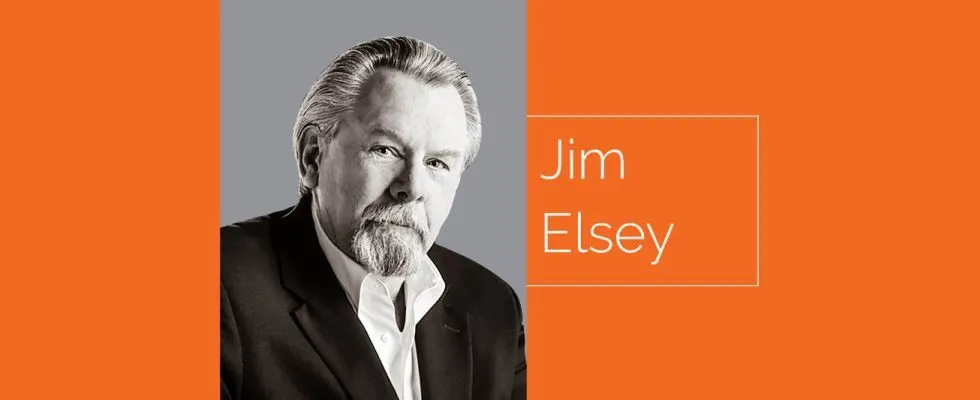
Due to the increased viscosity at cold temperatures, the negative effects on centrifugal pump performance are dramatic. If you are pumping cold water, viscosity is not a problem, but cold transformer oil is a whole different matter.
Background
Large power transformers (defined as those rated above 200 mega volt amps (MVA) and voltages typically above 120 kilovolts [kV] and up to 760 kV) are sometimes required to startup in freezing weather conditions. The cold startup situation most often occurs during an emergency, usually due to a winter storm or severe cold front.
Transformers in this class will employ circulating pumps to move the dielectric oil through the windings and heat exchangers in lieu of utilizing natural circulation. Some power transformers may have as many as 26 pumps installed. The cold startup scenario is especially critical for mobile transformers in the larger classes due to their concentrated geometry (power output per size). The consequences of operating the transformer pumps with oil temperatures below minus 10 C (+14 F) are not normally addressed by the transformer manufacturer, which is the main purpose of this column.
Transformer Oil Pump
The allowance for oil leaks on transformers is none (zero tolerance), so the pumps are sealless wet motor pumps (aka canned pumps). As a consequence of this design, the bearings are lubricated by the pumpage. Despite the fact that the pumped liquid is “oil,” note that all of the lubrication properties were purposely removed in the formulation process to enhance the required dielectric properties. The lack of liquid lubricity is the main reason I specify hydrodynamic fluid film bearings for these applications, and I do not recommend the use of antifriction (ball) bearings that some other manufacturers utilize.
During cold weather, with the transformer offline, the oil temperature decreases and the viscosity increases. Consequently, the head, flow and efficiency of the pump will be diminished. Of these three factors, the efficiency is diminished the most, so the required power for the pump to operate will increase.
Precautions affecting high motor amperage, breaker sizing/loading and other operational parameters must be practiced when operating the pumps at lower liquid temperatures. Review of the speed-torque curve would be prudent to ensure the motor is capable of coming up to full speed. If the transformer was already in operation and at normal internal operating temperatures, the drop in ambient temperature would not be an issue even down to negative 40 degrees (C or F).
Centrifugal Pump Performance Is Affected by Viscosity
One major disadvantage of a centrifugal pump is the marked reduction in efficiency when handling viscous liquids. I often refer to viscosity as the kryptonite for centrifugal pumps. Viscous liquids have a negative and weakening effect on centrifugal pump performance. The hydraulic inefficiencies and consequently the hydraulic losses that occur in all centrifugal pumps are largely due to the viscosity of the liquid.
The use of centrifugal pumps for liquid viscosities in the range approaching 600 centistokes (cSt) is generally not recommended because of the reduction in pump efficiency. However, in many commercial and industrial applications, the broad coverage range and high reliability of a centrifugal pump may still make it the best overall choice even when the viscosity exceeds these parameters.
Cost and reliability factors must be weighed in the overall evaluation. I have witnessed centrifugal pumps successfully applied where the liquid viscosity approached 2,000 cSt. I am aware of applications with even higher viscosities.
To ensure pump reliability and sustainability, you must have input from the manufacturer on allowable shaft torque and horsepower limits, usually expressed as maximum allowable brake horsepower (bhp) per 100 rotations per minute (rpm) limits. There will also be power frame bhp limits and, in rare cases, torque limits on impeller vane loading. A thorough cost analysis is strongly recommended with a specific focus on the required operational energy requirements. I always recommend reviewing the application with the pump manufacturer or an experienced pump engineer.
Viscosity
Viscosity is a measure of a liquid’s resistance to flow at a given temperature. You can also think of it as liquid friction. A technical definition would explain viscosity as a force required to move a hypothetical liquid plane (think plate) of some defined unit area over a defined distance placed above a stack of planes of equal area—all in a defined time period. I often define viscosity as a fluid’s resistance to pour or a resistance to be pumped against. Note this column addresses the pumping of liquids, not dual phase fluids or gases.
Viscosity is usually expressed in either absolute or kinematic terms (absolute viscosity is also often referred to as dynamic viscosity). The absolute viscosity of a liquid is defined as the resistance to flow and shear under the forces of internal friction. The internal friction is caused by the resistance of the liquid’s molecules moving relative to each other. On the other side of the explanation is kinematic viscosity, which is a measure of a liquid’s resistance to flow and shear under the forces of gravity.
