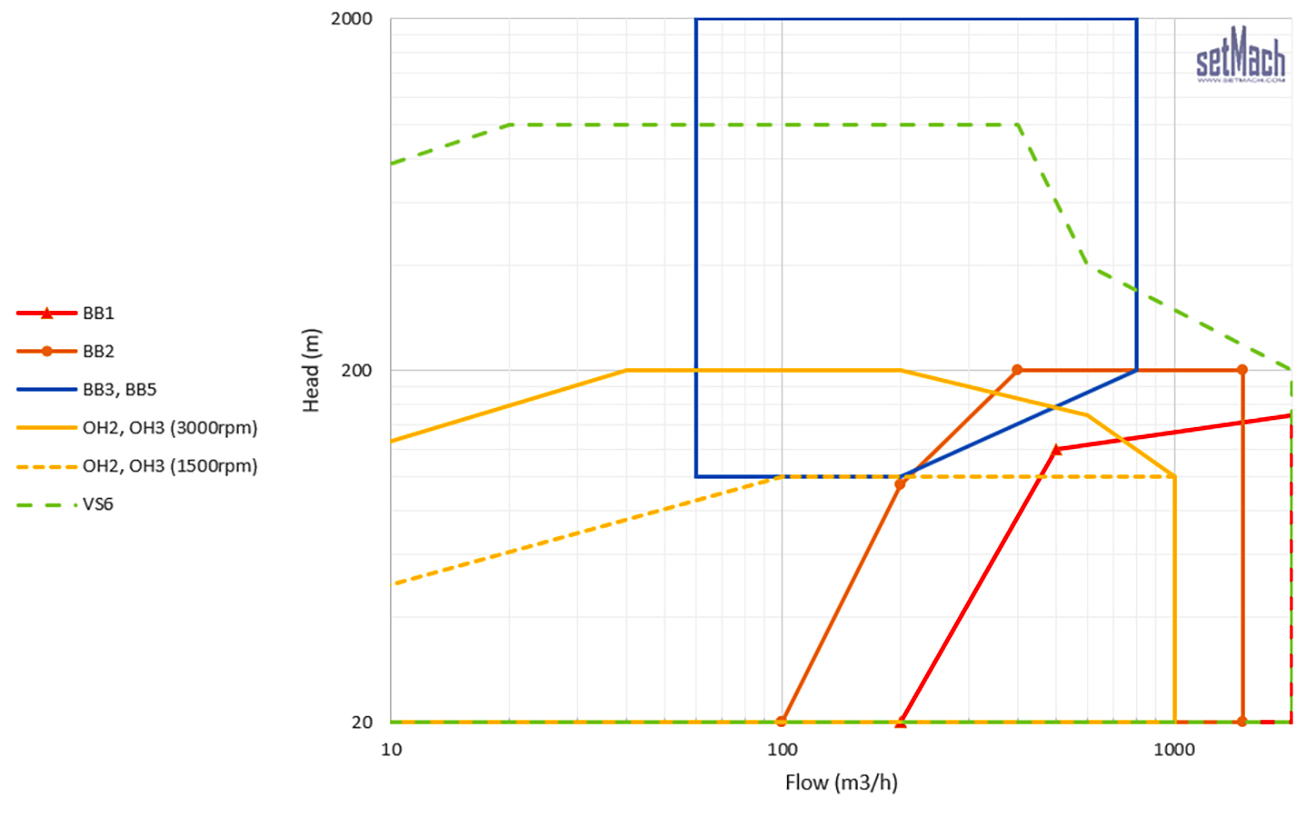
To ward off having to struggle with unreliable vertical process pumps, reliability-conscious users are encouraged to investigate (and aim for) pumps with the lowest life cycle cost. Attractive life cycle costs will steer reliability-focused best-in-class (BiC) users toward readily available and reliable vertical pumps. These pumps cover a wide range of heads (translatable to pressures) and flow rates (Image 1).
But, life cycle cost improvements are most easily achieved by going beyond merely upgrading the hydraulic end of process pumps. Improvements to the pump’s mechanical end can also yield impressive benefit-to-cost ratios.
Literature shows fine-tuning of pump hydraulics has been emphasized in the past five decades and has borne fruit. However, the same cannot be said for the mechanical or drive end of vertical pumps. Here, routine upgrades have been largely confined to the BiC pump user community. Many BiC users have found that the results of many upgrade measures meet or exceed the desired pump run length improvement goals and that the incremental cost of such upgrading is usually retrieved within a short time span. Chances are that the pursuit of such upgrades contributed to BiC pumps becoming top performers.
Some reliability professionals at BiC facilities use an experience-based rule-of-thumb multiplier. This multiplier simply states that a proven upgrade is likely to extend a pump’s uninterrupted run time capability by 20% or more.1 As just one of many examples, pumps with O-rings that risk being pinched during operation (Image 2) are thought to benefit from upgrading to products where this vulnerability does not exist (Image 3). The rule of thumb then assumes a 1.2-times run length extension for the first upgrade, and again a 1.2-times multiplier for the next upgrade.
