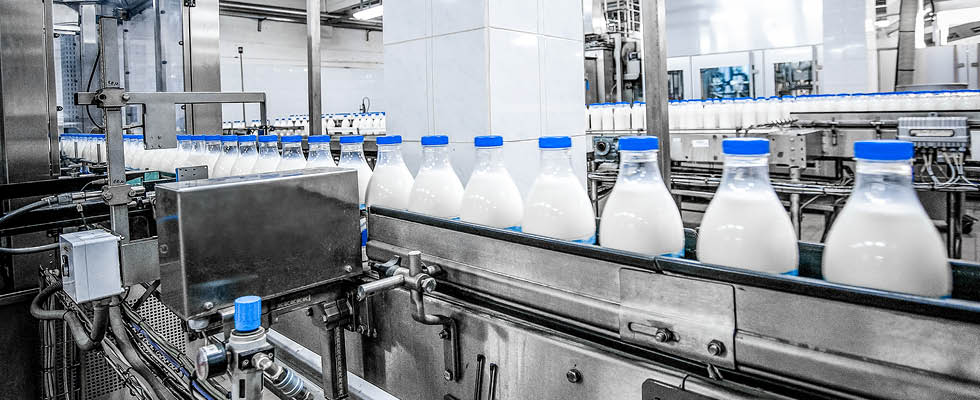
From pasteurization to milk bottling, the dairy industry has come a long way since it first introduced wider-scale processing systems to its production in the 1800s. Yet, many of the reasons behind this introduction are the same: cleanliness, efficiency and quality control.
Today, processors have intricate systems and components, like sensor-monitored valves or precise metering pumps, for every stage of the journey. Many traditional dairy manufacturers have added plant-based capabilities to their production arsenal, using a different set of equipment in the same factory premises or building a totally new facility dedicated to plant-based products. Each process line needs equipment with high-end innovation, sustainability and the highest degree of utilization. Choosing the right equipment for a dairy processing plant is essential, and it becomes even more critical when a brand is expanding into new product segments like plant-based products, which should be nutritious and tasty.
As the industry evolves—whether it is new products, protein sources or production methods—new technologies only multiply the benefits. Equipment manufacturers not only innovate to keep their users on the cutting edge, but they also aim to stay one step ahead.
Users demand top quality and consistency. The businesses manufacturing the product require ease of production, safety, cost-effectiveness and energy efficiency. The only way to deliver on both groups’ goals is to deploy the latest innovative ideas in processing equipment across every aspect of dairy and plant-based systems.
Sustainability: Optimizing for Efficiency
Sustainability and efficiency go hand-in-hand. Many companies are pledging sustainability commitments, including setting deadlines for carbon reduction. Sustainability is not just about emissions. Energy consumption, waste management and water consumption also play a role. While sustainability is one factor users may use to choose a company to support, it can also help the bottom line beyond securing environmental benefits—a commitment to sustainability can lead to lower costs, better maintenance and longer runtimes.
For example, the mixproof valves, which help with separation of product and cleaning solutions in the dairy and plant-based processing system, can play a role in waste management, including minimizing water and chemical loss and avoiding additional waste management expenses.
Technologies like variable speed drives, which allow pumps to operate at the exact flow rate and pressure required for their specific application, help plants with energy efficiency. Today’s leading manufacturers are offering more options to help cover the differing needs of the industry—whether it is new products or sources, like dairy alternatives. Ensuring the components are sized adequately for their specific purpose helps maximize energy efficiency and optimize the cleaning process.
Quality Control
Quality and consistency in food and beverage production often means finding the right combination of parts for specific needs while ensuring those same components are reliable.
That starts with pumps and valves, which control the flow and pressure of the product throughout the processing operations and thus are critical to maintaining consistent product quality. The high temperatures required by pasteurization necessitate unique system designs, including hygienic values. Additionally, pumps and valves are crucial to products that require sterilization, such as high-temperature short-time milk.
Other aspects affecting manufacturers’ pump and valve needs are the products’ acidity, solid content and viscosity. Valve selection will vary in elastomer selection, valve size and stroke capability. Equipment must be designed with its purpose, regulations and cleanability in mind. The type of product will determine the needs. For example, a more viscous production, like yogurt, demands pumps and valves that will maintain the product’s consistency, texture and body.
With such a range in component needs, equipment manufacturers continue to improve the selection and ranges for both pumps and valves, so every processor has access to the precise selection they need.
Cleaning & Regulations
The dairy industry has some of the highest regulatory requirements of any industry across a wide range of areas. From food safety to environmental regulations to sanitation, manufacturers can stay in good standing with regulators by using top-quality pumps and valves. End users must ensure their valves comply with 3-A and Pasteurized Milk Ordinance (PMO) design standards for the United States dairy market.
Clean-in-place (CIP) systems ensure a quality, safe dairy product. A plant with maximum uptime and the shortest possible cleaning cycles is the most efficient. New CIP technologies, like updated aseptic and hygienic pigging systems, continue to emerge to serve brand-new product lines, like plant-based and fermented foods. Not only do they help with cleaning the system, they save the manufacturer raw materials and reduce waste. Depending on the running condition of the plant, the latest pigging technology could reduce water usage by 60% to 70% and recover up to 97% to 99% of valuable product.
Innovation is not just seen in pumps and valves as a whole. Parts needed to maintain these components also continue to evolve. By choosing OEM components, businesses can ensure they get the best parts to fit specific needs without sacrificing or hindering functionality, cleanliness or operations.
Usage, Reliability & Maintenance
Automation is one of the biggest drivers of technological advances in equipment and components. Many of the latest systems can include IO-link or other automation technologies for pumps and valves. Providing real-time diagnostics regarding the health of the valves helps to eliminate unplanned downtime, which can yield lost product.
Automation also takes the imprecision out of manual operations. Systems can be set to specific setpoints with fewer errors, optimizing the plant’s heating, cooling and overall energy usage. The latest technology in valves can include position sensors, which allow end users to be notified with warnings if they become blocked unexpectedly. The valve usage parameters can be set to provide notice when they have reached a certain number of hours or cycles or are running slower than expected. Ultimately, these tools lead to good maintenance and, in turn, better planning. Knowing which spare parts are needed and when to plan maintenance means fewer surprises.
The milk and plant-based beverage industries are here to stay, but they need constant innovation to thrive. Exciting, groundbreaking technologies are always around the corner. It is vital processors and equipment manufacturers work together. Just as many companies started in dairy before expanding into plant-based alternatives, manufacturers are in the same boat. They continue to look for new ways their equipment can better serve this growing sector.
Companies should seek out experience, expertise and innovation in equipment partners. Otherwise, they risk being left behind in a fast-moving marketplace.