A simpler way to explain the difference is kinematic viscosities are timed flow rates through orifices where the driving force is typically gravity, while dynamic (absolute) viscosity is a measurement of the force required to overcome fluid resistance to flow through a tube (capillary). The easiest way to understand is kinematic viscosity is a measurement of time and dynamic viscosity is a measurement of force.
Units
The base unit of kinematic viscosity is the stoke, and one square meter per second is equal to ten thousand stokes. Since this unit is large and cumbersome, it is common to use square millimeters per second [(mm)2 ÷second ] or cSt.
The base unit of dynamic viscosity is the centipoise (base unit is poise). The relation between the two is expressed in Equation 1.
Equation 1) Centistoke = centipoise ÷ specific gravity
Transformer Oil
Transformer oil is typically formulated from mineral-based oil but can also be natural ester or silicon. All of these oils possess Newtonian properties. That is, the shear rate is linearly proportional to the shear stress. Further, the viscosity of a Newtonian fluid depends solely on the temperature and does not rely on the shear rate or the factor of time. There is an indirect relationship between the liquid temperature and the viscosity. As the temperature increases, the viscosity decreases and vice versa. The aforementioned properties remain true for all transformer oils, whether mineral-, silicon- or ester-based.
Transformer oils are designed for numerous purposes, but the two most important ones are the transfer of heat and as a dielectric (insulation with arc suppression capabilities). Transformer oil is designed to perform at the high temperatures encountered in an operating power transformer, frequently in the range of 60 C (140 F) and approaching 90 C (194 F).
Pump Performance Calculations for Viscous Liquids
The deleterious effects of viscosity on centrifugal pump performance have been studied for well over 100 years and can be predicted with a fair amount of accuracy based on empirical and test data—usually within 5% accuracy. The Hydraulic Institute (HI), in conjunction with prominent pump manufacturers and a few end users, have extensively tested centrifugal pump performance on viscous liquids. Note that it is still not an exact science. Most of the calculations and results can be summarized in a published standard (ANSI/HI 9.6.7: 2021, titled Rotodynamic Pumps Guideline for Effects of Liquid Viscosity on Performance).
Performance Corrections for a Typical 4x4 Transformer Oil Pump (OH9)
I recently calculated a fundamental estimation of pump performance on a typical transformer oil pump over a range of cold temperatures. For these calculations, I had to make several assumptions that affect the overall accuracy of my results, but not the general scale/magnitude of the effects (see chart). There is no overall predictive correction factor, and the level of uncertainty is within 5%.
Assumptions:
The original performance curve is based on performance with a mineral-based transformer oil at a temperature near 21 C (70 F).
Natural ester- and silicone-based oils were also considered, but this doesn’t change the net outcome.
The pump efficiency is approximately 70% at the best efficiency point (BEP) for this pump. Based on previous knowledge and assumptions of Reynolds number, a specific speed (Ns) range is normally used for these applications and bhp calculations.
The viscosities used for each temperature are based on collected data from alternate but reliable sources. Your oil may have slightly different viscosities at these temperatures.
I used two methods and averaged the two for results (old and new methods).
I used 0.88 for specific gravity.
I did not complete a calculation for the oil at minus 40 C because I did not have reliable data for the oil properties. Further, the obvious extrapolation from minus 20 C is that the pump efficiency would approach a very low number as to be essentially inefficient and require a high amp load on the motor.
Based on the performance curve shape (slope) and assumptions as to specific speed, blade entrance and exit angles and number of blades, I assumed the BEP was at 500 gallons per minute (gpm) (Q) and 45 feet of head (H).
When the transformer oil temperature drops from plus 60 C to minus 20 C, the pump efficiency in the mid-range drops from 70% to 19% (decrease of 51%), and the required motor horsepower increases from approximately 7 to 19 bhp (difference of 12 bhp increase or a factor of 2.7).
On a given power transformer, the pumps and heat exchanger fans may be able to operate at temperatures below normal, but it is not always a prudent decision for the sustainability and safety of the transformer.
Standard guidelines for energization of power transformers and ancillary equipment at cold temperatures are covered in IEEE C57.12.00 (Institute of Electrical and Electronics Engineers), where liquid temperatures below minus 20 C (minus 4 F) are considered as “unusual service.”
Also refer to IEEE Std C57.93-2007 installation and maintenance guide for transformers and guidelines from the transformer manufacturer, as suggested by the Conseil International des Grands Réseaux Electriques (CIGRE), a global community committed to collaborative development and sharing of end-to-end power system expertise.
Some transformer manufacturers allow startup and operation of their transformer oil pumps with oil temperatures at or near minus 40 C (minus 40 F), but it should be pointed out that the supplied motors, conductors and breakers (set at high trip settings) are greatly oversized, which raises the questions of efficiency and efficacy sacrificed during normal operations.
On cold startup, most transformer oil pumps have a design safety margin for the shaft and impeller that is more than adequate to handle the increased torque. At these low liquid temperatures, the real question becomes, “Are the motors and associated breakers properly sized for the increased loads encountered at the lower liquid temperatures—especially below the range of minus 10 C to 15 C?” Another question is, “Will the oil flow properly in the internal motor passages and bearings?”
I recommend letting the transformer warm up the oil before starting the pumps.
References
“Viscosity Effects”, Pumps and Systems, November 2017 Jim Elsey
“Pumping Viscous Oils with Centrifugal Pumps.” Oil and Gas Journal, May 1940 A. J. Stepanoff
“The influence of viscosity on centrifugal pump performance” ASME, Vol. 68 (1946), pp. 823-848 by A. T. Ippen
“Understanding Uncertainties in Viscous Performance Predictions for Centrifugal Pumps” TAMU 2020 / Scott Lang, Stefan Berten, PhD, Hemanth Satish, PE