Four simple upgrades would extend pump run lengths by 1.44 or perhaps more. The resulting maintenance cost avoidance is significant. The incremental cost of most upgrades is modest, and payback in most cases meets, or comes in below, the generally realistic expectation of less than six months.
Upgrading Mechanical Components
Generally, reliability-focused owner-operators of vertical pumps look for opportunities to combine their next repair event with judicious upgrading. Repeatedly repairing to the as-before status can be a recipe for continued unreliability of failure-prone vertical pumps. In pumps that incorporate the column bearings (Image 4), upgrade justifications are dependent on the observed rate of wear. In many such cases, column bearings have been upgraded to carbon-filled polyfluoroalkyd.2
Better bearings are available. Typical column bearings are sandwiched between two column flanges. A two-piece split tapered bushing secures two keyed shaft ends in place; a single-piece tapered sleeve fits over the two-piece split tapered component. Thrust bearings and associated lubrication are also important upgrade subjects. In particular, oil mist-lubricated rolling element thrust bearings have given better life. After passing through a back-to-back oriented set of ball bearings or a tapered roller bearing, coalesced oil mist droplets (erroneously called “excess oil mist”) exit from a drain port. In modern plantwide closed-circuit oil mist systems, the coalesced oil droplets are captured and reused.1
Although vertical pumps are ideally suited for multistage (high differential pressure) services, many vertical pumps are of single-stage design. They incorporate an end suction back pull-out type casing with the hydraulic end mounted below the liquid level. The impeller is connected to the motor by means of an extended shaft. The shaft is housed and supported in a rigid tubular intermediate pipe.
As a rule, vertical pumps in important hydrocarbon processing services are designed to the requirements found in an American Petroleum Institute (API) standard, API 610. User-purchasers view adherence to the standard’s stipulations as a powerful risk reduction step. API-compliant equipment incorporates considerable experience-based content derived from reliability-focused users. While equipment cost is always a concern, companies should aim for and achieve proper balance between initial monetary outlay and long-term reliability. In many cases, life cycle cost studies show significant advantages for API-compliant pumps over their lower-priced non-API competitors.
Lubricants & Lube Application
In cryogenic temperature environments and where dual seals are used, a low pour-point synthetic lubricant can be a good barrier fluid. Many bearing manufacturers agree that an oil spray or mist introduced into the bearing cage (the ball separator) is the most desirable lubricant application method. Oil spray or mist reduces the risk of overheating. Skidding bearings are of primary concern in pump geometries where several rolling element bearings are assembled as a stack of two or more bearings.
Because mechanical seals can be the weakest link in many pumps, seal upgrading in vertical pumps can be a highly relevant step toward maintenance cost savings and improved safety. Cartridge-style duals are among the most popular and readily cost-justified seal upgrades. It follows that BiC companies have standing procedures to view maintenance interventions as triggers for upgrades. Many are helped to achieve these goals by partnering with progressive independent pump rebuilders.3
Progressive pump rebuilders cooperate with pump users to define the payback for combining pump repairs with pump upgrading. Their input is often based on decades of experience and an intimate knowledge of the pump owners’ operating culture and spending philosophy. The best pump rebuilders freely part with a good portion of the pump wisdom they have acquired from working with customers or clients around the world.4 Working with a competent pump repair/redesign shop ensures the pump owner that technically superior configurations and realistic economics remain in balance.
A side benefit is derived from such cooperative efforts: the owner-purchasers can incorporate available upgrades in their future procurement specifications for new pumps. Without a good purchase specification for pumps and other fluid machinery, the buyer signals that price is the primary selection criterion.
Deficient signaling has resulted in least-cost, often unreliable vertical centrifugal pumps finding their way into petrochemical plants and oil refineries. If users have vertical process pumps with run times not reaching 36 months, they may have genetic deficiencies that make them prime candidates for upgrading or even replacement with well-proven designs.
References
1. Bloch, Heinz P.; Ehlert, Don; Geitner, Fred; “Optimized Equipment Lubrication, Oil Mist Technology, and Storage Preservation,” (2020), Reliabilityweb.com, Ft. Myers, Florida, ISBN 978-1-941872-98-7
2. Bloch, Heinz P., “Fluid Machinery: Life Extension of Pumps, Gas Compressors and Drivers,” (2020), DeGruyter Publishing, Berlin/Germany, ISBN 978-3-11-067413-2
3. Bloch, Heinz P., “Petrochemical Machinery Insights,” (2017), Elsevier Publishing, Oxford (UK) and Cambridge, Massachusetts, ISBN 978-0-12-809272-9
4. Bloch, Heinz P., “Pump Wisdom: Problem-Solving for Operators and Specialists,”
(2012), John Wiley & Sons, Hoboken,ISBN 978-1-118-04123-9