators. Pump manufacturers play a pivotal role in providing support, as efficiency improvements affect pumping systems and influence overall plant energy consumption.
A global pump OEM offers users high-efficiency pumps and comprehensive customized upgrade and rerate solutions for existing pumps, including those from other OEMs. These solutions aim to provide benefits such as ease of implementation, energy savings at the pump and plant level and reduced maintenance costs.
The OEM’s service portfolio focuses on the following opportunities:
- rerating pump hydraulic components
- redesigning pump mechanical components
- package engineering, such as the installation of pump speed control devices (variable frequency drive [VFD], fluid coupling, etc.)
- pump modification or replacement.
The OEM utilizes a systematic approach to develop customized energy-saving pumping solutions. The process includes a preliminary machine and plant configuration audit, an on-site survey, a feasibility study, the creation and implementation of the new engineered configuration and its subsequent validation and certification, including on-site testing and issue of a CPSA ISO14414 certified report.
High-Altitude Hydroelectric Power Plant Pumping Station Upgrade
The OEM participated in the upgrade of the pumping station of a high-altitude dam located at 2,000 meters. The dam is part of a large hydroelectric complex, consisting of 12 power plants. The services provided consisted of the complete modification of the dam’s pumping systems, as well as the modification of the pumping station itself, including its control systems upgrading. The new plant configuration was designed to reduce the pumped water cost and simplify plant operations, with efficiency gains allowing the user to absorb its investment costs in just a few years of operation.
The installation on-site presented definite challenges. The plant, set into a steep hillside at a 2,000-meter altitude, could only be reached by helicopter. This meant personnel, which included a team of eight specialists in servicing rotary units and systems, and materials with weights sometimes exceeding a ton, had to be airlifted. Harsh winter weather conditions were also a factor, as installation was required to be performed from January through March. Lastly, the pumping station’s location itself, a cave only reachable via a 60-meter-long sloping shaft fitted with rails, presented yet another difficulty.
The pumping station brings water from two nearby rivers into the reservoir at the base of the dam, which then is dropped down 1,000 meters to power the turbines of the nearby power station and an additional plant located at the bottom of the valley. Its efficiency plays a crucial role in the power generation process.
The OEM replaced the four existing horizontal axially split pumps performing water transfer with two high-efficiency enhanced pumping units of the same type, each comprising of a pump, motor, inverter (VFD) and transformer train. In the original configuration, the pumps worked in couples, separately for low- and medium-head pressures and in series for high-head pressures. With the new configuration, the VFD allows the two pumps to cover all the pressure services.
The pumping systems pipework, wiring, bases and supporting structures were also adapted to the user’s specifications. Additionally, the inclined shaft gear (winch and wagon) and the external handling systems were replaced to support the new weight of the equipment (three tons). Finally, the OEM supply included the upgrade of the pumping station’s control systems.
Energy Saving Project for Primary Power-Consuming Pumps at Desalination Plant
The OEM participated in an energy-saving project at a desalination plant where the end user opted to replace core components of the plant’s primary power-consuming machines—the brine recirculation and seawater supply pumps.
At the time of the project, the pumps in question had been operating for more than 30 years and remained in good condition thanks to the operational and maintenance standards in place. However, considering the progress made in pump design and operating efficiency since the plant’s commissioning, the end user decided to launch an energy-saving project. The outright replacement of entire pumps was not taken into consideration, as it was not financially justifiable. For this reason, the end user decided to focus only on changing the core components of the pumps. As the OEM that originally supplied both types of pumps had shifted its business, the end user searched for another pump manufacturer able to give a new life to its existing pumps.
The OEM conducted an extensive engineering study and proposed two high-tech solutions for the rebowling of the brine recirculation and seawater pumps. The solutions proposed optimized the hydraulics of the pumps while maintaining the existing interfaces and materials. They predicted energy savings substantially higher than the figures requested by the end user.
The project was executed according to the following phases:
- site assessment and testing of the pumps to verify the actual pumps’ performances
- further performance testing on one of the pumps at the OEM’s in-house test center
- retrofitting of the pumps (new hydraulic components, impellers and casings) and retesting their performances up to contractual specifications at the OEM workshop and test center
- on-site installation and final testing
The energy consumption of the brine recirculation pumps was reduced by 123 kilowatts (kW) per pump, equivalent to a 9.8% energy efficiency improvement as a result. This led to a 1.5 megawatt (mW) annual energy saving at the plant level, corresponding to 7,630 tons of carbon dioxide emissions reduction.